Introduction Elasticity is a property possessed by many solid materials, but the class of materials known as rubbers or elastomers possess a different property called high elasticity. This differs from conventional Hookean elasticity in that it exhibits much higher values of elongation at break, up to 1000% or more. This huge value for elongation at break means that many of the other properties measured in the accepted manner for metals show interesting variations. Tensile strength, for example, although still calculated in the usual way using the initial cross sectional area, will give values much lower than the true stress in the material because the actual cross section at break will be approximately one tenth of the original value. Another important point is that, over the elongation at break range, the slope of the line varies substantially, giving typically an S-shaped curve, so that the normal engineering term of modulus becomes meaningless. Rather confusingly a description of the relative stiffness of the rubbery materials, frequently used, is also called 'modulus'. This is simply a measure of the load at a given elongation, e.g. 'modulus at 300%' is simply a stress value for the material at an elongation of 300% (i.e. at four times the original length). Although 300% is a commonly used value, a range of extensions is used to give 'modulus' values relevant to different applications. In the context of rubbers and elastomers modulus refers to this rubber property. High Elasticity or Rubbery Elasticity Elastomers are materials of a very high molecular weight, generally composed of one or more monomers polymerised or co-polymerised together to form a polymer (or copolymer). The polymer consists of a very long chain of monomer molecules chemically bonded together to form a single molecule with a molecular weight of several million. This large molecule, which will consist of several tens of thousands of the small (monomer) units bound together. It has a very large length to diameter ratio (often more than 10,000 to 1) and does not exist as a straight rod-like structure, but in a form known as a random coil. In a raw uncompounded polymer, each random coil will be entangled with many neighbours making flow difficult. The mass behaves like a liquid but with a viscosity some five million times that of water, but will eventually flow under the effects of stress and temperature. Flow under stress is a severe limitation to the industrial utilisation of plain elastomers. It can be overcome by cross-linking. In this process the random coils are tied or cross-linked to others at intervals randomly along their length. This is achieved by reaction with added chemicals assisted by heating to 150 to 200°C. The resultant mass still exhibits the characteristic high elongation and modulus behaviour because lengths of random coil between cross-links can still straighten under load. The extent of elasticity will depend upon the length of random coil between cross-links. A heavily cross-linked polymer will exhibit lower extensibility and higher stiffness than a lightly cross-linked example. A simple indentation hardness test is used to characterise blends for industrial applications. Range of Properties Rubber materials in use are required to have a wide range of properties, from very soft to very hard. These are generally obtained by the compounder, using a base polymer or polymer blend to give essential properties such as strength, ageing and environmental resistance, then modifying hardness and modulus properties using additives such as fillers to achieve a suitable compound. Compounds containing only a vulcanising (cross-linking) system are generally known as gum compounds and generally have a density close to 1.0. Their modulus is affected by both the cross-link density and the ambient temperature. Cross-link density must be kept between limits to ensure that ‘rubbery’ properties are retained. The modulus shows an almost linear increase as the cross-link density increases but is mainly manipulated for engineering purposes by use of relatively large quantities of solid particulate materials called fillers. These range from cheap, inert materials such as washed clays and Whitings (calcium carbonates) to active, property enhancing materials, by far the most common being Carbon Black. This is why engineering rubber compounds tend to be black in colour. By using a range of type, volume fractions, and particle sizes of black, perhaps in conjunction with other fillers, the shear modulus (G) of the compound can be varied over the approximate range 0.3 to 2.5 MNm-2. Hardness Rubber hardness is measured, like metals, by an indentation method. The normal UK method is to use International Rubber Hardness Degrees (IRHD). Values range from about 30 for a soft gum rubber to about 85 for a highly filled material. There is an almost linear relationship between Youngs Modulus and IRHD. Physical Properties The physical properties of a rubber compound have a complex dependence on the cross-link system, cross-link density, and the type and quantity of filler, but in general can be represented as in figure 1. 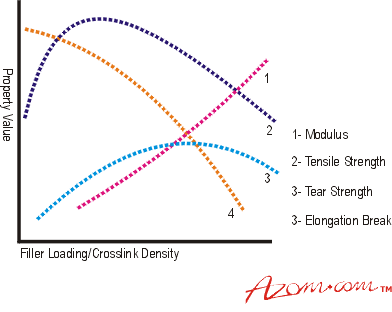 | Figure 1. How an elastomer’s properties vary with filler loading or cross-linking density. | As the article deforms under a steadily increasing tensile stress its behaviour is not linear. The curve obtained is a characteristic S curve, see Figure 2. 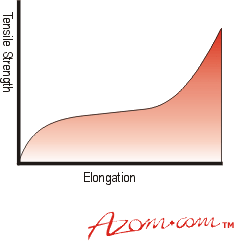 | Figure 2. Typical tensile behaviour of an elastomer. | However, the material behaves almost linearly in shear or compression deformation, figures 3a and 3b. 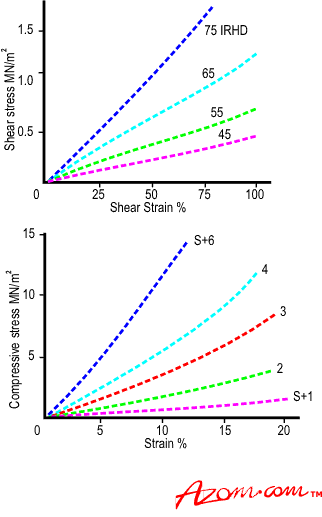 | Figure 3. (a) Typical shear behaviour of an elastomer and (b) typical compression behaviour of an elastomer.. | The early part of the Tensile curve is linear and the gradient of this is taken as a measure of the Youngs Modulus of the material (E). The Shear modulus, which can also be measured independently, can be shown to be one third of this value for a simple gum rubber network. The Shear modulus (G) ranges from about 0.3 MNm-2 upwards. For filled materials G can increase to about 2.5MNm-2, but E values then increase to 4 to SG. The Bulk (compressive) Modulus has the relatively high value of 1000 to 1300 Mm-2 and elastomers can be regarded, like most liquids, as effectively incompressible in a closed system. 1f the sample is relaxed before failure occurs the return stress strain curve follows closely the outward path, i.e. almost all the energy absorbed by the sample is returned on relaxation. This low level of energy loss (low hysteresis) in a cycle of deformation can be particularly useful. Rubber compounds can he used to isolate vibrating bodies (usually engines of all types), and the energy loss per cycle of vibration, although appearing in the rubber as heat, can be controlled by compound selection so that the bearing does not overheat. One unique property of high quality rubber compounds is that high stresses can be sustained over a wide range of elongation, thus the area underneath the stress strain plot is high, and a considerable amount of energy can be absorbed before the sample fails. All cross-linked polymers under stress suffer from stress relaxation or creep as the article undergoes small internal changes such as breaking (and possibly reforming) of individual cross-links suffering the highest stress levels. This is inconvenient but is fortunately quite predictable (linear against log time) and properly formulated Natural Rubber compounds can have very low creep rates (of the order of 2% per decade of time). Glass Transition Temperature (Tg) Elastomers have limited performance generally if a wide range of temperatures are considered. Low temperatures increase stiffness, and at a characteristic temperature called the Glass Transition temperature (Tg) the material loses all rubbery properties and becomes ‘glassy’, with characteristically brittle properties. The Tg for NR is about -72°C, lower than most synthetics, but applications involving arctic environments need careful testing. Many elastomers become progressively `leathery' as they cool towards Tg, their use in this state is not recommended. Crystallisation Under certain conditions some elastomers can ‘crystallise’. This is not usually desirable as it interferes with rubbery properties and occurs at temperatures well above Tg. Crystallisation involves segments of a random coil coming into close proximity to a neighbouring coil allowing areas of high organisation (crystallites) to form within the bulk. It is not possible particularly with cross-linked polymers, for the whole mass to be crystalline and a ‘percentage crystallinity’ figure is used to describe the condition, which varies with polymer structure, level of orientation, and temperature. The stiffening (increased modulus) effect becomes evident as ambient temperature reduces, and can manifest itself over long periods of time. The effect, however, is completely reversible if the temperature increases. Vulcanised Natural Rubber also suffers from crystallisation at high levels of extension when polymer chains are in sufficiently close alignment to enable associations to form, this is useful in resistance to cutting and tearing. However, normal usage of NR in applications in compression or shear will not produce this type of crystallinity. Chloroprene rubbers have a higher tendency to crystallise and can show stiffening (modulus increase) with ageing in service. The type of cross-linking system used can have marked effects on long term performance, and even NR compounds can show stiffening on exposure to temperatures below 10°C, which is commonly experienced in many parts of the world. Higher Temperature Effects High temperatures generally increase the rate of ageing (degradation of properties with time) due to the environment. Temperatures of the order of 120°C, typical of automotive under bonnet temperatures, are quite severe for many common elastomers and careful selection of compounds is necessary for satisfactory performance. |