Discover how the Thermo ScientificTM ProcessTM 11 and ProcessTM 16 extruders can aid in mechanical polymer recycling by helping define the optimal workflow and recycling parameters.
Why is it important to recycle polymers, and what are the primary methods of recycling these?
A number of technical applications, including packaging and equipment, employ plastic materials comprised of complex mixtures of dozens of chemicals. The complexity of these materials means that recycling such plastics to keep them out of a landfill is far more complicated than placing the item into the proper waste bin according to its labeling.
Researchers are working to develop closed recycling loops. These loops begin at the waste collection stage, separating out individual waste components before determining the best way to process these into recycled plastics that are equivalent to virgin plastic materials.
Three main methods of recycling exist, and these are categorized as chemical, mechanical, and solvent-based or physical. Each of these methods has its own advantages and disadvantages depending on the application in question; for example, these methods produce very different outcomes when used to recycle polymeric materials like plastics.
For example, chemical recycling works via depolymerization, resulting in a mix of different smaller building blocks or monomers. Physical recycling, however, uses solvents to dissolve plastics, but this method does not influence the polymer structures themselves.
Mechanical recycling involves the use of techniques like grinding, magnetic separation, sorting, vacuuming away volatile compounds (VOCs), and extrusion with melt filtration steps. The polymer structure is not affected during these mechanical recycling processes, at least not intentionally.
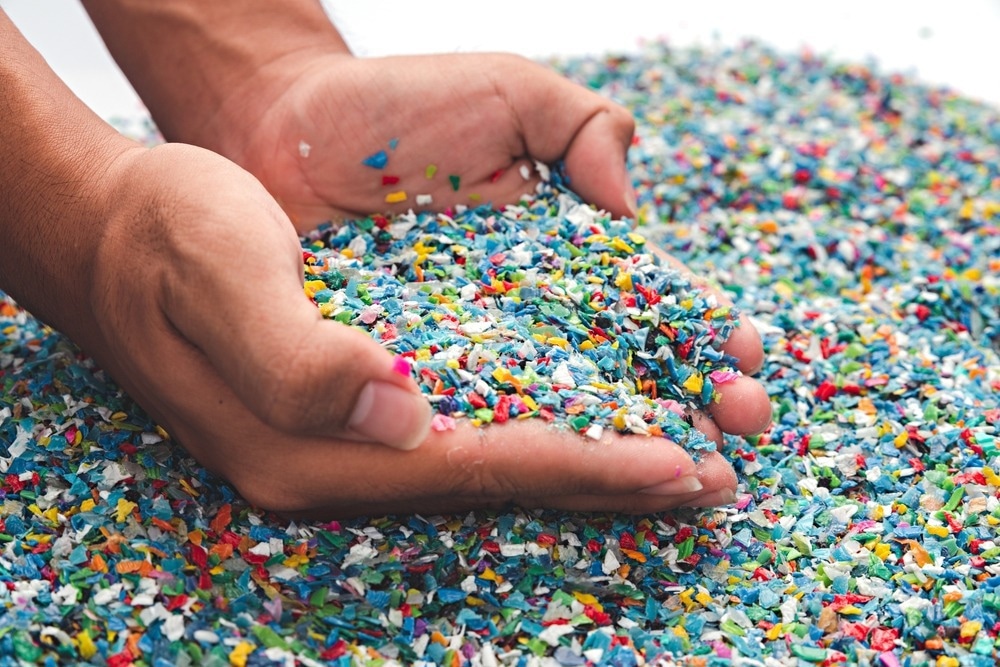
Image credit: meaw_stocker/shutterstock.com
Could you tell our readers about your work in mechanical polymer recycling? What are some of the specific challenges associated with this method?
I work at the Leibniz University in Hannover, Germany, specifically in the Department of Plastic Technology and Recycling, which is a part of the IKK - Institute of Plastics and Circular Economy.
My department focuses on mechanical recycling, looking at how we can use different mechanical processing steps to produce the highest purity plastic recyclates at the end of the recycling process.
A number of governmental organizations like the European Union (EU) have proposed directives that will require, for example, the automotive industry to use more recycled materials in their manufactured products. Other industries are also trying to be more environmentally conscious and reduce the amounts of waste they produce.
The textile industry provides a good example of both complex material usage and production waste, both of which can result in significant challenges in terms of recycling efficiency.
Sport bags or clothes, for example, tend to contain mixed materials that are often coated with other substances. These materials are used for manufacturing bags or garments, but there will be a lot of production-cut materials that cannot be used, so that excess material becomes waste that must be incinerated, placed into landfills, or disposed of in other ways. This excess material is not recycled, however.
A key element of IKK’s mission is working out how to recycle waste like this and produce useful materials from it.
We use a range of instruments to test these approaches. For example, a small laboratory-scale extruder, like the Thermo Scientific Process 11 or Thermo Scientific Process 16 Extruders, is extremely useful in our testing and recycling research to determine the most ideal parameters for different recycling routes.
This complex process involves a great deal of experimentation and many variables. For any product that could potentially be recycled, we must ask questions like, What is the material’s chemical composition? Is it suitable for mechanical recycling? Should the material be cut or ground up, and if so, to what size particles? What kind of pre-treatment is necessary in order to make the material processable in the extruder? Should the material be pelletized to improve its density before feeding into the extruder?
We must also consider the order of the pre-treatment steps and which order will allow us to optimize the material’s processing. The performance of the recyclates is also important; for example, after processing, would injection molding or fiber-to-fiber recycling be possible?
You mentioned the use of lab-scale extruders in your work. Why are these instruments so central to your workflow and in evaluating the effectiveness of mechanical recycling approaches?
IKK uses lab-scale extruders for preliminary work trials because it is impractical to test all these possible variables on an industrial scale. An industrial-scale extruder would require a minimum of approximately 100 kilograms of starting material. Not only is running experiments with such large volumes wasteful, in some cases such a substantial amount of material is not available at all.
Using the Process 11 and Process 16 lab extruders allows us to perform representative trials with 5 kg or 10 kg of material to gain some initial insight into the recycling potential of the material.
At lab scale, we are able to analyze a range of scenarios and perform different tests in the lab and in the technical center, allowing us to manufacture the end specimens and analyze these using appropriate material methods.
An extruder’s continuous processing capabilities allow the researchers to perform in-line testing to determine material characteristics such as color scale, rheological properties, flammability, the composition of captured off-gases, and many more.
These in-line techniques can be performed in just a few minutes, and they typically make testing easier and more frequent versus off-line laboratory testing. Lab testing, for example, often takes much longer and only uses a small, potentially non-representative, sample of the overall batch material.
It is possible to achieve representative results with a smaller quantity of plastics when using a lab extruder. This allows us to make more informed decisions when planning trials with larger extruders. Once a small amount of material has been used to experimentally determine a process, the method can be transferred to larger extruders with relative ease due to the scalability of the extrusion process.
What are some of the other benefits of working with lab-scale extruders?
A lab-scale extruder’s manageable size provides other advantages. We often use small-scale extruders where we have some materials that are difficult to work with.
Many variables must be considered when recycling plastic waste from products that were not designed for recycling and have never been recycled before. For example, plastic waste from electrical scrap, end-of-life vehicles, rotor blades, and similar products can pose specific recycling challenges.
Decisions must be made around which additives to use or what size particles work best. In these instances, it is possible to pre-adjust key processing parameters using lab extruders working with a very small amount of material. Because a lot of trials are required to optimize processing parameters and we just systematically adjust these, using small amounts of initial material is advisable.
The straightforward operation and small footprint of an instrument that fits on a lab bench are also advantages. Because our lab is based at a university, we work with a lot of student projects. The extruder is easy to use and can be operated by one person, meaning that students are able to work on the extruders themselves as part of their projects.
Small extruders also have excellent potential for use in feasibility studies. In fact, a lot of our projects would not be possible without them.
Was there a particular project that led to IKK’s adoption of lab-scale extruders in its work?
It was made apparent in a test case with an electronic component that highlighted the usefulness of lab-scale extruders when recycling a complex sample. The electronics sector uses many small components. These components may have a mass of just a few hundred grams, but often, only a part of a component is made of plastics.
In this instance, more than 12 different types of plastics were present in a single component, meaning that it was challenging to develop a suitable recycling method. The amount of each polymer is very small, so small extruders are essential for these types of feasibility studies.
Our researchers were able to use different sizes of extruders on the same batch of source material. An electronics company generally provides around 200 kg to 300 kg of a product to IKK.
First, we subject these components to grinding and metal separation processes.
Next, spectroscopic methods were used to help separate out the plastics, which resulted in a mixture of different amounts of polymers. Plastics from the devices’ housing made up more than 50 kg of obtained material, so this was enough to justify processing via a semi-industrial extruder.
Some of the remaining polymers comprised only 1 kg of material, or 500 grams or even less, however. The Thermo Fisher extruders were extremely useful for investigating these polymers because there is no other extruder on the market that can process such a small amount.
The IKK's smaller injection molding machine was also able to produce the specimens for subsequent testing with a focus on purity, processability, and use performance. This robust combination of technologies allowed us to manufacture new recycled products from what had been a complex mixture of polymers.
Once we had created new recycled products, we compared them against virgin plastics. We processed a similar amount of virgin plastics using the same extruder and identical process parameters. We compared the recycled products with the virgin plastics in terms of their tensile strength, chemical composition, and other characteristics, and we found that even at such a small scale, the recycled materials were good enough to be reused again, just as if they were virgin plastics.
How do you see your use of Thermo Fisher Scientific’s lab-scale extruders evolving in the future?
Many applications and sectors are still at the beginning of the transition to a circular economy, and there are often only small quantities of input streams available.
This means that there is a very promising future for smaller lab-scale extruders’ use in the recycling field. The Process 11 or Process 16 lab-scale instruments may be the only viable options for developing the best recycling strategy when working with such limited quantities of materials.
Thermo Fisher Scientific can provide assistance to researchers working with novel or hard-to-process materials, and I was thrilled with the level of support IKK received. In some cases we worked with, the material was so specific that our extruders at the technical university were not able to process it. Additional equipment modules were needed, but we were able to send the material to Thermo Fisher Scientific, and it was perfectly processed.
Not only this, but the team at Thermo Fisher Scientific informed us what was done, how it was done, and why it was done that way.
Our colleagues at Thermo Fisher Scientific were so helpful, and we are very happy to be working with them both now and in the future.
About the interviewee
Dr. Madina Shamsuyeva is the Head of the Department of Plastics Technology, Recycling, and Plastics Analytics at IKK—Institute of Plastics and Circular Economy, Leibniz University Hannover. Her fields of expertise include chemical analysis of (recycled) plastics, standardization of plastic recycling, and fiber surface treatment. Her current research is focused on polymer analytics, recycling of thermoplastics, and textile recycling.
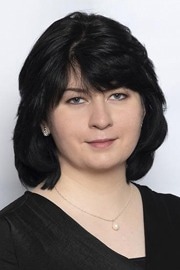
Disclaimer: The views expressed here are those of the interviewee and do not necessarily represent the views of AZoM.com Limited (T/A) AZoNetwork, the owner and operator of this website. This disclaimer forms part of the Terms and Conditions of use of this website.