Introduction
Advanced material fabrication techniques can be classified as single or multi-step processes. The latter are environmentally stressing, energy-consuming, and high-cost techniques. Soft chemistry or soft solution processing, which includes the hydrothermal technique, is a single-step process that is more environmentally friendly than vacuum or chemical vapor deposition of thin films [1].
Hydrothermal techniques have been used for the preparation of thin films of perovskites of the AIIBIVO3 form since 1989 [2, 3]. Initially, BaTiO3 (BT) and SrTiO3 films were prepared by this technique [4] and later other compounds were also synthesized [5, 6]. The method consists in the immersion of the B-metal (usually titanium or zirconium) or of a non-metallic substrate coated with the B-metal in an alkaline aqueous solution containing the A ions at temperatures above 100ºC for a few hours, with pressures well above one atmosphere. Temperatures as low as 55ºC and lower pressures have also been used in the synthesis of BT films [7]. Compatibility with microstructuring techniques used in the semiconductor industry has been shown by growing 2.5 μm features below 100ºC [8]. Hydrothermal film preparation is reviewed in ref. [3].
Despite the fact that the hydrothermal technique is a comparatively low energy consumption technique, the standard hydrothermal or mild-hydrothermal processes (below 100ºC) require raising the temperature of the complete vessel and its surroundings so that the solution can be heated to the working temperature. In this work we propose a modification of this technique leading to an even lower energy-consuming procedure, which we have called the “Localized Hydrothermal Technique”, for the fabrication of BaTiO3 films, which can be extended to several complex oxide thin films. This technique uses the Joule effect to locally heat a metal plate immersed in an aqueous solution of an alkali-earth hydroxide to produce the hydrothermal reaction on the surface of the metal, thus forming a deposit of a complex oxide. In this paper we present successful results of the formation of BaTiO3 films on a Ti metal foil immersed in a Ba(OH)2 solution. A similar technique has been applied recently to the deposition of hydroxyapatite coatings on titanium [9]. In this experiment there was no chemical reaction between the substrate and the solution and the key point was to use the decreasing solubility of hydroxyapatite with increasing temperature to precipitate the film onto the heated substrate.
Experimental
In the first set of experiments the substrates were rectangular titanium foils 0.13 mm thick and 30 x 10 mm. Their room temperature resistance was around 0.01 Ohm. The main impurities reported by the supplier (Mat-Vac Technology) were iron (1200 ppm) and oxygen (750 ppm). The samples were spot-welded to titanium bars 0.91 mm thick, 19.4 mm wide, and 102 mm long and cleaned. The position of the sample in the solution was either horizontal or vertical. In both cases, the sample was covered with around 5 mm of solution. Figure 1 represents the experimental setup when the sample was placed horizontally.
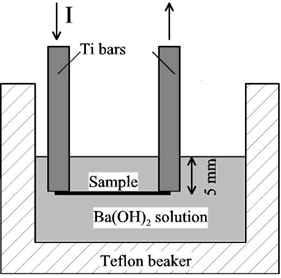
|
Figure 1. Schematic experimental set-up for the localized hydrothermal fabrication of thin films.
|
A 0.25 M Ba(OH)2 solution was prepared with a 98% purity reactive (Fluka, main impurity: Sr) and distilled water previously heated to remove CO2. The solution (80-90 ml) was placed in a Teflon beaker and the sample was immersed in it, and then an AC electric current was passed through the sample. The current was stable at 52 A, leading to a current density of 40 A/mm2 and a dissipated power of around 25 W, which is far less than that required for heating the entire vessel as used in standard setups.
In a second set of experiments the samples were either spot-welded or fixed with titanium screws to titanium bars 3.25 mm in diameter and 80 mm long. Some experiments were performed using zirconium and niobium foils instead of titanium.
The temperature of the foil was measured with a Teflon-coated thermocouple in close contact with it. In some experiments the thermocouple was spot-welded to the metal foil. The foil temperature changed from 40°C to 130°C in 8 min., remaining constant during the rest of the experiment, whose total duration was 15 min.
The samples were characterized by means of x-ray diffraction (XRD), x-ray photoelectron spectroscopy (XPS), Auger electron spectroscopy (AES), micro-Raman spectroscopy and scanning electron microscopy (SEM). XRD was performed on a Siemens D5000 apparatus. Both XPS and AES were measured in a Physical Electronics 1257 system, while micro Raman spectra were recorded on a LabRam 010 from ISA, and SEM was performed in a Philips SFEG XL30 instrument.
Results and Discussion
Titanium Foils Placed Horizontally
The lower face of the samples fabricated in horizontal position by the localized hydrothermal technique were blue or violet due to light interference, generally exhibiting large elongated spots of approximately 10 mm in length (the film) and sometimes a few smaller spots surrounding it. The top face displayed only a few dark spots. Some experiments were performed with the metal foil surrounded by a 6-mm internal diameter Teflon tube in order to avoid convective heat loss, but these samples did not exhibit any film that could be detected by simple observation, except for a few dark spots. All of these visual observations were confirmed by XRD and XPS measurements, revealing that the film growth only took place on the lower side of the metal foil. Similar results were observed by Lisoni et al. in (001) oriented rutile samples placed horizontally in 0.5 M Ba(OH)2 and treated at 200ºC for 4 h, where BT was reported to grow only on the lower face and not on the upper one [10]. Suchanek et al. [11] reported that the grain size of BT films increased with the flow rate of the solution (barium acetate in their case). Film nucleation of PZT, however, can be inhibited by agitation, since convection is related directly with the material supply to the film [12]. We suggest that under our hydrothermal film-growth conditions the difference in convection between the top and the bottom of the strip are responsible of these extreme differences in growth rate.
Figure 2 shows the micro-Raman measurements. Curve a) corresponds to substrate regions where no growth was observed and did not exhibit losses due to barium titanate. Curve b) is from a BT single crystal used as a reference: the sharp peak at 305 cm-1 and the broader one around 720 cm-1 are characteristic of the tetragonal phase of barium titanate and are absent in the cubic phase. Curve c) was recorded from a hydrothermal-electrochemical film grown at 80ºC and described in ref. [13], where the broad features of barium titanate coexist with a peak from the substrate (probably a reflection), thus revealing a thin film. Curve d) was recorded from one of the samples generated in the present work. There were no losses associated with the substrate, which can be interpreted as a film thicker than that the one obtained in c). The broad features of barium titanate revealed a film of rather poor crystallinity, although the distorted feature at around 305 cm-1 was detected, allowing the identification of the pseudocubic BT phase in the region of the continuous film, revealing the same pseudocubic BT film.
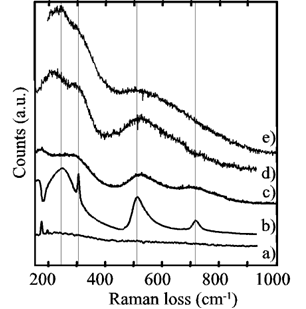
|
Figure 2. Micro-Raman spectra from a) a Ti substrate, b) a BaTiO3 single crystal, c) a hydrothermal-electrochemical film (80ºC) [13], d) a continuous film generated in this work, and e) a spot on a film-free region of the substrate (sample placed horizontally).
|
XPS spectra (not shown) exhibited the usual carbon contamination and the barium (II), titanium (IV) and oxygen signals in the appropriate stoichiometric ratio of BT, similar to those already reported in ref. [14].
The surface color inhomogeneities of the coating observed both optically and by Raman spectroscopy were further investigated using Auger electron spectroscopy (AES). Figure 3 shows an AES spectra from the lower surface (a, b and c) and from the top surface (d) of a sample in the first derivative representation. Spectrum a) was recorded from a film-free region, showing some carbon contamination, the titanium and the oxygen AES peaks, and only traces of barium, hardly visible in the as-recorded data. The reader must be aware that the spectrum is in the dN/dE mode and not in the d(NE)/dE mode, therefore the barium amplitude appears smaller than in most published spectra. The BT film is represented by curve b), where a larger amount of barium and a lower carbon content was observed. Curve c) was recorded from a small spot inside a film-coated region. The larger amount of carbon suggests some carbonates coexisting with the BT film. Spectrum d), recorded on a dark spot on the top side of the sample, displayed only traces of titanium, but clear peaks from carbon, oxygen and barium. We suggest that this corresponds to precipitation of barium carbonate and that no BT nucleation occurred on the upper side of the metal foil.

|
Figure 3. Auger electron spectra in the dN/dE mode recorded from a) a film-free region, b) a BT film, c) a spot inside a film, and d) a spot on the top of the sample where no film growth was observed (sample placed horizontally).
|
Titanium Foils Placed Vertically
Titanium samples placed vertically and treated in Ba(OH)2 exhibited homogeneous films with colors ranging from violet to dark blue. Figure 4 is an XRD record showing the (110) reflection of BaTiO3, whereas the inset is a high resolution scan of the (110) reflection exhibiting no splitting, thus identifying the material as cubic instead of tetragonal, as is usual in hydrothermally derived films [2]. Figure 5 is a SEM micrograph exhibiting the characteristic microstructure of films grown from solution, similar to those reported in ref. [2] and by other authors. All of the films seemed to be similar to those grown by standard hydrothermal processing in pressurized vessels. The average film thickness of several samples was determined by the weight loss method, i.e., by weighing a coated strip before and after removing the film with hydrochloric acid. The mass changes around 0.05 mg for samples around 2 cm2. Assuming for the film the bulk density of 5.85 g/cm3, the average film thickness was around 50 nm, with an error of 2 nm associated to the determination of the mass change. Probably the largest but unknown error was assuming the bulk density for the film.
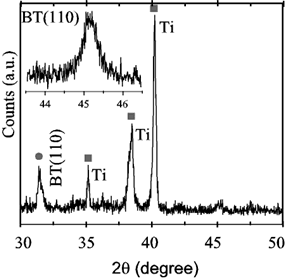
|
Figure 4. XRD spectrum of Ti foils treated at 130ºC. Inset: high resolution scan of the (110) reflection.
|
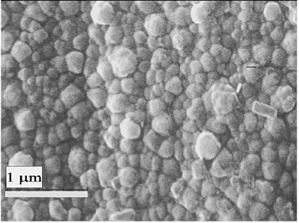
|
Figure 5. SEM micrograph of a BaTiO3 film made by the localized hydrothermal method (vertical position).
|
A titanium foil placed in Sr(OH)2 grew a golden colored film that exhibited reflections from titanium dioxide, but not from SrTiO3 under XRD examination. However, strontium incorporation was observed by XPS. The color of the coatings coincided with those observed by Pilleux et al. in hydrothermally grown SrTiO3 films on Ti foils [15].
Titanium foils treated in saturated solutions of Ca(OH)2 exhibited similar golden coloration, but did not show the expected CaTiO3 reflections under XRD, which were also not reported by Hamada et al. after two hours of conventional hydrothermal treatment at 121ºC [16]. Surface incorporation of calcium was detected by XPS, which in some cases was observed even after erosion by argon ions, consistently with the observations of ref. [16]. This suggests that calcium titanate growth requires longer times, probably because of the lower concentration of Ca2+ ions in the saturated Ca(OH)2 solution. It seems that the temperatures presently used are not high enough to grow the crystalline CaTiO3, which can be made under conventional hydrothermal processing at 200ºC [17].
Zirconium and Niobium Foils Treated in Ba(OH)2
Zirconium foils treated as described in Table 1 did not show barium incorporation under XPS and only exhibited reflections from ZrO2 under XRD examination. This is consistent with other reports, since BaZrO3 growth requires hydrothermal treatments above 200ºC [6].
Niobium foils treated as reported in Table 1 exhibited a golden coloration. Barium was incorporated at least a few tens of nanometers, as shown by XPS assisted with argon ion sputtering. The quantitative estimate provided by XPS was close to the nominal composition of NbBa2O7. On the other hand, a large amount of reflections were found by XRD (not shown). Some of them corresponded to niobium oxide, but none of them to the tabulated oxides of the Ba-Nb-O composition. Since to our knowledge there are no reports on the growth of Ba-Nb-O films by hydrothermal techniques, it is not possible to make any definitive statement at the present time with regards to the growth of niobate films by these methods.
Conclusions
We have demonstrated a new procedure for growing BaTiO3 thin films on metallic titanium using “Localized Hydrothermal Growth”. This technique involves partial heating of only the metallic substrate inside an aqueous solution with alkali-earth ions at temperatures as high as 130ºC at atmospheric pressure. This technique uses an extremely simple and low energy consumption experimental setup that has not been previously reported for the fabrication of perovskite thin films. The technique failed to grow films on zirconium substrates, which can be readily grown by the conventional hydrothermal and electrochemical-hydrothermal methods.
|
Titanium*
|
30x10x0.130
|
540
|
52
|
Ba(OH)2 0.25M
|
BaTiO3
|
Titanium
|
37x10x0.030
|
540
|
26-51
|
Ba(OH)2 0.25M
|
BaTiO3
|
Titanium
|
37x10x0.030
|
540
|
25
|
Sr(OH)2 0.25M
|
No SrTiO3 film
|
Titanium
|
37x10x0.030
|
540
|
25
|
Ca(OH)2 sat
|
No CaTiO3 film
|
Niobium
|
37x10x0.025
|
160
|
39-46
|
Ba(OH)2 0.25M
|
See text
|
Zirconium
|
37x10x0.020
|
440
|
26-56
|
Ba(OH)2 0.25M
|
Zirconium oxides
|
*This set of samples was positioned horizontally and exhibited film growth on the lower side only.
Acknowledgements
The present work was supported by the Chilean government under grants FONDAP 11980002 and FONDECYT 3990042, and by Fundación Andes under grant C-13680/5. We acknowledge the help of Mr. J. Ampuero in recording the XRD data and the assistance of Mr. J. P. Wiff in performing hydrothermal experiments. We were able to collect Raman data thanks to the technical expertise of Dr. J. Baier. We also thank grant FONDEF D97F1001 for financing the acquisition of the Micro-Raman system.
References
1. M. Yoshimura, W. Suchanek, and K. Byrappa, "Soft solution processing: A strategy for one-step processing of advanced inorganic materials", MRS Bull., 25 (9) (2000) 17-25.
2. M. Yoshimura, S. E. Yoo, H. Hayashi, and N. Ishizawa, "Preparation of BT Thin Film by Hydrothermal-Electrochemical Method", Jpn. J. Appl. Phys., 28 (1989) L2007-2009.
3. M. Yoshimura and W. Suchanek, "In Situ Fabrication of morphology-controlled advanced ceramic materials by Soft Solution Processing", Solid State Ionics, 98 (1997) 197-208.
4. M. E. Pilleux, C. R. Grahmann V. M. Fuenzalida and R. E. Avila, "Hydrothermal ABO3 Ceramic Thin Films", Appl. Surf. Sci., 65/66 (1993) 283-288.
5. S-W. Song, K-S Han, I. Sasagawa, T. Watanabe, and M. Yoshimura, "Effect of LiOH concentration change on simultaneous preparation of LiCoO2 film and powder by hydrothermal method", Solid State Ionics, 135 (2000) 277-281.
6. V. M. Fuenzalida and M. E. Pilleux, "Hydrothermally Grown BaZrO3 Films on Zirconium Metal, Microstructure, XPS and AES Depth Profiling", J. Mater. Res., 10 (1995) 2749.
7. P. Bendale, S. Venigalla, J. Ambrose, E. Verink, and J. Adair, "Preparation of barium titanate films at 55ºC by an electrochemical method", J. Am. Ceram. Soc., 76 (1993) 2619-2626.
8. T. Hoffmann, M. Gültzow, C. M. Sotomayor-Torres, Th. Doll, and V. M. Fuenzalida, "Microstructures in BaTiO3 thin films by hydrothermal growth and lift-off technique", Mater. Sci. Semicond. Process., 2 (1999) 335-340.
9. K. Kuroda, R. Ichino, M. Okido and O. Takai, "Hydroxyapatite coating on titanium by thermal substrate method in aqueous solution", J. Biomed. Mater. Res., 59 (2002) 390-397.
10. Judit G. Lisoni, C. H. Lei, T. Hoffmann and V. M. Fuenzalida, "Hydrothermal Growth of BaTiO3 on TiO2 single crystals", Surf. Sci., 515 (2002) 431-440.
11. W. Suchanek, T. Watanabe, and M. Yoshimura, "Preparation of BaTiO3 Thin Films by the Hydrothermal-Electrochemical method in the flowing solution", Solid State Ionics, 109 (1998) 65-72.
12. W. L. Suchanek, M. Oledzka, K. Mikulka-Bolen, R. L. Pfeffer, M. Lenka, L. McCandlish, and E. E. Riman, "Hydrodynamic Effects in Hydrothermal Syntesis of Lead Zirconate Titanate Powders And Epitaxial Thin Films", in Proc. 5th Int. Conf. on Solvo-thermal Reactions, 22-26 July 2002, East Brunswick, NJ.
13. P. Valverde, "Influence of Potential and Concentration on the Hydrothermal-Electrochemical Synthesis of BaTiO3", Thesis, Universidad de Santiago de Chile, Santiago, Chile, 1999 (in Spanish).
14. S. Escobar, C. I. Silva, T. Vargas, and V. M. Fuenzalida, "Nucleation and Inhibition Control during the Hydrothermal-Electrochemical Growth of Barium Titanate Films", J. Am. Ceram. Soc., 83 (2000) 2673-2676.
15. M. E. Pilleux, C. R. Grahmann and V. M. Fuenzalida, "Hydrothermal SrTiO3 films on titanium: XPS and AES study", J. Am. Ceram. Soc., 77 (1994) 1601-1604.
16. K. Hamada, M. Kon, T. Hanawa, K. Yokoyama, Y. Miyamoto, and K. Asaoka, "Hydrothermal modification of titanium surface in calcium solutions", Biomaterials, 23 (2002) 2265-2272.
17. M. Yoshimura, W. Urushihara, M. Yashima, and M. Kakihana, "CaTiO3 coating on TiAl by hydrothermal-electrochemical technique", Intermetallics, 3 (1995) 126-168.
Contact Details
Víctor M. Fuenzalida
Universidad de Chile, Fac. Cs. Fís. y Matem., Casilla 487-3, Santiago 651.1226,
Chile
E-mail: [email protected]
|
Boris Chornik
Universidad de Chile, Fac. Cs. Fís. y Matem., Casilla 487-3, Santiago 651.1226,
Chile
|
Rodrigo A. Espinoza
Universidad de Chile, Fac. Cs. Fís. y Matem., Casilla 487-3, Santiago 651.1226,
Chile
|
Mauricio E. Pilleux
NRAO - Associated Universities, Inc.
|
Marcelo E. Robles
Universidad de Chile, Fac. Cs. Fís. y Matem., Casilla 487-3, Santiago 651.1226,
Chile
|
Ramón A. Zárate
Universidad Católica del Norte,
Antofagasta,
Chile.
|
Alejandro L. Cabrera
Pontificia Universidad Católica de Chile, Facultad de Física, Santiago,
Chile.
|
|
|