In medical technology, the quality and documentation standards are superior to those implemented in other branches of industry. Manufacturers of medical products have to ensure a uniformly high quality standard in production and long-term delivery assurance, continually taking basic legal conditions into account. Requirements-oriented quality control thus encompasses not only the development and manufacturing of such products but also the packaging of the medical parts and components.
Individual Solutions
Zwick, the testing machine manufacturer based in Ulm, Germany, has come up with requirements-geared solutions for mechanical, technological investigations in the medical industry. With its versatile, modular offering of machines, specimen grips, and software, Zwick is able to put together the optimal system at excellent value for money. The testing software - tried and tested in both industry and research - supports the user in performing the test jobs. Additionally, integration into the Microsoft Office package allows convenient data exchange between applications.
Example Solutions
A number of the latest Zwick projects illustrate clearly illustrate this:
- Unrolling test for bandages
- Torsion test for artificial hip joints
- Injection and catheter needle testing
- Tightness testing of medical gloves
- Resistance testing of containers and dispensers
- Testing of surgical tubing, fittings, and catheters
- Torsion testing of bone screws and bone replacement materials
- Testing of woven materials used in biomedical applications
Unrolling Test for Bandages
To ensure reliable unrolling of bandages unhindered by stray fibers locking, an unrolling test is performed using a testing machine with 10 kN nominal force and equipped with a driven unrolling unit. A testing program from the Zwick testXpert® program portfolio has been specially designed for this test.
Torsion Test for Artificial Hip Joints
Artificial hip joints have to withstand both compression and torsion stresses. The testing system used consists of a Zwick material testing machine with a nominal force of 20 kN and a 500 Nm torsion drive.
Injection and Catheter Needle Testing
Needle insertion force measurement is a critical parameter for injection needles, catheter needles, transfusion needles, and biopsy needles. Typically a compact Zwick testing machine is used for needle tests - or a member of the ProLine family of testing machines, which has been especially developed for cost-effective standard applications or functional testing of components.
Tightness Testing of Medical Gloves
Medical gloves can be manufactured from materials such as latex, nitrile and vinyl, all of which must adhere to performance levels for tightness against air, liquids, and micro-organisms. Testing should examine the strength and elongation of the material at break to ensure that measured values fall within normal ranges of use.
Testing of strain on gloves with or without a seam is done with the aging effects of the material also evaluated. A Zwick or ProLine testing machine is well suited for these tests.
Resistance Testing of Containers and Dispensers
The force needed to remove the cover, the strength of the handle, the penetrability of the bag or container, and the sealing properties all need to be tested. Ideal for these applications are a Zwick or one of the Zwick ProLine testers.
Testing of Surgical Tubing, Fittings, and Catheters
Surgical tubing is used in a wide range of applications such as drains, feeding tubes, irrigation and surgical procedures and comes in many shapes and sizes with dozens of possible interconnections and fittings that should be both simple and reliable. A Zwick Z005 testing machine supplemented by a 100 Nm torsion testing device was employed to test these critical components. In this test, the use of standard compression force, torque, and indentor was essential.
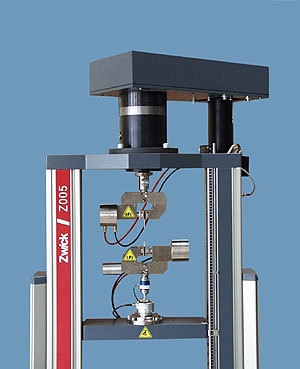
Torsion Testing of Bone Screws and Bone Replacement Materials
A torsion drive is used to insert a bone screw in bone replacement material. The parameters of interest in this test were the necessary torque in connection with the compression force applied. The testing machine used was a Zwick Z020 (20 kN nominal force) with a 100 Nm torsion drive.
Testing of Woven Materials Used in Biomedical Applications
These materials are often used in bandages a product whose materials and designs are characterized by their ability to carry a tensile load - i.e., how much force they can withstand before failure occurs in tension. Measurement of other mechanical properties such as how much liquid the material is able to suck up or the time needed for a liquid to penetrate the material allows evaluation of bandage performance while providing insight for manufacturing processes and quality control. Typically, a Zwick or a compact tabletop model such as the Z005 are used in these tests.
No Manipulation Possible
In both medical technology and the pharmaceutical industry, activities must be traceable even years after they have taken place - and this traceability requirement is especially strict. For this reason, equally strict demands are placed on the software used to document the traceability of the activities carried out. With its proprietary test software, testXpert®, Zwick meets just this challenge with a special option that satisfies these demands.
The new software option from Zwick enables complete, no-manipulation-possible documentation of the actions carried out using the testXpert® software. The exact logging requirements are defined by the user on the basis of the underlying quality management handbook or third-party specifications, as desired. In individual cases, this may mean that any changes made to a test-relevant parameter, e.g., the testing speed, may be recorded from beginning to end of testing.
FDA Compliance
Together with the built-in user administration, this testXpert® package is the ideal tool for ensuring compliance with the requirements of FDA 21 CFR Part 11(guidelines set up by the US Food and Drug Administration).
With quality parameters easily available and assurance that manipulation of data is not possible, manufacturers of safety-critical products reap key benefits: process optimization and enhanced product quality.
|