The GFD®Lab is an effective benchtop Agitated Nutsche Filter Dryer (ANFD) for laboratory solid-liquid separation procedures. It is a small-scale version of PSL's production ANFD filter dryers, offering the same benefits and reliability for efficient filtration and drying.
GFD® technology is specifically engineered to address common obstacles manufacturers encounter when utilizing conventional production techniques like oven tray-drying and Büchner filtration. It is an effective option for executing scale-up and scale-down operations and acquiring predictive performance data.
An agitated vessel intended to operate in both vacuum and pressure is incorporated in the GFD®Lab. The vessel includes a heated jacket for effective drying and is available in Borosilicate 3.3 glass, 316L Stainless Steel, or Alloy 22. Solid-liquid separation is carried out within its unique filtering basket, which is removable to facilitate and maximize product recovery.
Research centers, labs, universities, and businesses from various industries are served by the GFD®Lab nutsche filter dryer. Around the world, scientists and process engineers use GFD® technology to help them create and optimize their specific processes.
Download the Brochure for More Information
Features and Benefits
Combined Filtration and Drying
Designed to adhere to Good Laboratory Practices (GLP) for regulated research and development activities, the GFD®Lab is an all-in-one filter dryer. It enables manufacturers and process developers to complete a variety of procedures using a single system:
- Solid-liquid separation via slurry filtration
- Product washing
- Re-slurry
- Vacuum drying
- Product sampling
- Product discharge
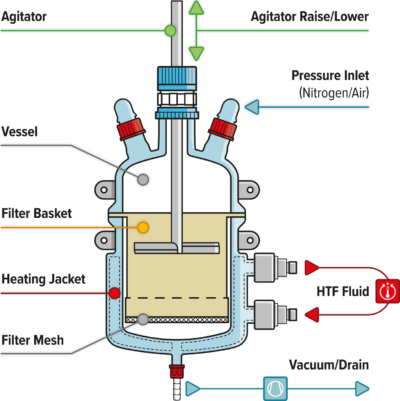
Image Credit: Powder Systems
Unrivaled Product Recovery
PSL appreciates the value of the desired product and therefore how essential it is to maximize product output to stay competitive in the industry.
The fundamental features of the GFD®Lab nutsche filter dryer address this essential need. After process completion, the unique filtration basket within the GFD®Lab vessel can be removed to retrieve the product batch.
The GFD®Lab basket enables fast and simple switching of filtering meshes made of different materials and pore sizes (Polypropylene, PTFE, 316LSS, Alloy 22, etc.), making multi-product applications possible.
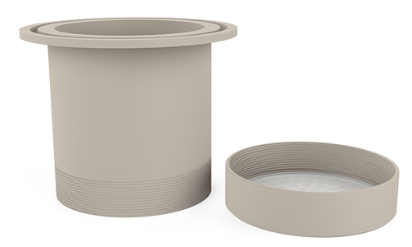
Image Credit: Powder Systems
Flexible Modular Design
With its modular design, the GFD®Lab is a unique agitated nutsche filter dryer that allows vessel sizes from the 010 and 050 series to be alternated without requiring a new base frame.
The base frame of every GFD®Lab model is also compatible with all vessel materials currently on the market, such as 3.3 borosilicate glass, 316LSS, and Alloy 22, to increase production flexibility further.
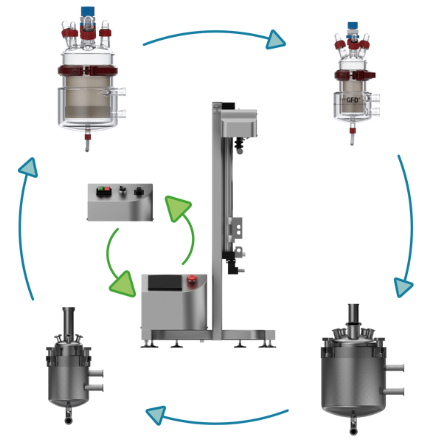
Image Credit: Powder Systems
GFD®Lab PLUS, Fast-Lane to Production
The GFD®Lab Filter Dryer can be upgraded to a GFD®Lab PLUS model by simply installing a new base frame to the current vessel, thanks to its unique modular design. Opting for this upgrade provides extra capabilities such as user automation of the GFD®Lab's controls, expediting development tasks.
- Digital display (HMI touchscreen)
- Straightforward user interface for speedy navigation
- Display of a process graph in real-time
- Sequences of the design process
- Optimize and save up to 99 process recipes
- Record and export process data
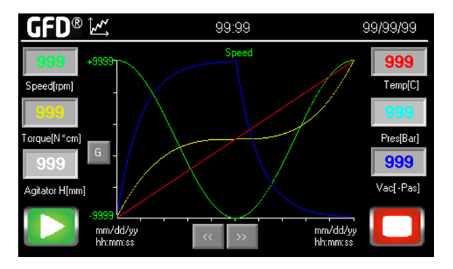
Image Credit: Powder Systems
Batch Reproducibility at the Touch of a Button
Users can create custom process sequences and optimize process recipes using the GFD®Lab PLUS to fit specific process applications.
With a push of a button, production can begin. Pre-designed recipes can commence with the preferred process parameters (temperature, duration, agitator speed/torque, pressure/vacuum, etc.), maximizing batch-after-batch replication and minimizing human error.
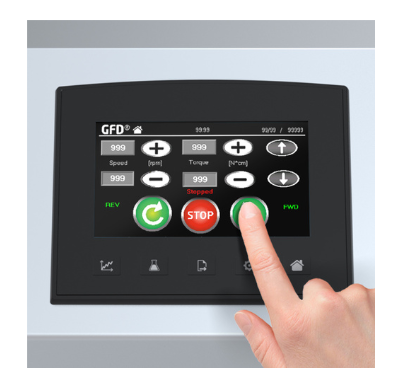
Image Credit: Powder Systems
Predictive Scale-up
Choosing the appropriate process technology throughout the R&D stage is essential for a scale-up to succeed. The GFD® Nutsche Filter Dryers from PSL are designed to make scaling up research and development easier.
This includes employing the GFD®Lab range for early R&D activities, and the GFD®Pilot option for GLP batches and pilot plant production levels.
It helps preserve important process objectives (like product quality, product yield, batch uniformity, etc.) and important production parameters (like filtering time, washing time, drying time, etc.) at every scale, which makes it ideal for completing scale-up and scale-down studies.
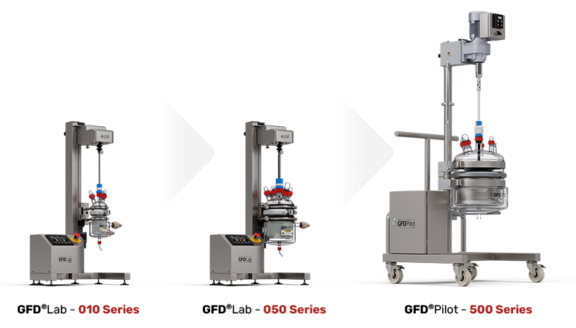
Image Credit: Powder Systems
Be Containment-Ready With the GFD® Filter box
PSL, one of the first developers of containment technology, created the exclusive FilterBox isolator line, which can effectively fit all GFD®Lab vessel sizes.
Choosing a GFD®Lab FilterBox ensures that the product is shielded from production settings and that operators are safe from the most potent and dangerous substances.
PSL also offers integration solutions for/with third-party containment providers.
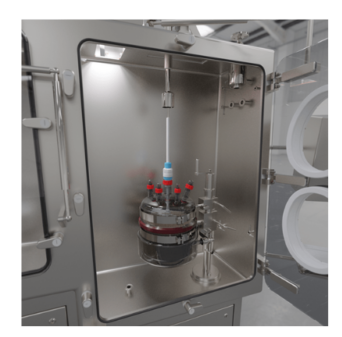
Image Credit: Powder Systems
Download the Brochure for More Information
Technical Overview
Applications and Options
Source: Powder Systems
|
GFD®Lab Vessel Sizes
|
|
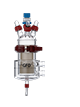
010 Series |
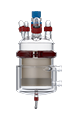
050 Series |
Typical Product Cake Volume (process-dependant) |
0.03 – 0.10 L |
0.18 – 0.50 L |
Vessel Volume |
0.3 L |
2.0 L |
Filtration Area |
0.002 m2 |
0.010 m2 |
Frame Dimensions (H x W x D) |
980 x 530 x 330 mm |
980 x 530 x 330 mm |
Source: Powder Systems
GFD®Lab Upgrade Options/Features |
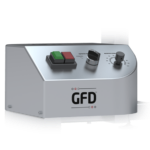
GFD®Lab |
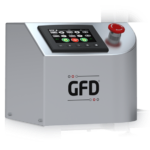
GFD®Lab PLUS |
Combined Filtration & Drying |
✓ |
✓ |
Removable Filter Basket |
✓ |
✓ |
316L or Alloy 22 Vessel |
✓ |
✓ |
Agitator Raise & Lower (R&L) |
Manual R&L only |
Automated R&L available |
Digital Display & Touchscreen |
✘ |
✓ |
Real-time Value & Graph Display |
✘ |
✓ |
Process Sequence Design |
✘ |
✓ |
Process Recipe Optimisation |
✘ |
✓ |
Process Data Recording & Exporting |
✘ |
✓ |