Agitated Nutsche Filter Dryers (ANFDs), such as the GFD®Pilot, are used in pilot and kilo-lab size solid-liquid separation operations. It makes proof of concept and feasibility studies made during smaller-scale phases of research and development easier. It offers the same quality, dependability, and efficiency as the full-size PSL ANFD filter dryers, yet is a smaller, more portable model.
The distinctive GFD® technology from PSL was created to solve the well-known production issues that manufacturers encountered while utilizing conventional production techniques like oven tray-drying and Büchner filtration.
The GFD®Pilot comprises an agitated vessel with pressure and vacuum capabilities. The vessel features a heated jacket for effective drying and can be fabricated with Borosilicate 3.3 glass, 316L stainless steel, or Alloy 22. The special filtration basket, which is removed to facilitate and maximize product recovery, is where solid-liquid separation is carried out.
GFD®Pilot technology is the logical step up from the laboratory-based GFD®Lab. Before going into commercial production, it helps develop and assess the intended final product.
Download the Brochure for More Information
Features and Benefits
Combined Filtration and Drying
The GFD®Pilot is an all-in-one filter dryer used at a pilot plant production scale. It is frequently used for applications involving delicate chemical processing and pharmaceuticals, and it conforms with Good Laboratory Practices (GLP). Developers and manufacturers can use a single, standardized system to carry out a variety of tasks:
- Solid-liquid separation via slurry filtration
- Washing of products
- Vacuum drying
- Re-slurry
- Product sampling
- Product discharge
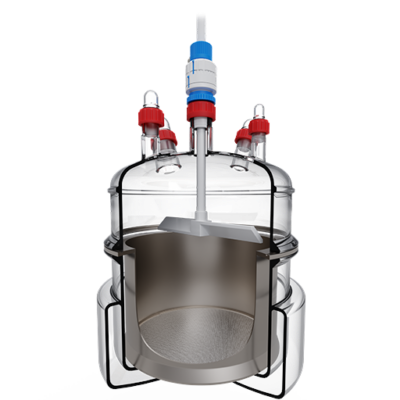
Image Credit: Powder Systems
Maximum Product Recovery
Yield maximization is essential at small-scale production and pilot-scale feasibility stages. With the significance of the finished product in mind, the GFD®Pilot was developed.
The product batch can be easily collected after processing is finished as the filtration basket can be fully removed from the GFD® vessel.
Because it makes it simple and quick to switch between filtration meshes with different pore sizes and materials—like polypropylene, PTFE, Alloy 22, and 316L stainless steel - the GFD® basket is appropriate for multi-product applications.
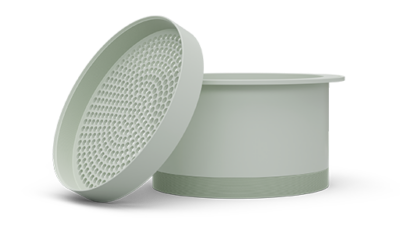
Image Credit: Powder Systems
Flexible Modular Design
Because of its modular construction, the compact and portable GFD®Pilot filter dryer offers production flexibility.
The base frame and motor are compatible with all relevant vessel materials (Borosilicate 3.3 Glass, 316L stainless steel, and Alloy 22), providing a straightforward, functional solution, just like the GFD®Lab series.
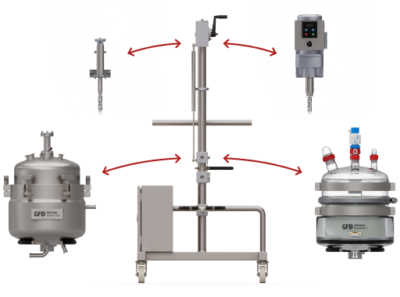
Image Credit: Powder Systems
Complete Mobility
The GFD®Pilot includes a movable frame enabling integration with various upstream procedures.
The frame has been designed to be as compact as possible to facilitate integration within fume cupboards and walk-in laminar flow booths.
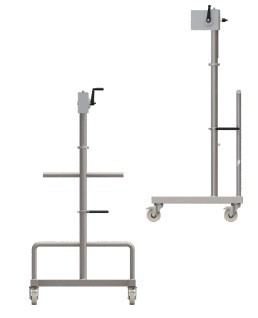
Image Credit: Powder Systems
Hazardous Area Compliant
Because organic solvents are frequently used in chemical and pharmaceutical operations, hazardous area considerations must be made when scaling up to the operational levels possible with the GFD®Pilot.
To address this, PSL provides alternative agitator drives that fit these settings and have the necessary certifications, such as ATEX and NFPA.
Pneumatic motor drives are also used to maintain the compact design.
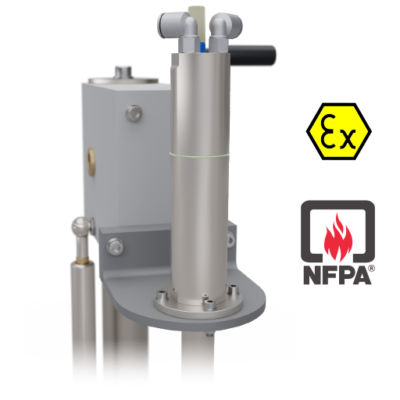
Image Credit: Powder Systems
Pressure Directives
Metallic variants of the GFD®Pilot are offered for situations with higher operating pressure requirements.
Pressure Directives of the installation location are accommodated within the design. If necessary, PSL can provide SELO, PED, and U-Stamp certification.
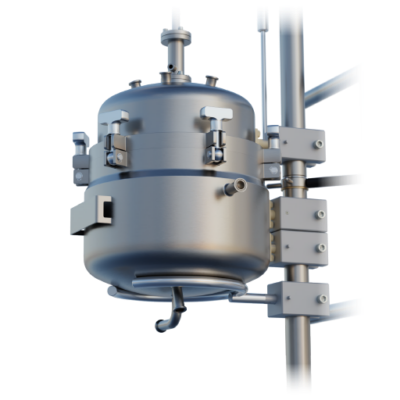
Image Credit: Powder Systems
Be Containment-Ready with the GFD®FilterBox
PSL, one of the first companies to specialize in containment technology, created the unique FilterBox isolator range to fit every vessel variation used with the GFD®Pilot.
Selecting a GFD®FilterBox shields the product from production surroundings and protects operators from the most toxic and dangerous substances.
PSL also offers integration solutions for/with third-party containment providers.
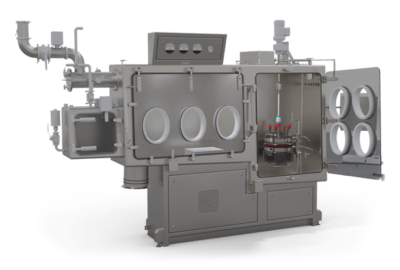
Image Credit: Powder Systems
Vessel Specification
Applies to 500 Series Glass & Metallic Variations. Source: Powder Systems
. |
. |
Typical Product Cake Volume |
0.93 – 5.00 L |
Vessel Volume |
10.0 L |
Filtration Area |
0.05 m2 |
Frame Dimensions (H x W x D) |
1680 x 784 x 650 mm |
Download the Brochure for More Information
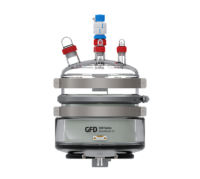
500 Series Glass Vessel. Image Credit: Powder Systems
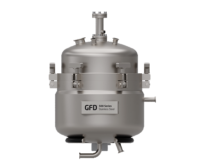
500 Series Metallic Vessel. Image Credit: Powder Systems