Established in 1938, Carbolite has over 60 years experience in the design & manufacture of electric laboratory & industrial furnaces, laboratory & industrial ovens & incubators.
During this time, Carbolite has established an enviable reputation for its ability to design and manufacture quality products for standard & special applications for laboratory, pilot scale & industrial applications.
Laboratory Furnaces
The extensive portfolio offered by Carbolite includes both laboratory chamber furnaces & laboratory tube furnaces to 1800°C. Tube furnaces are available as single or multi-zone, horizontal/vertical, split & rotating models. A wide variety of tube diameters & tube heated lengths is available. Chamber furnaces are available in many sizes; models include high temperature furnaces, ashing/calcining furnaces, furnaces for the analysis of coal & coke and precious metals evaluation furnaces (cupellation/fire assay).
Industrial Furnaces
In addition to the range of electric laboratory furnaces, ovens and incubators, Carbolite also offers an extensive range of pilot plant and industrial furnaces and industrial ovens for various heat treatment applications. Product ranges include:
- Mesh belt furnaces
- Roller hearth furnaces
- Rotary hearth furnaces
- Top loading furnaces
- Top hat furnaces
- Blade strip hardening furnaces
- Elevator hearth furnaces
The range of industrial ovens includes both batch and continuous ovens. Examples of these are aluminum solution ovens, bogie hearth ovens, air recirculating chamber ovens and inert atmosphere ovens.
Industrial Aluminium Solution Treatment Ovens
Carbolite offers a range of aluminium solution treatment ovens. These include:
- Industrial Drop Bottom Aluminium Solution Treatment Oven
- Industrial Solution Treatment and Ageing Ovens
- Front Loading Aluminium Treatment Oven With Quench
Industrial Drop Bottom Aluminium Solution Treatment Oven
- A specially designed industrial oven for solution treatment of thin aluminium alloy panels with minimal temperature loss between the heating cycle and quenching
- The oven processes a wide variety of skin panels up to a max size of 3 x 2m.
- As the maximum thickness of the material is only 1.6mm, quenching must be within 5 seconds of leaving the oven to ensure the metallurgical properties are maintained
- A solution treatment cycle generally lasts one hour at a temperature of 500°C
- Air circulation is provided by 8 heavy duty impellers and air guides, giving a temperature uniformity nominally rated at +3°C
- A typical charge weighs 80kg
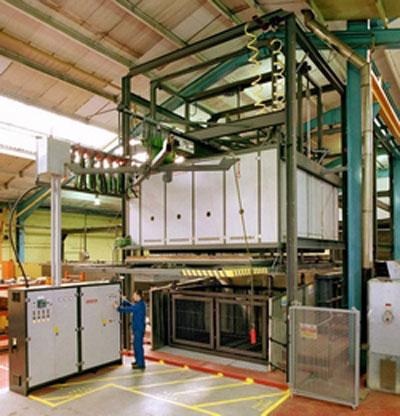
Figure 1. Industrial Drop Bottom Aluminium Solution Treatment Oven
Industrial Solution Treatment and Ageing Ovens
- For processing of aluminium components
- Solution treatment oven
- Top loading chamber
- Temperature range: 50 - 600°C
- Power rating: 96kW
- Ageing oven
- Top loading chamber
- Temperature range: 50 - 200°C
- Power rating: 42kW
- Both units have air circulation
- Chamber dimensions: 1800mm (h) x 1600mm (w)x 1100mm (d)
- Work baskets are lowered into the chamber from above and located in a stainless steel basket guide assembly
- Electrically powered sliding door on the oven top provides access to the heating chamber
- Controls are linked to a remote PC
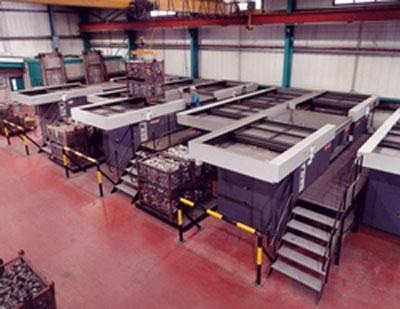
Figure 2. Industrial Solution Treatment and Ageing Ovens
Front Loading Aluminium Treatment Oven With Quench
- Heat treatment oven designed for a leading UK manufacturer of aluminium aerospace components
- Maximum operating temperature 600°C
- Chamber capacity 1400mm (h) x 1400mm (w)x 2000mm (d)
- Temperature uniformity within the chamber is better than the ± 5°C required by BS2M54 and other UK & overseas standards, such as AMS 2750 & MIL-STD-6088
- Quenching at the end of the heating cycle is achieved via a one-piece door which is rapidly lifted by an electric motor, providing good access to the chamber for unloading quenching charges quickly as the end of the heating cycle
- Maximum power rating 54kW
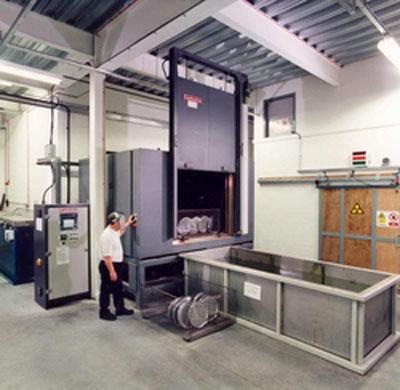
Figure 3. Front Loading Aluminium Treatment Oven with Quench Chamber capacity 1400mm (h) x 1400mm (w)x 2000mm (d)
Smaller Front Loading Aluminium Treatment Oven With Quench
- Designed to provide in-house heat treatment of aluminium alloy fabrications for the aerospace industry
- Chamber capacity : 120mm (h) x 1500mm (w) x 1500mm (d)
- Maximum operating temperature 600°C
- Used for solution heat treatment at 475-530°C, annealing at 360-450°C and precipitation hardening at 120-175°C
- Process times range from 20 minutes for annealing up to 14 hours for hardening
- Heating is provided by incolloy sheathed rod elements positioned behind the side duct sheets and isolated from the working area to prevent heat radiating directly on to any part of the furnace charge
- Temperature uniformity of better than ±3° is achieved via an air ciculation system with heavy-duty fans providing a horizontal airflow through the chamber
- For ease of handling and to ensure the products are held firmly in place, a stainless steel basket is used which fits on tracks in the base of the chamber
- At the end of the cycle, the basked is pulled manually onto a platform immediately in front of the oven, which automatically lowers it into a water quench tank below
- Quenching is performed within the 10 seconds required by the aerospace industry
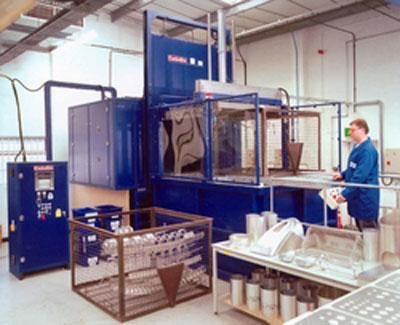
Figure 4. Front Loading Aluminium Treatment Oven with Quench Chamber capacity : 120mm (h) x 1500mm (w) x 1500mm (d)
|