Feb 20 2006
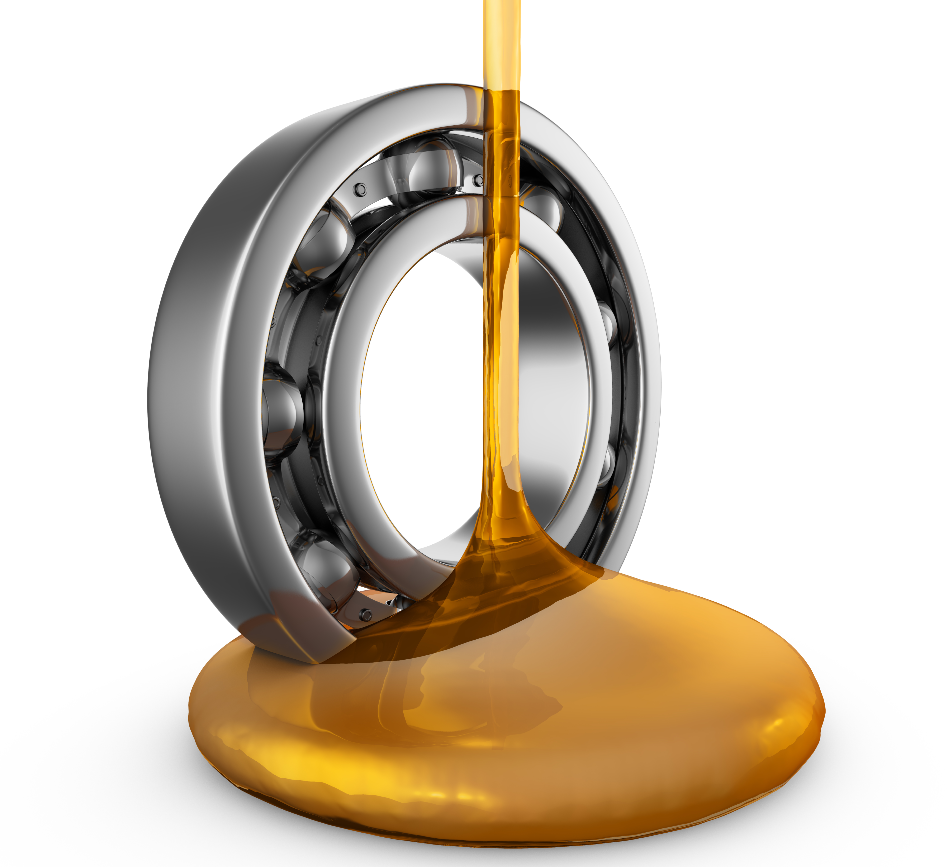
rommma / Shutterstocl
The term “tribology” comes from the Greek word “tribo” meaning rubbing and “logy” meaning knowledge. The Greeks first applied tribology when they were attempting to understand the motion of large stones across the surface of the earth. Nowadays, tribology has expanded to include the systematic study of lubrication, friction, and wear.
Tribology has a critical role to play in various technological areas. In the sophisticated technology industries of data storage and semiconductor, tribological studies help enhance polishing processes and lubrication of data storage substrates. In conventional industries such as aerospace and automotive, tribological studies help boost the lifetime of mechanical components.
Lubricants
A number of industrial processes need a comprehensive understanding of tribology at the nanoscale. Lubricant development in the automobile sector is governed by the adhesion of nanometer layers (monolayers) to a material surface. The assembly of components can rely critically on the adhesion of materials at the nanoscale.
Friction and Wear
Many conventional tools are available for characterizing lubrication, friction, and wear. The most typical characterization tool is the tribometer, which has numerous configurations such as a ball on flat, pin-on-disk, and flat on flat, etc. Producing motions at the nanoscale is very difficult. New characterization methods are needed to comprehend tribology at the nanoscale.
Studying Nanoscale Tribology
The atomic force microscope is currently being used as a standard for analyzing nanoscale tribology. The AFM’s natural extension for tribology applications is derived from the motion of a nano-sized stylus in the AFM over a surface. Conventional tribology testing is not carried out with an AFM, but several new kinds of applications are possible.
Listed below are examples of the application of AFM to tribology:
- Measurement of the thickness of liquid and solid lubricants that have nanometer or even monolayer thickness
- Direct 3D visualization of scars or wear tracks on a surface
- Measurement of frictional forces at the nanoscale
- Assessment of mechanical properties such as elasticity, hardness, and plastic deformation at the nanoscale
- Surface characterization of texture, morphology, and roughness
Materials Suited for Analysis
A key advantage of the AFM for tribological research is that the AFM can be regularly used on all varieties of materials. Materials that are generally examined include ceramics, polymers, metals, semiconductors, optical materials, magnetic materials, and biomaterials. AFM investigations are commonly performed under ambient conditions. AFM studies can be carried out in a liquid or vacuum environment.
Nanoscale Wear Analysis
The effects of wear at the nanoscale are critical to the stability and optimization of machines, as the tolerances in precision machines get minimized. Conventional microscopes like the optical and scanning electron microscopes enable visualization of wear in two dimensions. For instance, the SEM can be used to obtain an enlarged view of wear tracks in the x-y axis; however, cross-sectioning is necessary to measure the depth of wear tracks.
The AFM enables direct 3D visualization of scars and wear tracks. The images can be presented in a 3D projection and a 2D projection. Direct measurement of wear track depth can be simply performed using a line profile obtained from the AFM image.
Lubricant Studies
It is a known fact that layers of lubricants on surfaces measuring <100 nm can greatly influence lubrication behavior. Such films must be characterized to create enhanced lubricating films. However, the nanoscale characterization of lubrication films is considerably challenging.
Optical methods such as ellipsometers can be employed for measuring the lubrication thickness of large sections (>10 μm2) of a surface. Measurement of the localized (<1 μm) film thickness cannot be done with the ellipsometer.
In an AFM, the probe is placed at the end of a cantilever, thus enabling the measurement of interaction forces between the surface and the probe by observing the cantilever’s deflection. A graph, known as a force/distance curve, gives an account of the forces on the probe as the distance between the surface and the probe is shortened.
The nature of the force/distance curve is subject to the force constant of the cantilever, the probe geometry, lubrication density, and the lubrication thickness.
The thickness of lubrication films can be directly determined by measuring the changes in force/distance curves in an AFM.
Frictional Forces
Friction between two surfaces relies on the mechanical and chemical interaction between the surfaces. Variations in chemical composition resulting in friction can be measured using the AFM. The method for measuring these forces is known as lateral force, or frictional force microscopy.
When the probe moves over a surface in the AFM, variations in the chemical composition of the surface can result in torsions of the cantilever on which the probe is positioned. Consequently, the torsion of the cantilever is dependent on the friction between the surface and the probe.
Simultaneous Measurement of Topography and Friction Forces
The AFM can be used to measure topography and frictional force images at the same time. The topography image is obtained by tracking the vertical forces on the cantilever, and the friction image is obtained simultaneously by tracking the lateral motions of the cantilever.
Surface Texture/Morphology/Roughness
The AFM offers very high contrast on surfaces that are flat at the nanoscale. Optical and electron microscopes do not have the ability to resolve surface texture that can be measured using the AFM without any difficulty. Applications comprise line roughness measurements, the visualization of surface topography in both 2D and 3D perspectives, and area roughness measurements. All of the conventional area and surface roughness factors can be computed after the AFM image is obtained.
Nanoscale Mechanical Properties
Mechanical properties like hardness, stiffness, elastic modulus, and compressibility, as well as material characteristics such as plastic deformation and fracture, can be examined using the AFM.
Nano-hardness can be tested by directly pressing an AFM probe onto the surface of a sample. However, it is beneficial to use an instrument optimized for nano-indentation. The main benefit of the nano-indenter over an AFM for nano-hardness measurements is that calibrated measurements can be easily obtained using the nano-indenter.
AFM can be easily used to measure the 3D topography of indentations made with a nano-indenter. AFM images enable direct visualization of fracture behavior or material deformation.
Methods such as pulsed force mode can be used to measure the stiffness of a sample at a range of locations. This data can be used to develop a stiffness mapping of a surface. Stiffness maps can only be developed on samples with a surface stiffness less than the stiffness of the cantilever. Such stiffness images are regularly measured on polymer samples.
Incorporating a fixture to the stage of the AFM enables the examination of material behavior, such as plastic deformation and fracture. The fixture allows forming forces on a sample while AFM images are being captured. A range of materials can be studied using such a method.