Introduction To reduce air pollution and save energy consumption, the application of magnesium alloys, having a low density of 1.8 kg/m3, is very favorable due to their contribution to the reduction of inertia. However, magnesium alloys have low wear resistance and hardness, and sticking or seizure phenomena easily occur with the counter materials. No self-lubricant is contained in the matrix. In the previous work, magnesium matrix composites with in-situ formed Mg2Si dispersoids were developed via solid-state reaction process, when employing the elemental mixture of magnesium alloy and silicon powder [1]. Mg2Si shows high hardness of 350~700 Hv, high Young’s modulus of 120 GPa and a low density of 1.9 kg/m3 [2,3]. This study reports the tribological properties of these magnesium composite alloys under wet conditions, i.e., a wear test carried out in an oil lubricant. In particular, the effect of Mg2Si content of the composites on the friction coefficient is evaluated. Experimental Pure magnesium powder with a mean particle size of 112 μm and a purity of 99.9% and AZ31 (Mg-3Al-1Zn/mass%) alloy powder with that of 199 μm are employed as raw materials for the matrix. Si and SiO2 powders, having a mean particle size of 22 and 21 μm respectively are used to form Mg2Si via solid-state reaction with the above matrix raw materials. In the latter, not only Mg2Si but also MgO is synthesized by the deoxidization process [4]. The elemental mixture of each powder, having the content of Si from 0 to 10 mass% and that of SiO2 from 0 to 8 mass% respectively, is consolidated by the conventional cold compaction with an applied pressure of 600 MPa. Mg2Si forms between raw powders during heating the green compact at 853 K for 240 s in nitrogen gas atmosphere. The heating temperature is decided by the differential scanning calorimeter (DSC) because the formation of Mg2Si accompanies exothermic heat. After heating the green compact, it is immediately consolidated into full density by hot forging or hot extrusion. In the former, a pressure of 800 MPa is loaded to the green compact in the die heated at 573 K. Furthermore, an extrusion ratio of 26 and a die temperature of 673 K are employed to fabricate the magnesium composites with a diameter of 8.2 mm. Ultimate tensile strength (UTS), Yield Stress (YS) and elongation of each composite are evaluated at room temperature. Pin-on-disk type wear test equipment was used for evaluation of tribological properties. S35C carbon steel was employed as a disk specimen. The pin and disk specimens were sunk in motor oil 10W30. Sliding speed was 1 m/s and step-wise loading with a gradient of 1 N/s was applied up to 500N to the pin specimen. The friction coefficient during wear test was calculated. The optical observation of the sliding surface and its roughness of each specimen after test were examined. Results and Discussion Structural Analysis and Microstructures Figure 1 shows X-ray diffraction (XRD) patterns of hot forged magnesium composites in using Si particles (a) and SiO2 (b). Figure 1 (a) shows Mg2Si peaks but no Si peak. The peak intensity of Mg2Si increases with an increase in the content of Si particles of raw materials. Furthermore, DSC analysis on each forged specimen shows no exothermic heat, that is no synthesis of Mg2Si during heating. Accordingly, Si particles are completely reacted with magnesium powder to form Mg2Si, and it is dispersed in the matrix. Figure 1 (b) also indicates the same result in synthesizing Mg2Si and MgO, when using SiO2 particles. Figure 2 shows the optical microstructure of hot extruded AZ31 composites with Mg2Si dispersoids, in employing AZ31-7.5mass%Si mixture as input materials. They are uniformly distributed in the matrix, and their mean particle size is almost the same as that of Si particles because there is no remarkable coarsening during solid-state synthesis of Mg2Si dispersoids. 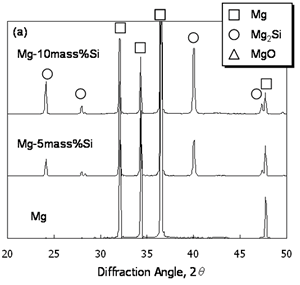 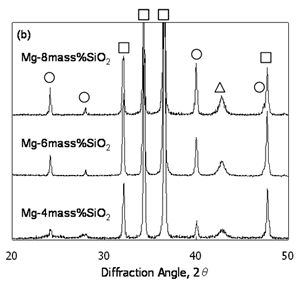 | Figure 1. XRD Patterns of hot forged magnesium composites with in-situ formed Mg2Si dispersoids. | | 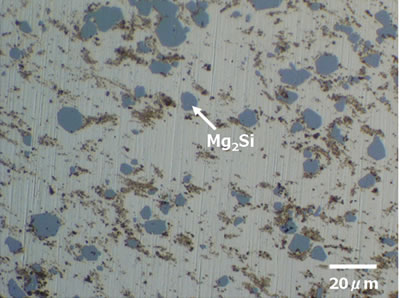 | Figure 2. Optical Microstructure of hot extruded magnesium composites with Mg2Si dispersoids, in employing elemental powder of AZ31-8mass%Si. | Mechanical properties of magnesium composite alloys Figure 3 shows the dependence of UTS and YS of magnesium composites on the content of Si or SiO2. UTS and YS gradually increase with increase in content of the additives. It means that the dispersion strengthening of the magnesium composites by Mg2Si or Mg2Si /MgO is effective because, as mentioned above, they are fine and uniformly dispersed in the matrix. 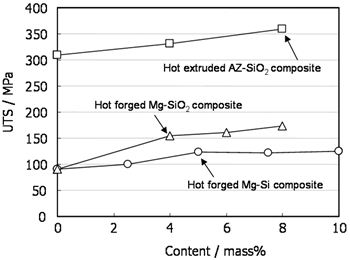 | Figure 3. Dependence of UTS magnesium composites with Mg2Si dispersoids on Si or SiO2 content of raw materials. | Tribological properties of magnesium composite alloys Figure 4 shows the dependence of friction coefficient (μ) on the applied load of the magnesium composite with Mg2Si dispersoids. At the initial stage in applying small load until about 250 N, every magnesium composite indicates the decrease of μ value, however it increases again with an increase in load. This corresponds to “Stribeck diagram”, which means the μ value is proportional to both the viscosity of oil lubricants and the inverse of applied load, on the tribological behavior under wet conditions. The reduction of μ value at the initial stage is due to a thick oil film existing between the pin and disc specimens. The friction torque also strongly depends on the force to break them, in other word, the viscosity of the oil lubricant. In increasing the applied load, the oil lubricant is removed between the contacting surfaces, and the thin oil film reduces the friction torque. That is, elasto-hydrodynamic lubrication (EHL) dominates the friction mechanism at the initial stage in applying a small load. However, when the applied load is over 250-400 MPa, each friction coefficient increases again. This is because the mechanical contact between both specimens occurs after the breakage or removal of the oil films. In particular, the magnesium composite including the silicon content of 10 mass% reveals the smaller load to increase the friction coefficient; for example at 250 N. It means that the breakage of the oil lubricant films easily occur compared to the other composites. That is, Mg2Si dispersoids protruded from the sliding surface of the pin specimen seem to effect the breakage of the oil films. 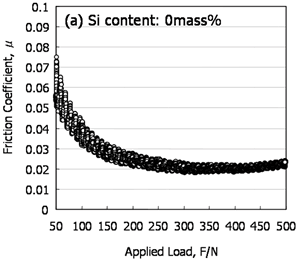 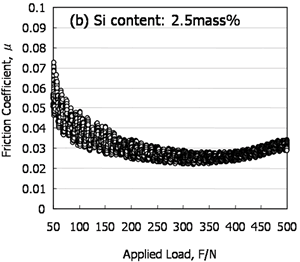 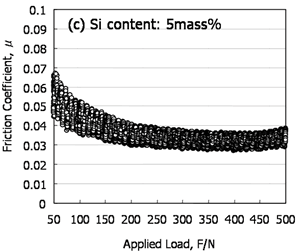 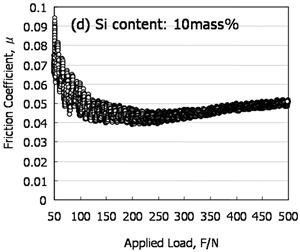 | Figure 4. Changes in friction coefficient during wear test as a function of applied load, Si content of 0% (a), 2.5% (b), 5% (c) and 10% (d). | Furthermore, Figure 5 indicates changes in the μ value at 500 N loading as a function of the silicon content of the raw materials. It increases proportionally to the Mg2Si content. In general, there are two factors to increase the μ value; one is an abrasive wear due to the attacking or plowing by the hard particle and another is an adhesive wear due to sticking or seizure phenomenon. The observation on the damages of the sliding surface is available to discuss what the dominant factor is, that is, to clarify the wear mechanism. Figure 6 shows the optical observation results on the damaged surface of each specimen after wear test. The sliding surface of every pin specimen shows a slight wear tracks by an abrasive wear. However, the damages of the disc specimens are quite different to each other. It is clear that the damaged area (attacked tracks by pin specimens) due to a plowing wear increases with an increase in silicon content. Furthermore, as shown in Figure 7, the in-situ monitored total wear also increases after increasing silicon content. That is, the attacking or plowing by the Mg2Si dispersoids protruded from the pin specimen surface increases the wear of the counter materials. Considering these results, Figure 8 illustrates the wear mechanism in using the magnesium composite with Mg2Si dispersoids under wet conditions. The increase of the friction coefficient at a large load is caused by the abrasive wear due to the plowing by Mg2Si dispersoids of the pin specimen under EHL condition because the dispersoids, having micro-hardness of about 600-700 Hv, are much harder than the S35C mild steel counter material with that of 100-120 Hv. 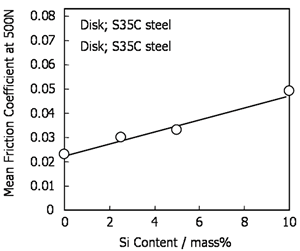 | Figure 5. Dependence of mean friction coefficient at 500N under wet conditions on Si content of raw materials. | 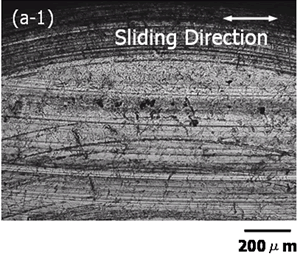 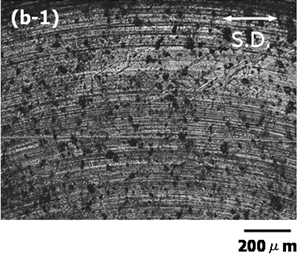 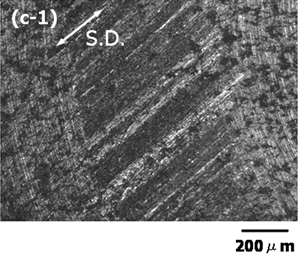 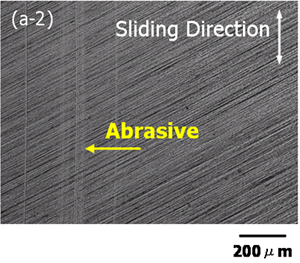 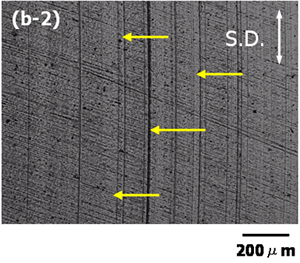 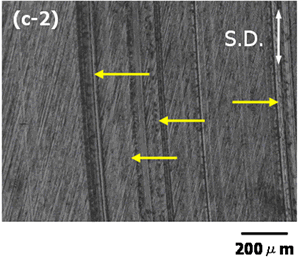 | Figure 6. Optical observations on sliding surfaces of pin specimens (magnesium composite with Mg2Si) and S35Ccounter materials under oil lubricant; Si content of 0% (a), 5% (b) and 10% (c). (Upper; pin, Lower; disk). | 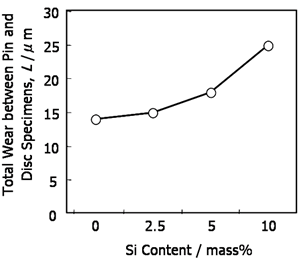 | Figure 7. Effect of Si content of magnesium composites on total wear of specimens. | Conclusions The mechanical and tribological properties of magnesium composites with Mg2Si dispersoids synthesized from the elemental powder mixture of Mg-Si or Mg-SiO2 via solid-state reaction were investigated. The UTS of the composite increases with increase in the Si content because of the dispersion strengthening effect of fine Mg2Si particles distributed uniformly in the matrix. The friction coefficient between the magnesium composite and S35C counter material increases with an increase in Mg2Si content, when wear test is carried out in an oil lubricant. This is because hard Mg2Si dispersoids attack the surface of the counter material. Acknowledgements Many thanks for experimental help by Mr. Muramatsu, a graduate student of Musashi Institute of Technology (current: Toho Titanium Co. Ltd). This work is financially supported by Kanagawa Academy Science and Technology (KAST) in Japan. References 1. K. Kondoh, R. Tsuzuki and T. Aizawa, “Magnesium Matrix Composite with Solid-state Synthesized Mg2Si Dispersoids”, Mater. Trans., 44 (2003) 611-618. 2. L. F. Mondolfo, “Alunimum Alloys: Structure and Properties” Butterworths, London (1976) pp.566. 3. C. C. Koch, "The Synthesis and Structure of Nanocrystalline Materials Produced by Mechanical Attrition: A Review," Nanostruct. Mater., 2 (1993) 109-129. 4. K. Kondoh, H. Oginuma, E. Yuasa and T. Aizawa, “Solid-State Synthesis of Mg2Si from Mg-Si Mixture Powder”, Mater. Trans., 42 (2001) 1293-1300. Contact Details |