Smart or intelligent materials possess unique capabilities, such as self-adaptability, memory, self-sensing, and multi-functionality, making them attractive across many industries, including aerospace. With air travel passengers expected to double to approximately 8 billion per year by 2036, advanced technologies like smart materials are essential to meet this demand safely and economically.
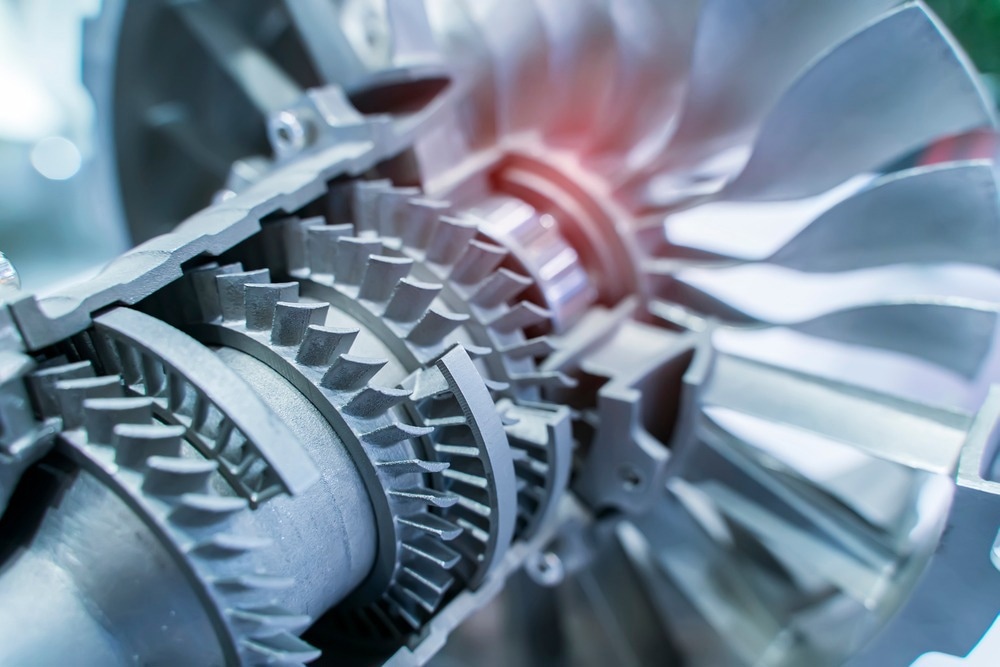
Image Credit: asharkyu/Shutterstock.com
Aerospace engineering applications are often performed in open and highly variable environments.1 The primary research motivations in aerospace include weight reduction, cost savings, and component service life extension. Substantial investments are thus being made in research to integrate smart materials into aerospace applications.
What are Smart Materials?
Smart materials are innovative constituents with superior structural and functional performance than conventional materials. They can precisely modify their physical properties in response to external stimuli such as pressure, temperature, electric and magnetic fields, stress, chemicals, and nuclear radiation.
The response of an object made from smart materials can manifest in changes to its size and shape, rigidity, restraining, adhesion, or viscosity. These materials are also known as intelligent materials due to their intellectual operations, such as their ability to detect errors and fissures and subsequently self-repair. Various types of smart materials are employed in aerospace innovations based on their properties and functionalities.1
Shape Memory Alloys in Aerospace
Shape Memory Alloys (SMAs) are a class of thermo-responsive materials that change shape in response to thermomechanical or magnetic variation.2 They undergo a large change in elasticity modulus upon heating above the phase-change temperature, making them well-suited for manufacturing actuators.1
SMAs are bio-compatible, lightweight, and have a high force-to-weight ratio. They can return to a predetermined shape when heated, contributing to aerodynamic control surfaces and self-healing structures.2
Some commonly used SMAs are nitinol (Ni-Ti alloy), Fe-Pt, and CuAlNi. These materials improve the twisting and turning capabilities of aircraft wings and hinge-less systems.1 SMAs can be implemented in fixed-wing aircraft, rotorcraft, and spacecraft.2
Piezoelectric Materials for Energy Harvesting and Sensing
Certain polymers and ceramics undergo mechanical changes in response to a varying electric field or produce a voltage when subjected to stress. These are called piezoelectric materials. Thus, a piezoelectric material-based structure can be bent, expanded, and folded by applying an electric field.1
In aerospace innovation, these smart materials can be used to transfer aerodynamic vibrations into usable electrical power supply for small sensors, wireless nodes, and other hard-to-reach areas of an aircraft. Such piezoelectric energy harvesting can eliminate the need for complex aircraft wiring, thereby reducing airplane weight.3
Some commonly used piezoelectric materials are lead zirconate titanate (PZT), polyvinylidene fluoride, and lead magnesium niobate. They also find applications in structural health monitoring (SHM) systems that detect damage or stress in aircraft components.1
Smart Composites for Enhanced Structural Performance
Innovative composites based on aluminum (Al), magnesium (Mg), titanium (Ti), ceramics, and polymers have been developed, showcasing outstanding properties for aerospace applications.
Recently, advanced carbon fiber-reinforced polymer (CFRP) composites have significantly contributed to the manufacture of lightweight structures and are used in airframes and engine components to decrease fuel expenditure.
Advanced technologies that combine smart composites with traditional materials offer enhanced properties such as optimized weight reduction, fatigue resistance, fracture toughness, flight range, corrosion resistance, and damage tolerance. Sensors mounted on lightweight carbon and glass fiber composites are employed as real-time SHM systems.4
Thermoelectric Materials for Temperature Regulation
Thermoelectric materials allow direct conversion of temperature difference into electrical energy without the use of moving parts. They help generate energy in extreme conditions like outer space, where photovoltaic energy harvesting fails. In 1989, NASA’s Galileo spacecraft contained a thermoelectric module to generate electrical power.
Since then, the application of thermoelectric materials has expanded significantly. They are being used to manage the thermal conditions of spacecraft and high-speed aircraft. Thermoelectric energy generators can convert waste heat into electrical energy, supporting sustainable energy production and waste energy re-utilization. Wireless sensors made of thermoelectric materials are also used to ensure aircraft safety and during flight tests. 5
Industry Pioneers: Companies Advancing Smart Materials in Aerospace
The aerospace industry faces significant economic pressure to lower costs while boosting performance and ensuring compliance with critical safety parameters.1 Thus, various companies are investing in the advancement of smart materials for aerospace applications.
For instance, Boeing uses smart material-actuated rotor technology to reduce noise and improve flight performance by reducing vibrations by approximately 80 %. Airbus Helicopters SAS has developed a similar system. Piezoelectric material-based sensors are also being installed in Boeing 777 aircraft to measure levels of ultrasonic fuel tanks.1
Smart materials can be used to modify the structure of different propulsion systems’ inlets on aircraft. For example, NASA has developed a wind tunnel that features one SMA installed opposite another. This setup can be used to rotate the inlet cowl, altering its cross-sectional area through sequential heating of each SMA. Such SMAs pave the way for the development of morphing wings or adaptive air inlets for improved flight efficiency.2
Future Perspectives
Advances in nanotechnology are extending the capabilities of smart materials by enhancing their functionality. Nanomaterials respond to external stimuli faster than traditional smart materials due to their small size, large surface area, and multiple surface-active sites. This synergy between nano and smart materials is set to accelerate aerospace innovation.
For instance, layers of smart nanomaterials can detect cracks in an aircraft. The surface texture of an aircraft body fabricated from nano-smart material can change in response to temperature, pressure, or electric field variations.1 Coating jet engine turbine blades with nanocomposites also prevents grain formation, even at high temperatures.4
However, the production of smart nanomaterials faces challenges such as poor size control, long durations, high costs, and low manufacturing rates. Quality and costs are the major challenges in developing smart materials.1 The low strength-to-weight ratio of aircraft components limits their mechanical and structural performance.4
Smart materials also encounter limitations in practical applications, including difficulties in anchoring within laminated structures, coupling electrical and magnetic characteristics, and keeping pace with advancements in microelectronics, information processing, and sensor technology.1
Despite these limitations, smart materials are on track to dominate the future. Their unique properties can be used to overcome challenges facing the aerospace industry. Future innovations should focus on fabricating regulated structures and adaptable wings to strengthen maneuverability.
Compressed and efficient smart materials are required to control noise and vibration. Nano-smart materials with enhanced shock absorption, spontaneous damage prevention, self-repairing abilities, and temperature moderation can address current limitations and unlock new possibilities in aerospace technology.1
For More on Smart Materials: Smart Polymers and Their Impact on the Future of Materials Science
References and Further Reading
1. Basheer, AA. (2020). Advances in the smart materials applications in the aerospace industries. Aircraft Engineering and Aerospace Technology. doi.org/10.1108/aeat-02-2020-0040
2. Balasubramanian, M., Srimath, R., Vignesh, L., & Rajesh, S. (2021). Application of shape memory alloys in engineering – A review. Journal of Physics: Conference Series. doi.org/10.1088/1742-6596/2054/1/012078
3. Brigham Young University. (no date). Piezoelectric Energy Harvesting. Brigham Young University. Available at: https://icelab.byu.edu/piezoelectric-energy-harvesting#:~:text=Piezoelectric%20Energy%20Harvesters%20(PEHs)%20use
4. Parveez, B., Kittur, M. I., Badruddin, I. A., Kamangar, S., Hussien, M., Umarfarooq, M. A. (2022). Scientific Advancements in Composite Materials for Aircraft Applications: A Review. Polymers. doi.org/10.3390/polym14225007
5. D’Angelo, M., Galassi, C., Lecis, N. (2023). Thermoelectric Materials and Applications: A Review. Energies. doi.org/10.3390/en1617640
Disclaimer: The views expressed here are those of the author expressed in their private capacity and do not necessarily represent the views of AZoM.com Limited T/A AZoNetwork the owner and operator of this website. This disclaimer forms part of the Terms and conditions of use of this website.