Introduction
Hybridization of different materials is an important concept of material design to develop new functional materials and high-performance materials. Ceramic matrix composites (referred to as CMCs) dispersed with metallic particles have great potential for high-temperature structural materials as functionally graded materials [1,2]. CMCs dispersed with nano-sized metallic particles have excellent mechanical properties at high temperatures [3]. However oxidation/corrosion properties of CMCs dispersed with metallic particles have not been clarified yet.
Exposing these composites into oxidizing atmosphere at high temperatures, metallic particles dispersed in the ceramic matrix are oxidized by mass transport though the ceramic matrix. When the metallic dispersoid is oxidized by inward diffusion of oxygen passing though the ceramic matrix, the metallic dispersoid is expanded by oxidation. Finally the matrix is fractured. Nanko et al. [4] reported the oxidation behavior of partially stabilized zirconia (PSZ) composites dispersed with nickel particles (Ni/PSZ) at temperatures raging from 600 to 800ºC. Since PSZ is a typical oxide ion conductor, nickel particles dispersed in the PSZ matrix are oxidized by oxide ions diffusing though the PSZ matrix. A cracked zone was formed due to high-temperature oxidation of Ni particles and grew with a constant rate.
Oxidation resistance is one of important properties for designing lifetime of CMCs dispersed with metallic particles for high-temperature applications. In order to understand oxidation properties of metal-dispersed ceramic composites systematically, the diffusion properties of the ceramic matrix should be focused. Here, two typical engineering ceramics are selected as a composite matrix with significant cation diffusivity.
Magnesium oxide, MgO, is an engineering ceramics with higher cation diffusivity than oxide ion. In addition, MgO is isomorphous with FeO and NiO, which are oxides of base-metals of heat-resistant alloys. By doping such transition metals in MgO, vacancy of Mg2+ ions and holes becomes primary defects. MgO composites dispersed with such heat-resistant alloys should be oxidized by diffusion of cations.
Aluminum oxide, Al2O3, is also a typical engineering ceramic with high mechanical strength with excellent thermal stability. Diffusion properties of Al2O3 are very complex and dominated by grain boundary diffusion [5-12]. Both cations and oxide ions can diffuse comparably.
The authors have investigated high-temperature oxidation of Ni-dispersed Al2O3 composites [13, 14] and MgO [15]. There are some phenomenological reports on high-temperature oxidation of Al2O3 composites dispersed with metallic particles [16-19]. In this paper, a role of cation diffusion in high-temperature oxidation of CMCs dispersed with metallic particles is discussed for understanding oxidation behavior of the ceramic composites at high temperatures.
Experimental Procedure
Powder of Al2O3 or MgO was mixed with an Ni powder with 10 µm in particle size in ethanol for 30 min by an Al2O3 mortar. Al2O3 powder mixed with Ni nano-particles was also prepared by reducing the powder mixture of Al2O3 and NiO made from Al2O3 slurry with Ni(NO3)2 aqueous solution, as described previously [14]. Volume fraction of Ni particles was 5 vol% for each ceramic composite. Their powder mixtures were sintered by the pulsed electric current sintering process. Density of the sintered samples reached at least 99 % of the theoretical value. The sintered samples were ground by using abrasive papers and polished by using 4µm diamond abrasive slurry.
The samples were exposed to air at 1300°C for 1 d. In the case of MgO matrix, the ZrO2 marker experiment was carried out by oxidation at 1300°C for 2d. Slurry made of ethanol and ZrO2 in 3 µm grain size was applied on the surface of the MgO composites. The oxidized samples were characterized by X-ray diffraction (XRD), scanning electron microscopy (SEM), and electron probe microanalysis (EPMA).
Figure 1 shows the cross-sectional view of MgO composites dispersed with Ni particles (refereed to as Ni/MgO) after oxidation. A region of 100 µm in depth includes no Ni particles and partially oxidized ones in deeper area. This region is defined as an oxidized zone. There are some voids in the oxidized zone. Since NiO is dissolved into MgO, an oxidation product of this compound is (Mg,Ni)O solid solution. Figure 2 shows the result of marker experiment for Ni/MgO oxidized at 1300°C for 2 d in air. ZrO2 powder is located in the inside of oxidized zone. The initial surface is located at 7 μm in depth from the current surface after oxidizing at 1300°C for 2 d.
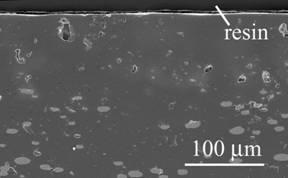
Figure 1. Cross-section of Ni/MgO oxidized at 1300ºC for 1 d in air.
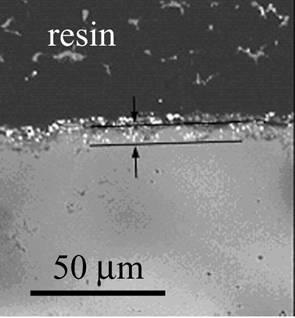
Figure 2. Cross-section of Ni/MgO with a ZrO2 marker oxidized at 1300ºC for 2 d in air.
Figure 3 shows the cross-section of Al2O3 composite dispersed with Ni particles (Ni/Al2O3) after oxidation. A region of 30 µm in depth includes no Ni particles and partially oxidized ones in deeper area (Figure 3 (a)). Based on XRD analysis and EPMA, the oxidation product was NiAl2O4 spinel, which was formed from oxidation of Ni involving Al2O3 matrix. In the oxidized zone, the oxidation product different to Al2O3 matrix and Ni particles in color can be observed. The voids are located inside of NiAl2O4. A continuous NiAl2O4 layer is also observed on the surface, as seen in Figure 3 (b).
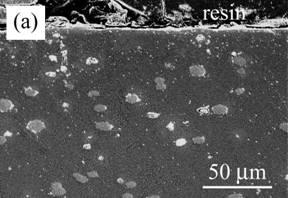
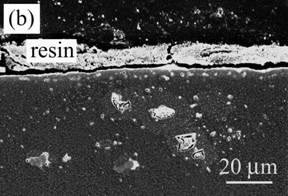
Figure 3. Cross-section of Ni/Al2O3 oxidized at 1300ºC for 1 d in air. (a) low magnification and (b) high magnification near the surface.
Figure 4 shows the cross-section of Al2O3 composite dispersed with Ni nano-particles (nano-Ni/Al2O3) after oxidation. The oxidation zone is approximately 100 µm in thickness, which is 3 times thicker than Ni/Al2O3. Fine voids of 1 μm size were observed in the oxidized zone. A continuous NiAl2O4 layer is also observed on the surface, as shown in Figure 4 (b).
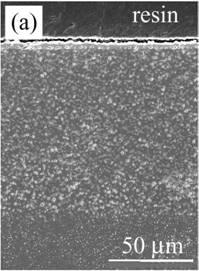
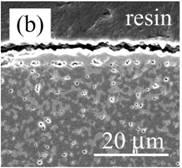
Figure 4. Cross-section of nano-Ni/Al2O3 oxidized at 1300ºC for 1 d in air. (a) low magnification and (b) high magnification near the surface.
Discussion
In the cases of Ni/MgO and Ni/Al2O3, no crack was generated by high-temperature oxidation. The formation of voids in the inside of oxidized zone is direct evidence of outward diffusion of cations to decrease volume expansion of Ni particles by oxidation.
Volume expansion of metals by oxidation can be calculated from the volume of its oxide. In the case of Ni, the volume change ratio, R, is:
(1)
where vi is molar volume of i. The value is so-called Pilling-Bedworth ratio [20]. However, outward diffusion of cations in the matrix means volume decrease in ceramic composite during oxidation. As an example, the oxidation reaction of Ni in the inside of Ni/MgO can be considered simply as follows:
(2)
where h+ means an electron-hole. The hole concentration of the oxidized zone is increased by doping NiO in MgO. Volume change per volume of Ni due to outward diffusion of cations can be estimated by:
(3)
This negative value means volume shrinkage, i.e., formation of voids in the inside of the oxidized zone. In the case of Ni/Al2O3, the ratio of outward and inward diffusion is not clear. In the case of Ni/Al2O3, contribution of cation diffusion can not be obtained quantitatively. Assuming that the flux of Al3+ is equal to the flux of O2-, the value of the total volume change is calculated as –1.13. Voids should be created in Ni/Al2O3 after oxidation.
The surface NiAl2O4 layer on Ni/Al2O3 is also a good evidence of outward diffusion of cations, in particular, Ni ions. In the case of Ni/MgO, the marker experiment revealed outward diffusion of cation during oxidation because the initial surface was located in the inside of oxidized zone.
For designing metal-dispersed ceramic composites, the matrix with significant contribution of cation diffusion is preferable to prevent the crack formation due to high-temperature oxidation. Dispersion with metal particles with submicrons to nanometers reduces void size in the oxidized zone. It is expected to reduce the degradation of mechanical strength of ceramic composites with metallic dispersoid due to high-temperature oxidation.
Summary
Prevention of crack formation due to high-temperature oxidation of a ceramic composite with metallic dispersoid can be achieved through significant cation diffusivity. However, voids form in the oxidation zone due to the volume change difference between oxidation of metallic dispersoid and reduction of the matrix in the inside of the composites. Since voids are very fine in nano-composites made of ceramic matrix with metallic nano-particles, it is expected to reduce the degradation of mechanical strength of ceramic composites with metallic dispersoid due to high-temperature oxidation.
Acknowledgements
The authors wish to express their gratitude to the Japanese government for partially supporting this work through the 21st Century Centers of Excellence (COE) Program of the Ministry of Education, Culture, Sports, Science and Technology.
References
1. S. Sampath, H. Herman, N. Shimoda and T. Saito, “Thermal Spray Processing of FGMs,” MRS Bull. 20 [1] (1995) 27-31.
2. A. Kawasaki and R. Watanabe, “Thermal Fracture Behavior of Metal/Ceramic Functionally Graded Materials”, Eng. Frac. Mech., 69 (2002) 1713-1228.
3. T. Sekino, T. Nakajima, S. Mihara, S. Ueda and K. Niihara, Interface Structure of Ceramic/Metal Nanocomposites”, in Ceramic Transactions: Materials Processing and Design: Grain-Boundary-Controlled Properties of Fine Ceramics II (Ed. K. Niihara, K. Ishizaki and M. Isotani), The American Ceramic Society, Westerville, OH, (1994) pp243-251.
4. M. Nanko, M. Yoshimura and T. Maruyama, “High Temperature Oxidation of Y2O3 Partially-Stabilized ZrO2 Composites Dispersed with Ni Particles”, Mater. Trans. 44 [4] (2003) 736-742.
5. Y. Oishi and W. D. Kingery, “Self-Diffusion of Oxygen in Single-Crystal and Polycrystalline Aluminum Oxide”, J. Chem. Phys., 33 [2] (1960) 480-486.
6. A. E. Paladino and W. D. Kingery, “Aluminum Ion Diffusion in Aluminum Oxide”, J. Chem. Phys., 37 [5] (1962) 957-962.
7. R. E. Mistler and R. L. Coble, “Rate-Determining Species in Diffusion-Controlled Processes in Al2O3”, J. Amer. Ceram. Soc., 54 [1] (1971) 60-61.
8. H. A. Wang and F. A. Kröger, “Chemical Diffusion in Polycrystalline Al2O3”, J. Amer. Ceram. Soc., 63 [11-12] (1971) 613-619.
9. K. Asaga and K. Hamano, “Initial Sintering Kinetics of Compacts of Apherical Alumina Particles”, Yogyo-Kyouai-Shi, 83 [3] (1975) 136-142.
10. K. Messaoudi, A. M. Huntz and B. Lesage, “Diffusion and Growth Mechanism of Al2O3 Scale on Ferritic Fe-Cr-Al Alloys”, Mater. Sci. Eng., A247 (1998) 248-262.
11. V. K. Tolpygo and D. R. Clarke, “Microstructural Evidence for Counter-Diffusion of Aluminum and Oxygen during the Growth of Alumina Scales”, Mater. High Temp., 20 [3] (2003) 261-271.
12. P. Y. Hou, X. F. Zhang and R. M. Cannon, “Impurity Distribution in Al2O3 Formed on an FeCrAl Alloy”, Scripta Mater., 50 (2004) 45-49.
13. M. Nanko, T. Nguyen Dang, K. Matsumaru and K. Ishizaki, “High Temperature Oxidation of Al2O3-Based Composites with Ni Particle Dispersion”, J. Ceram Proc. Res., 3 [3] (2002) 132-135.
14. M. Nanko, M. Mizumo, M. Watanabe, K. Matsumaru and K. Ishizaki, “High-Temperature Oxidation of Nano-Ni Dispersed Al2O3 Composites in Air”, Adv. Technol. Mater. Mater. Process. J, 6 [2] (2004) 240-243.
15. M. Nanko, A. Sakashita, K. Matsumaru and K. Ishizaki, “High Temperature Oxidation of MgO Composites with Ni Particle Dispersion”, Adv. Technol. Mater. Mater. Process. J, 6 [1] (2004) 43-46.
16. Ch. Laurent, X. Devaux, A. Rousset, J. High Temp. Chem. Proc., 3 (1994) 489-505.
17. A. Rousset, “Alumina-Metal(Fe, Cr, Fe0.8Cr0.2) Nanocomposites”, J. Solid State Chem., 111 (1994) 164-171.
18. Ch. Laurent, A. Peigney, O. Quénard and A. Rousset, “Synthesis and Mechanical Properties of Nanometric Metal Particles-Ceramic Matric Nanocomposites”, Sil. Ind., 63 (199) 77-84.
19. T. C. Wang, R. Z. Chen and W. H. Tuan, “Oxidaiton Resistance of Ni-Toughened Al2O3”, J. Euro. Ceram. Soc., 23 (2003) 927-934.
20. N. B. Pilling and R. E. Bedworth, “The Oxidation of Metals at High Temperature”, J. Inst. Met., 29 (1923) 529-582.
Contact Details
Makoto Nanoko
Department of Mechanical Engineering
Nagaoka University of Technology
Nagaoka, Niigata 940-2188, Japan
Email: [email protected]
|
Koji Matsumaru
Department of Mechanical Engineering
Nagaoka University of Technology
Nagaoka, Niigata 940-2188, Japan
|
Kozo Ishizaki
Department of Mechanical Engineering
Nagaoka University of Technology
Nagaoka, Niigata 940-2188, Japan
|
|
|