These testing machines from Zwick are predominantly used to perform tensile, compression and flexure tests with complex, dynamic stress sequences.
Special Features
- Extremely rigid, practically resonance-free load frame with manually or hydraulically adjustable crosshead.
- Continuous rated working cylinder with highly accurate guide mechanisms thus ensuring maximum rigidity on all testing levels
- Precision strain gauge load cells for continuous operation at maximum dynamic loading
- LVDT-extensometer (installed centrically in the piston rod) with high resolution, linearity and long service life.
- Freely positionable hydraulic unit
- Low noise level through internal geared wheel feed pump
- Optionally water or air cooling
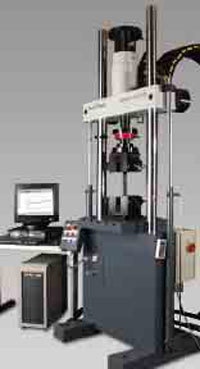
Figure 1. Servo-hydraulic Testing Machine Amsler HB126/80
Technical data
See table servohydraulic testing machines (STM)(Table 1)
Measurement and Control Electronics
The digital measurement and control electronics Amsler HydroWin® 9600 offers connections for external transducers and extensive applications software.
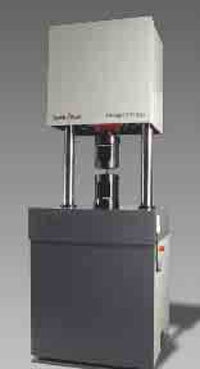
Figure 2. High-frequency Testing Machine Amsler HFP 400
High-frequency Testing Machines (Vibrophores) (With Electro-magnetic Resonance Drive)
Application
Force or strain-controlled tests for determining the oscillation stability in the time and fatigue strength range.
- Fatigue tests according to DIN 50100 (Wöhler curve) in the tensile, compression, pulsating and alternate load range
- Mechanical fracturing tests on CT and COD specimens
- Stimulation of oscillations of the flexure specimens
- Time and fatigue-strength investigations on components such as springs, bolts, crankshafts, connecting rods, steering knuckles etc.
- Production and quality control of components which are exposed to dynamic stressing during their service life.
- Tests under various environmental conditions (temperature, aggressive media).
Special features
- Low energy consumption
- High test frequencies, short test times
- No adjustment of excitation air gap
- High-frequency testing machine
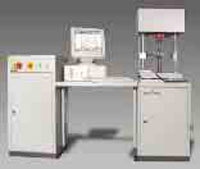
Figure 3. Amsler HFP 5
Technical Data
See table high-frequency testing machines (HFP)(Table 2)
Measurement and Control System
Measurement and control of these testing machines is taken over by the measurement and control electronics VibroWin®. The data selected by the operator as well as the set values and actual values are digitally displayed on the screen.
Rotary Bending Testing Machines
Application
With the rotary bending test, the fatigue strength of round specimens under reversed bending stresses is determined.
Technical Data
See table rotary bending testing machines (UBM) (Table 3)
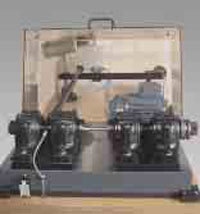
Figure 4. Rotary bending testing machine Amsler UBM 200
Table 1. Servo-hydraulic testing machines (STM) - Standard design1
|
Construction type
|
table top
|
floor stand
|
floor stand.
|
Load frame nominal force – kN
|
5 – 25
|
50 – 1000
|
50 - 500
|
Test stroke – mm
|
100
|
100/250/400
|
100/250
|
Specimen length – mm
|
100 – 700
|
100 – 1100
|
250 - 1500
|
Hydraulic unit
|
|
|
|
System pressure bar
|
210/280
|
210/280
|
210/280
|
Flow l/min
|
4 – 23
|
9 – 600
|
9 - 600
|
Max. power consum. kVA
|
2.2 – 11
|
2.2 – 74
|
2.2 - 74
|
Table 2. High-Frequency testing machines (HFP)
|
Construction type
|
table top
|
floor standing
|
Load frame nominal force kN
|
1 – 5
|
20 - 550
|
Max. force amplitude kN
|
2.5
|
275
|
Max. elast. spec. deform. Mm
|
± 3
|
± 2
|
Frequency range Hz
|
35 – 300
|
35 - 300
|
Frequency levels
|
5
|
16/5
|
Working area width mm
|
350
|
530/600
|
Max. power consum. kVA
|
2
|
5
|
Table 3. Rotary bending testing machines (UBM)
|
Max. bending moment Nm
|
200
|
2000
|
Load reversal frequency min
|
-1 50 – 5000
|
600 – 3000
|
Max. specimen diameter mm
|
25
|
50
|
Max. power consum. kVA
|
1.6
|
5.5
|
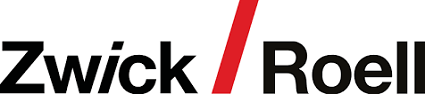
This information has been sourced, reviewed and adapted from materials provided by ZwickRoell GmbH Co. KG
For more information on this source, please visit ZwickRoell GmbH Co. KG.