Impact Tests Impact tests are designed to measure the resistance to failure of a material to a suddenly applied force. The test measures the impact energy, or the energy absorbed prior to fracture. The most common methods of measuring impact energy are the: • Charpy Test • Izod Test What is Impact Energy Impact energy is a measure of the work done to fracture a test specimen. When the striker impacts the specimen, the specimen will absorb energy until it yields. At this point, the specimen will begin to undergo plastic deformation at the notch. The test specimen continues to absorb energy and work hardens at the plastic zone at the notch. When the specimen can absorb no more energy, fracture occurs. The Charpy Test While most commonly used on metals, it is also used on polymers, ceramics and composites. The Charpy test is most commonly used to evaluate the relative toughness or impact toughness of materials and as such is often used in quality control applications where it is a fast and economical test. It is used more as a comparative test rather than a definitive test. Charpy Test Specimens Charpy test specimens normally measure 55x10x10mm and have a notch machined across one of the larger faces. The notches may be: • V-notch – A V-shaped notch, 2mm deep, with 45° angle and 0.25mm radius along the base • U-notch or keyhole notch – A 5mm deep notch with 1mm radius at the base of the notch. What Does the Charpy Test Involve? The Charpy test involves striking a suitable test piece with a striker, mounted at the end of a pendulum. The test piece is fixed in place at both ends and the striker impacts the test piece immediately behind a a machined notch. 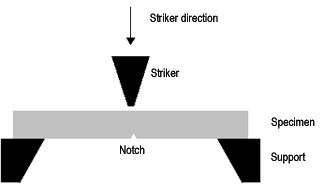 | Figure 1. Schematic of the Charpy impact test. | Determination of Charpy Impact Energy At the point of impact, the striker has a known amount of kinetic energy. The impact energy is calculated based on the height to which the striker would have risen, if no test specimen was in place, and this compared to the height to which the striker actually rises. Tough materials absorb a lot of energy, whilst brittle materials tend to absorb very little energy prior to fracture. Factors Affecting Charpy Impact Energy Factors that affect the Charpy impact energy of a specimen will include: • Yield strength and ductility • Notches • Temperature and strain rate • Fracture mechanism Yield Strength and Ductility For a given material the impact energy will be seen to decrease if the yield strength is increased, i.e. if the material undergoes some process that makes it more brittle and less able to undergo plastic deformation. Such processes may include cold working or precipitation hardening. Notches The notch serves as a stress concentration zone and some materials are more sensitive towards notches than others. The notch depth and tip radius are therefore very important. Temperature and Strain Rate Most of the impact energy is absorbed by means of plastic deformation during the yielding of the specimen. Therefore, factors that affect the yield behaviour and hence ductility of the material such as temperature and strain rate will affect the impact energy. This type of behaviour is more prominent in materials with a body centred cubic structure, where lowering the temperature reduces ductility more markedly than face centred cubic materials. Fracture Mechanism Metals tend to fail by one of two mechanisms, microvoid coalescence or cleavage. Cleavage can occur in body centred cubic materials, where cleavage takes place along the {001} crystal plane. Microvoid coalescence is the more common fracture mechanism where voids form as strain increases, and these voids eventually join together and failure occurs. Of the two fracture mechanisms cleavage involved far less plastic deformation ad hence absorbs far less fracture energy. Ductile to Brittle Transition Some materials such as carbon steels undergo what is known as a ‘ductile to brittle transition’. This behaviour is obvious when impact energy is plotted as a function of temperature. The resultant curve will show a rapid dropping off of impact energy as the temperature decreases. If the impact energy drops off very sharply, a transition temperature can be determined. This is often a good indicator of the minimum recommended service temperature for a material. |