A cutting edge developer of scientific instrumentation was sourcing a small diameter ceramic bobbin requiring concentricity to three microns on a tiny axial bore. Although high electrical and wear resistance were required, there was indecision over specifying YTZP zirconia or 99+ alumina.
Advanced Ceramic Solution
With Insaco’s many years of machining experience with hardened materials, Zirconia was the recommended first choice for this application due to excellent impact resistance which might be vital with such a delicate design. However, being such a resilient material also makes diamond grinding tiny holes problematic and expensive. Alumina met all the stated requirements, and was the lower-cost alternative once machining costs were included. To help the user decide, the first prototype order was split over both materials, without cost penalty, to allow real application evaluation.
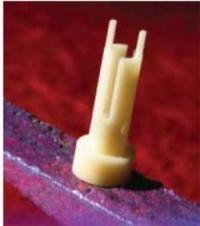
Figure 1. Precision machined alumina part
Result
Alumina more than exceeded performance requirements, and was lower in cost for both material and machining. Production requirements have now been formalized for fine-grained, 99.5% alumina, and reliability is proving excellent.
|
|
.jpg)
This information has been sourced, reviewed and adapted from materials provided by INSACO Inc.
For more information on this source, please visit INSACO Inc.