By Taha KhanReviewed by Lexie CornerMay 2 2024
Three-dimensional (3D) printing is a type of additive manufacturing that constructs three-dimensional objects layer by layer from a digital model. This technology has transformed various industries, especially healthcare, due to its ability to provide precise and accurate miniaturized biomedical sensors.
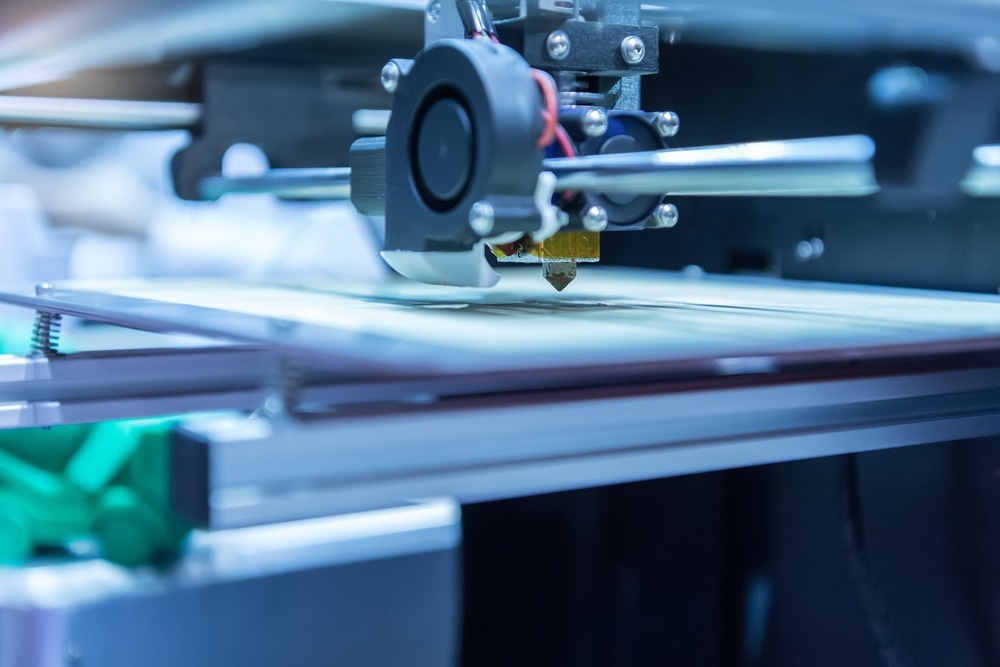
Image Credit: asharkyu/Shutterstock.com
These tiny sensors can be implanted within the body or worn externally to monitor various health parameters, including blood sugar levels, heart rate, blood pressure, and even brain activity.1
Basics of 3D Printing
3D printing is used to create real-life 3D objects from a digital model, facilitating the realization of ideas and concepts with high accuracy.
Various 3D printing technologies exist, including stereolithography (SLA), fused deposition modeling (FDM), and selective laser sintering (SLS), each offering distinct advantages in terms of resolution, material compatibility, and production speed.1
For instance, stereolithography produces 3D objects using a photopolymer resin cured by computer-controlled ultraviolet (UV) light to create solid layers. After each layer is completed, the build platform descends, a new layer of resin is spread over the cured coating, and the process is repeated until the entire object is formed.2
Fused deposition modeling, another additive manufacturing process, involves feeding a thermoplastic filament from a spool into the extrusion head, which heats it to its melting point. The nozzle moves along a predetermined path, adding the melted material in thin layers, which solidify upon cooling. As each layer is deposited, the build platform lowers to accommodate the new layer and eventually forms the desired 3D object.3
Similarly, selective laser sintering builds 3D objects by selectively fusing powdered material—typically thermoplastics or metals—using a high-powered laser.4
What are Biomedical Sensors?
There are various types of biomedical sensors, each tailored to a specific purpose.
For instance, electrochemical sensors use electrical signals generated by the body in response to chemical changes, such as glucose levels.
Piezoelectric biomedical sensors convert mechanical stress into an electrical signal, making them suitable for monitoring pressure or motion. Similarly, optical sensors utilize light to detect various biological events, such as changes in blood oxygen saturation. 5
Integrating 3D Printing with Biomedical Sensors
The main advantage of 3D printing is that it allows manufacturers to fabricate complex structures using almost the same process, enhancing precision, accuracy, control, and repeatability.
Traditional manufacturing methods, such as casting and machining, involve multiple processes, each with its limitations in terms of precision and accuracy. Consequently, the final product, particularly for miniaturized objects like biosensors, often falls short of these metrics.
However, in 3D printing, the process begins with the creation of a 3D computer aid-designed (CAD) model, which provides the manufacturer with a preview of the final product. If any alterations are needed, adjustments can be easily made to the CAD model. This updated model is then fed into a 3D printer, which accurately and precisely materializes the design in the real world.1, 5, 6
3D-printed Biosensor for Monitoring Tissue Metabolites
In a 2015 study, researchers developed a novel 3D-printed microfluidic device that integrates biosensors for the continuous monitoring of human tissue metabolites.
This device, coupled with FDA-approved clinical microdialysis probes, allows real-time analysis of subcutaneous glucose and lactate levels, particularly during physical activities like cycling. Unlike conventional methods, this system offers improved temporal resolution and eliminates the need for constant interruptions during activity.
The study demonstrates the potential of this wearable technology in both sports monitoring and clinical applications, paving the way for real-time evaluation of tissue health and fitness effectiveness.7
Material Innovations and Design Flexibility
Innovation in biocompatible materials is crucial for the advancement of 3D-printed biomedical sensors.
For instance, conductive polymers can conduct electricity, making them ideal for crafting electrodes within electrochemical sensors. Similarly, biocompatible hydrogels mimic the body's own tissues, ensuring better integration with the surrounding environment and minimizing the risk of rejection.
Novel 3D Electrochemical Sensor
In a 2015 study, researchers developed a novel 3D electrochemical sensor utilizing conductive polymers for biosensing applications.
The sensor, constructed on a polymeric substrate, features through-substrate via contacts filled with a conductive polymer, facilitating vertical electrical signal transmission and enabling direct sensing without transferring cells onto the sensor surface.
The chip, comprising gold electrodes and an Ag/AgCl quasi-reference electrode, demonstrated stable voltammetric signatures and successfully detected alkaline phosphatase enzymatic activity in cell lines.
Fabrication involved a simple, cost-effective process, including mold design with stereo lithography 3D printing, conductive PDMS filling, and electrode deposition.
This 3D-printed sensor is important for non-invasive diagnostics in both in-vitro and in-vivo settings, offering potential applications in healthcare and medical industries for precise surgical procedures with enhanced sensor functionality and patient compatibility.8
Challenges and Limitations
While the advantages of 3D-printed biosensors are abundant, there are inherent challenges associated with these technologies that still need addressing.
3D printing is a slow process, requiring a lot of time to print even simple designs. This poses a significant challenge in scaling production processes while maintaining precision and consistency. 3D printing is also restricted by the limited range of suitable materials.1, 5, 6
As medicine directly impacts human health, strict regulatory requirements for medical devices are in place. Ensuring that 3D-printed sensors meet these standards requires rigorous testing and quality control measures.
Future Outlooks
The future of 3D printing in biomedical sensors is tied to advancements in material science, printing techniques, and automation.
In the future, 3D printers will integrate more materials, allowing researchers to develop customized sensors for individual patients, considering factors like body shape and allergies. Similarly, advancements in automation and printing techniques could lead to faster, more precise, and more accurate printers.
More from AZoM: Can Fungal Filaments Transform Energy Storage?
References and Further Reading
- Paul, AA., Aladese, AD., Marks, RS. (2024). Additive Manufacturing Applications in Biosensors Technologies. Biosensors. doi.org/10.3390%2Fbios14020060
- Melchels, FP., Feijen, J., Grijpma, DW. (2010). A review on stereolithography and its applications in biomedical engineering. Biomaterials. doi.org/10.1016/j.biomaterials.2010.04.050
- Mohamed, OA., Masood, SH., Bhowmik, JL. (2015). Optimization of fused deposition modeling process parameters: a review of current research and future prospects. Advances in manufacturing. doi.org/10.1007/s40436-014-0097-7
- Fina, F., Goyanes, A., Gaisford, S., Basit, AW. (2017). Selective laser sintering (SLS) 3D printing of medicines. International journal of pharmaceutics. doi.org/10.1016/j.ijpharm.2017.06.082
- Ali, MA., Hu, C., Yttri, EA., Panat, R. (2022). Recent advances in 3D printing of biomedical sensing devices. Advanced functional materials. doi.org/10.1002%2Fadfm.202107671
- Han, T., Kundu, S., Nag, A., Xu, Y. (2019). 3D printed sensors for biomedical applications: a review. Sensors. doi.org/10.3390%2Fs19071706
- Gowers, SA., et al. (2015). 3D printed microfluidic device with integrated biosensors for online analysis of subcutaneous human microdialysate. Analytical chemistry. doi.org/10.1021/acs.analchem.5b01353
- Ragones, H., Schreiber, D., Inberg, A., Berkh, O., Kósa, G., Shacham-Diamand, Y. (2015). Processing issues and the characterization of soft electrochemical 3D sensor. Electrochimica Acta. doi.org/10.1016/j.electacta.2015.04.109
Disclaimer: The views expressed here are those of the author expressed in their private capacity and do not necessarily represent the views of AZoM.com Limited T/A AZoNetwork the owner and operator of this website. This disclaimer forms part of the Terms and conditions of use of this website.