Examining the results of millions of years of evolution and applying those learnings to enhance material properties has a romantic connotation to it. This is precisely the path that Mingyang Zhang, Ning Zhao & al. decided to follow in their investigation of bioinspired architecture for material design, aiming to attain enhanced physical properties.
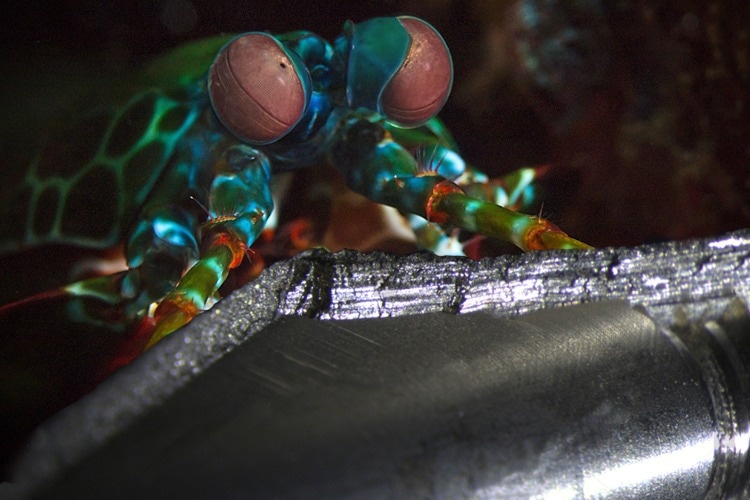
Image Credit: Thermo Fisher Scientific - Software
The team drew inspiration from three members of the animal kingdom for their investigation. The shell of the sea snail Haliotis Rufescens inspired a brick-and-mortar type of architecture, while the colorful variety of mantis shrimp, Odontodactylus scyllarus, provided the design for a twisted plywood architecture. Lastly, the mollusk Saxidomus purpuratus served as a reference for a cross-lamellar type of architecture.
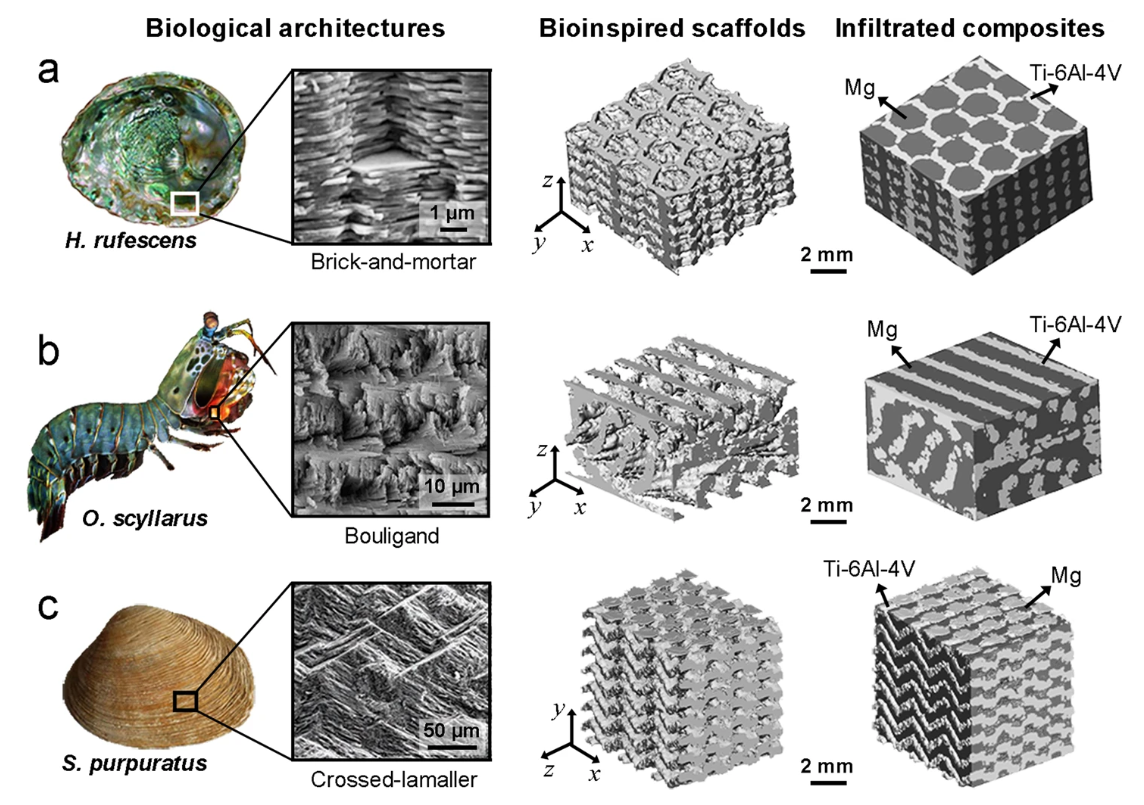
The structures of the representative biological prototypes (sea snail, mantis shrimp, and clam) are displayed together with the brick-and-mortar, Bouligand, and crossed-lamellar architectures. Additionally, the bioinspired scaffolds and the infiltrated composites are shown. Image Credit: https://doi.org/10.1038/s41467-022-30873-9
From Ideation to Fabrication
The team decided to replicate the described architecture using a combination of a 3D-printing suitable titanium alloy and a second phase made of magnesium. This decision was made after careful consideration, as shaping and combining different metals typically means working with high temperatures or pressures, in contrast to what can be achieved with polymers.
By using 3D printing, the team was not only able to build the material “bottom-up” to reflect what happens in nature, but they could also create a porous scaffold of Ti-6Al-4V suitable for a pressure-less infiltration of Mg.
After the bioinspired materials were manufactured, the scientists used X-Ray and electron microscopy (XRT, CT, SEM) to assess the absence of pores in the material.
Make it—and Break it!
As the materials were manufactured according to expectations, the team proceeded to apply tensile stress on the sample in the hope that the material properties would eventually justify the convoluted fabrication methods.
The materials were then scanned with a CT microscope. The findings were transferred to visualization and image processing software, enabling the team to isolate and analyze the fractures that had developed within the material. This yielded valuable insights into the formation of fractures based on the chosen architecture, validating the selection of specific materials utilized in the manufacturing process
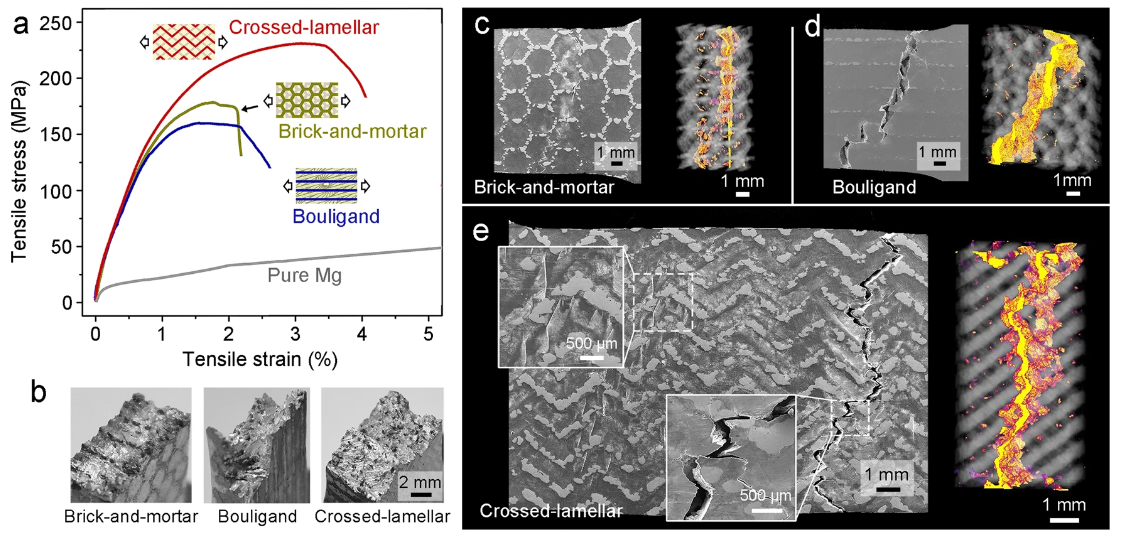
a Tensile engineering stress-strain curves and b overall fracture morphologies of the composites with the loading configurations for tensile tests illustrated in the insets in a. The data for coarse-grained pure Mg are also shown in (a) for comparison. c–e SEM images and X-ray computed tomography (CT) volume renderings of the tensile samples unloaded just prior to fracture for the (c) brick-and-mortar, (d) Bouligand, and (e) crossed-lamellar architectures. The CT images were processed by filtering out the signals of Mg and highlighting the cracking regions in yellow color. The insets in e magnify the slip bands within Mg and the deflection and branching of cracks in the composite with crossed-lamellar architecture. Image Credit: https://doi.org/10.1038/s41467-022-30873-9
Was the Performance Better?
The team employed two reference points for comparing the bioinspired materials. The first reference involved a dense 3D-printed Ti-6Al-4V sample. This comparison highlighted the superiority of the second material in terms of tensile properties.
The situation flipped when comparing it to a stir-cast Mg alloy reinforced with Ti-6Al-4V to approximate the chemistry of the bioinspired sample. In this comparison, the bioinspired sample outperformed in both strength and ductility, with the cross-lamellar architecture proving superior.
Visualizing the Fractures
To gain a clear understanding of fracture formation, the typical procedure involves utilizing image segmentation software to identify and emphasize the fractures within the material.
In this study, the fractures were observed using Avizo Software from Thermo Fisher Scientific, which highlights how the cracks do not propagate in a straight path but rather in-plane and out-of-plane (crack deflection and crack twist).
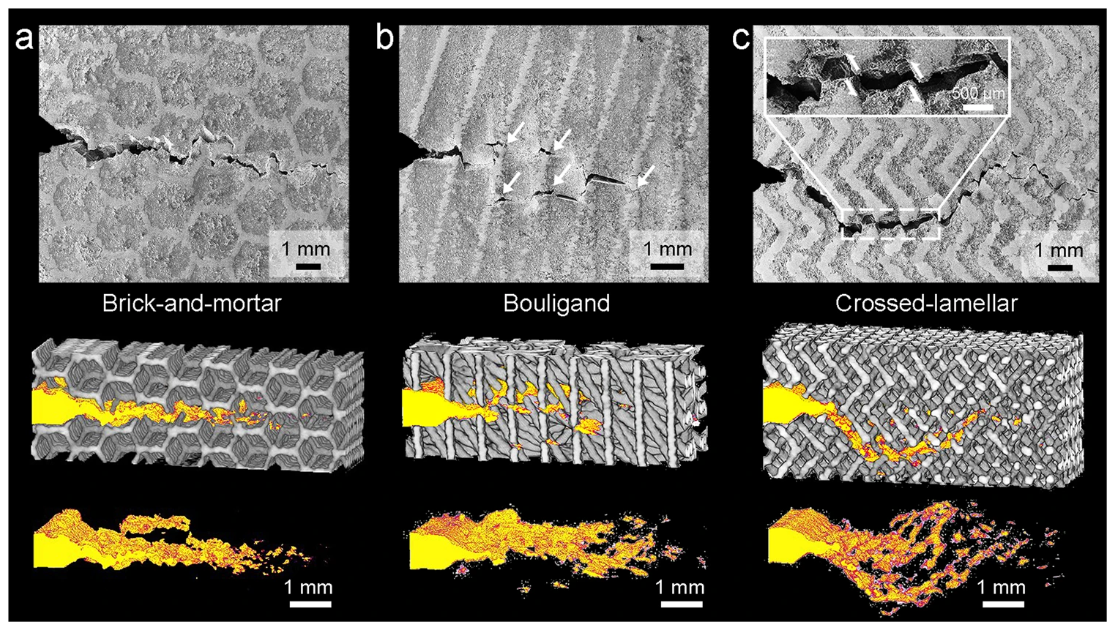
SEM images and CT volume renderings of the quasi-static fracture toughness samples for the composites with bioinspired (a) brick-and-mortar, (b) Bouligand, and (c) crossed-lamellar architectures. The CT images were processed by filtering out the signals of constituents and highlighting the cracking regions. The white arrows in (b) indicate the microcracks ahead of the crack tip. The inset in (c) magnifies the zig-zag cracking path and the resulted frictional sliding between crack faces, as indicated by the arrows. Image Credit: https://doi.org/10.1038/s41467-022-30873-9
The team concluded that by mutually partitioning components, the cracking in the weaker Mg phase could be constrained, thereby delaying the fracture of the entire composite. These improved mechanical properties have led the researchers to envision potential future applications for similar bioinspired materials in structural or biomedical fields.
Learn more: Introduction to Avizo Software for composite materials characterization webinar
References and Further Reading
Zhang, M., Zhao, N., Yu, Q. et al. On the damage tolerance of 3-D printed Mg-Ti interpenetrating-phase composites with bioinspired architectures. Nat Commun 13, 3247 (2022). https://doi.org/10.1038/s41467-022-30873-9
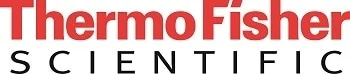
This information has been sourced, reviewed and adapted from materials provided by Thermo Fisher Scientific - Software.
For more information on this source, please visit Thermo Fisher Scientific - Software.