Rivets are primarily used for joining sheet metal components, for example in airplane construction. The joining of such materials in blind riveting is performed from only one side of the component. The blind rivet is inserted through a drilled hole, and the protruding mandrel is subsequently pulled out with a riveting tool. This process results in compression and broadening of the rivet on the opposite side of the drilled hole, and the protruding end of the mandrel then breaks off at the predetermined breaking point.
Blind rivet connections require good load carrying capacities and high clamping forces, and in order to achieve good static and dynamic stresses, a good, consistent rivet and mandrel strength is very important.
Each application demands the appropriate rivet, and the production of the blind rivets is adapted accordingly. The effect of different production parameters can now be easily tested with the new device from Zwick which determines the mechanical properties in accordance with EN ISO 14589.
The device includes tooling for tensile testing, shear testing, and for testing the fastening capability of the mandrel e.g. the mandrel press-out strength, and the mandrel breaking load. The testing device is modular in construction having different inserts for various rivet types and diameters. The testing devices are designed for maximum loads up to 50 kN and the hardened testing inserts guarantee a long life.
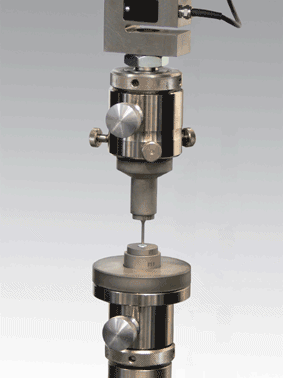
|
|
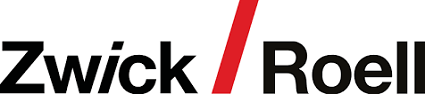
This information has been sourced, reviewed and adapted from materials provided by ZwickRoell GmbH Co. KG.
For more information on this source, please visit ZwickRoell GmbH Co. KG.