Three-dimensional (3D) metallography is the science and art of studying the microstructure of metallic components in a non-destructive manner. The method involves the creation of a 3D map of the structure and determination of the 3D coordinates of the atoms within the structure, which allows for the observation, analysis, and visualization of the 3D microstructures of metallic components. This article introduces the concept of 3D metallography and its applications in the scientific and industrial sectors.
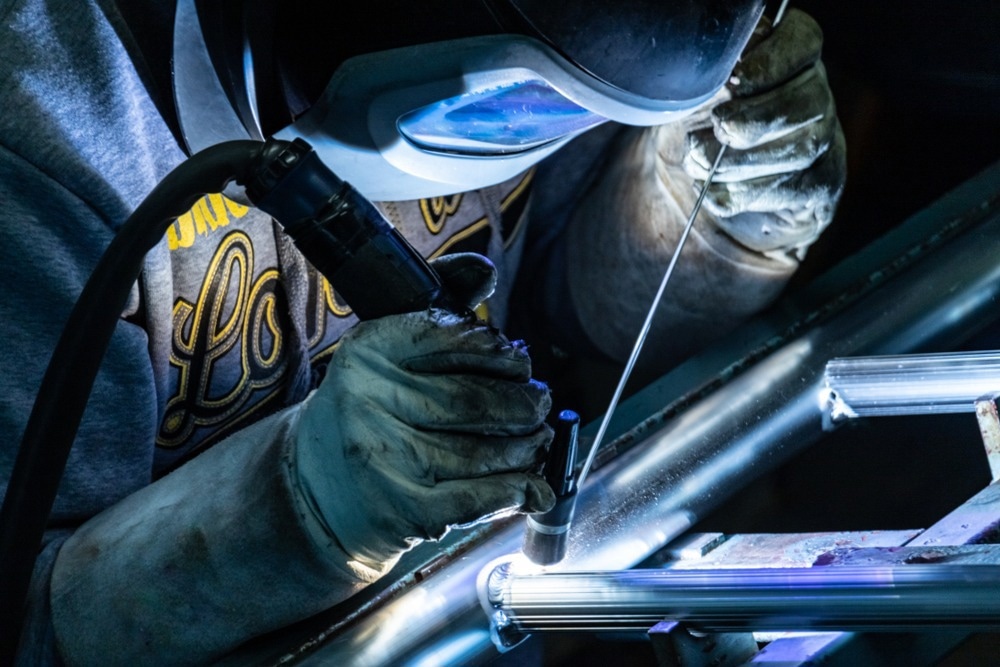
Image Credit: Kocsis Sandor/Shutterstock.com
What is Metallography?
Metallography is the science of using microscopic techniques to examine sections or polished surfaces of metallic materials. It provides information about a metallic component’s composition, microstructure, corrosion level, and production methods of a material.
This technique was initially employed in archaeology in the early 20th century, and has proven to be a valuable tool for archaeologists. By studying metallic materials, archaeologists gained insights into how these materials were used and valued in the past and the processes involved in extracting them from ore and transforming them into finished artifacts.
Metallurgical investigations involve methods such as image processing, microscopic examination, and chemical assessments to evaluate the grain size, microstructure, defects, and historical aspects of metals.
3D Metallography in Microstructural Analysis
Material science is the central principle governing the microstructure of a metal component that influences the performance and properties of the material. Hence, characterizing the microstructure of a material quantitatively and representing it mathematically is of considerable importance in material science.
Because material structures are in a 3D form, studying their 3D microstructural geometry is crucial. Owing to the opacity of metals, microstructural observations are generally made on two-dimensional (2D) metallographic sections.
However, a 2D metallographic section does not contain all information regarding the true 3D microstructural geometry. Therefore, the development and application of techniques for the reconstruction, visualization, and direct quantification of opaque 3D microstructures, known as 3D metallography, are of significant interest.
The microstructural features are unique because of their stochastic nature, and neither the two fields of view nor the two particles or grains within a field of view are exactly alike. These features often have complex morphologies, and their locations and orientations can be non-uniform.
Spatial clustering and correlations frequently exist between microstructural features. Thus, reconstructing 3D microstructure volume segments with high resolution and large volumes is desirable for understanding the complexity of a microstructure.
The microstructural features observed in a metallographic section are the points where the features of the 3D structure intersect with the plane of sectioning. Consequently, in the metallographic plane, volumes such as grains, voids, and particles appear as areas, whereas surfaces such as the grain boundaries and precipitate interfaces appear as lines.
Recent Studies
A study published in the Journal of Thermal Analysis and Calorimetry analyzed the traits of melt marks resulting from short circuits and fire-induced accidents in copper-core PVC-insulated single-core flame-retardant wires.
Here, an electrical fault simulation experimental device was used to simulate both primary and secondary short-circuit faults, and a gasoline torch was employed to replicate high-temperature fire conditions.
Employing a metallurgical microscope and Image-Pro-Plus software, the examination was conducted to evaluate the grain and pore size and shape, as well as the metallurgical organization characteristics of the melt marks, under various conditions.
The results indicated that the primary short-circuit melt traces displayed fine grains with an average diameter of 13.14-17.87 μm, primarily found in the 0-800 μm2 area. These grains were dominated by dendrites with fine grain boundaries and an excitation-layer structure. They had fewer pores and a regular shape, and were mainly concentrated in the 0-1500 μm2 region.
The secondary short-circuit fusion trace grains were predominantly composed of columnar and cytosolic grains with an average diameter of 15.72-22.30 μm. They were largely concentrated in an area of 200-1200 μm2 and had sparse and coarse grain boundaries. Additionally, they had a greater number of pores, a larger volume, and irregular shapes, primarily found in the region of 1000-3500 μm2.
The fire fusion marks revealed the presence of coarse grains, primarily composed of equiaxed crystals, with an average diameter of 16-28 μm and a grain area concentrated within 600-1800 μm2.
The surface layer of the fusion marks exhibited only small pores and fewer internal pores and shrinkage holes. The findings of this study contributed to the identification of physical evidence related to electrical fires and the determination of the cause of fires.
Another study published in the Journal of Materials Research and Technology examined how the morphology of the grains and α+β textures affected the anisotropic mechanical characteristics of a two-phase titanium alloy billet that was processed using β forging.
The 3D metallographic morphologies were observed using an Axiovert 200 MAT optical microscope (OM), and the high-magnification microstructure was characterized using a MIRA3 scanning electron microscope (SEM).
The alloy billet displayed a distinct macro streamline that ran parallel to the radial direction, as well as a microscopic basket-weave structure. The yield strength and elongation of the specimen in the radial direction were both greater than those of the compression direction specimen. This anisotropy in strength is attributed to both fine grain and texture strengthening. Meanwhile, plastic anisotropy was influenced by the normal stress acting on the crack propagation plane.
The relationship between the tensile properties and fracture toughness was evident, and the internal and external contributions to the fracture toughness in various orientations demonstrated that external toughening also holds significant importance.
The R-C specimens exhibited superior crack-initiation and growth toughness, which was attributed to their dominant elastic toughening mechanism. The proportion of plastic components progressively increased with the propagation of cracks.
The differences in the fracture toughness between the three orientations were clear. The intrinsic toughness, which was determined by the high strength and high modulus, played a dominant role in the fracture toughness owing to the effect of the two-phase texture. This resulted in the high toughness of the R-R and R-C specimens. Moreover, the elongated β grain arrangement positively affected the extrinsic toughness, mainly through delamination and crack deflection.
Conclusion
Overall, the use of 3D metallography has greatly improved the field of structural analysis by providing in-depth information about the microstructures of metallic components. Through advanced microscopy techniques, metallographic examination uncovers intricate details that are essential for the evaluation and quality assessment of materials, as well as for enhancing the accuracy of engineering processes.
More from AZoM: Mechanical Properties of Steel in High-Stress Environments
References and Further Reading
Wang, W et al. (2023). Study on quantitative metallographic analysis method of copper wire melt trace under short-circuit and fire conditions. Journal of Thermal Analysis and Calorimetry, 1-14. https://doi.org/10.1007/s10973-023-12527-0
Brätz, O., Henkel, KM. (2023). Investigations on the microstructure of drawn arc stud welds on structural steels by quantitative metallography. Weld World, 67, 195–208 . https://doi.org/10.1007/s40194-022-01417-y
Scott, D. A. (2014). Metallography and microstructure of metallic artifacts. Archaeometallurgy in Global Perspective: Methods and Syntheses, 67-89. https://doi.org/10.1007/978-1-4614-9017-3_4
Gokhale, A. M., Singh, H., Mao, Y., Zhang, S., & Gurumurthy, A. (2010). Three-Dimensional Metallography for Visualization, Characterization, Modeling, and Simulation of Three-Dimensional Microstructures. Microscopy and Microanalysis, 16(S2), 714-715. https://doi.org/10.1017/S1431927610063105
Disclaimer: The views expressed here are those of the author expressed in their private capacity and do not necessarily represent the views of AZoM.com Limited T/A AZoNetwork the owner and operator of this website. This disclaimer forms part of the Terms and conditions of use of this website.