Fine chemicals serve as the model example for precision and purity. They are characterized as extremely limited chemicals produced in quantities less than 1,000 tons per year, but doing so is an expensive enterprise, as they cost over $10 per kilogram to produce.
The proportionally low yield, high expense nature of fine chemicals manufacturing is due to the complex synthesis routes involved in production. Plants are generally multipurpose facilities that produce fine chemicals in multistep processes. These systems are subjected to rigorous protocols to meet the required specifications to ensure ultrahigh purity levels.
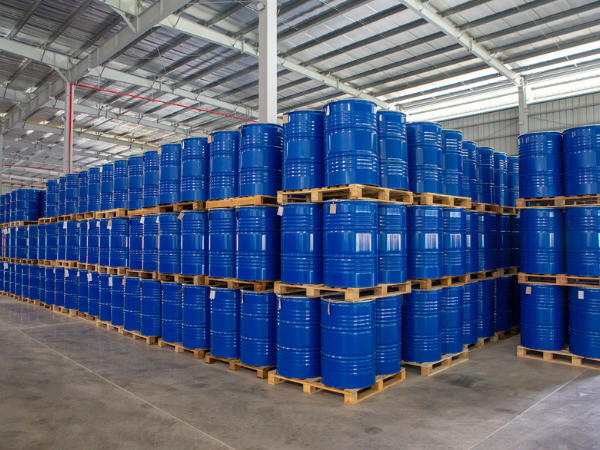
Image Credit: Powder Systems
Understanding the Importance of Yield
Purity is at the core of fine chemical synthesis as these materials provide the basis for developing more complex, specialty chemicals custom-made for specific end uses. They are usually found in active pharmaceutical ingredients (APIs), alkaloids, biocides, peptides, proteins, etc. Despite the disproportionate cost-to-yield ratios, total global production of fine chemicals often exceeds $85 billion annually.
Yield is a key factor in any form of synthesis as it is a marker of the efficiency of processes and chemical reactions, which determine the quality of a given product.
Low yields may signal process inefficiencies and defects, including impure starter material. On the other hand, high yields demonstrate improved resource efficiency and high-quality products. Of course, the primary aim of fine chemical synthesis is to produce materials with impeccable purity, but maximizing throughput is an appealing prospect too.
Improving system efficiency can help manufacturers reduce production costs, which in turn boosts margins. It can even lead to greater product quality. Yet, this process can present significant challenges. Achieving high yields demands a deep understanding of reaction kinetics, acquiring the right equipment, and integrating appropriate purification methods.
There are several strategies to improve yields in fine chemicals manufacturing, as listed below:
Reaction Kinetics: Diving into reaction kinetics can lead to greater yields. It is about knowing how to fine-tune certain components in the process, such as finding the right temperature, the optimal pressure, and the perfect reactant concentrations.
Equipment and Purification Methods: Yield enhancement depends on more than just the reaction; the tools of the trade are just as essential. Using high-quality raw materials, rigorous equipment maintenance, and refining purification methods all have a part to play.
Identification and Mitigation of Potential Challenges: Generating high yields is not the main issue, the challenge is quality. There are many challenges, from byproduct formation to impurity generation and reaction optimization. Yet, being able to identify challenges means mitigation strategies can be employed, and therein lies the key to optimizing the yield.
There is no leeway in fine chemical manufacturing, and errors must be eliminated. Intermediate chemicals are subjected to rigorous evaluation regarding purity, particle size, and moisture content. The industry can continually improve its standards and unlock new yield levels with strategic implementation and vigilant monitoring.
Filter Dryers – The Unsung Heroes of Yield Enhancement
Several different pieces of equipment are involved in the complex, multi-step synthesis of fine chemicals. The question is, why are filter dryers considered to be so special?
Isolation of Solids with ANFD
The Agitated Nutsche Filter Dryers (ANFD) by PSL are considered near-indispensable equipment in fine chemical manufacturing. Designed specifically to address a variety of applications from the laboratory to commercial production, ANFDs are proficient in the isolation of solids during batch processing.
A combination of pressure, vacuum, and agitation methods within a contained vessel are brought together throughout the process. This facilitates the effective separation of the solid product from its solvent.
Efficiency in Drying
Drying is just as vital as isolation for enhancing yield. Powder Systems’ filter dryers have a heated filter plate that directs heat energy directly into the product cake. This design makes drying efficient, outperforming conventional methods like Büchner filtration and oven tray drying.
Adaptable Filter Dryers
Nutsche filter dryers by PSL can be distinguished by their versatility. They are suitable for use in a variety of processes, including pharmaceuticals, precious metals, and natural extraction. Their seamless design means they can easily be incorporated into a range of fine chemical manufacturing processes, making them an indispensable asset.
Combining Solid-Liquid Separation, Product Washing, and Drying in a Single Equipment
One of the main advantages of an Agitated Nutsche Filter Dryer (ANFD) is its capability to perform solid-liquid separation, product washing, and drying in a single unit. This groundbreaking design simplifies the fine chemical manufacturing process and minimizes product transfers, mitigating the risk of product loss while boosting overall yield.
The ANFD efficiently isolates the solid product from its solvent during the solid-liquid separation step, ensuring high purity and recovery. A heated filter plate and agitator support effective drying, outclassing conventional methods like Büchner filtration and oven tray drying. The agitator also plays a key role in product washing, facilitating dynamic washes under temperature control conditions, if required.
By bringing these features into a single unit, PSL’s filter dryers meet the highest standards of safety and quality and follow various key industry practices, directives, and regulations, including cGMP, ATEX, and 21 CFR Part 11.
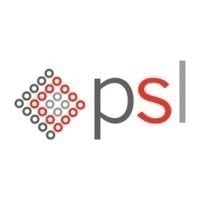
This information has been sourced, reviewed and adapted from materials provided by Powder Systems.
For more information on this source, please visit Powder Systems.