One of the most common tests, at least in the United States, of the physical characteristics of plastic materials is the notched izod impact test as specified by ASTM D256 Standard Test Method for Determining the Izod Pendulum Impact Resistance of Plastics.
How the Izod Impact Test Works
The Izod impact test fixes one end of a notched specimen in a cantilever position by means of a vice. A striker on the arm of a pendulum or similar energy carrier then strikes the specimen. The energy absorbed by the specimen in the breaking process is known as the breaking energy. The breaking energy can be converted into an indication of a materials impact resistance using such units as foot-pounds or joules.
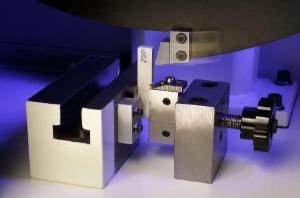
Figure 1. Close up of notched specimen about to undergo an Izod impact test.
Izod Impact Test Data
While use of the data generated from a test for designing a part is not necessarily recommended, it still provides reasonable service as a quality control tool. Most US resin manufacturers have years of izod test data and many customers are accustomed to selecting product based on the data. So, love it or hate it, it appears that the impact test is here to stay.
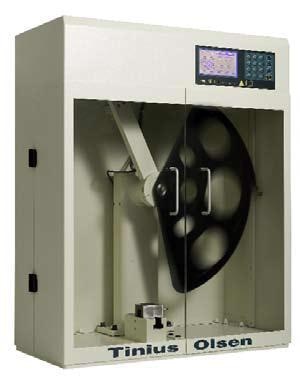
Figure 2. Tinius Olsen's model IT503 enclosed impact tester, capable of performing both Izod and Charpy impact tests on plastic specimens, with up to 25J of available energy with add-on weight sets.
Ensuring Repeatable Izod Impact Testing
Since we’re stuck with it, we might as well look at ways that we can improve the repeatability and reproducibility of the test. The key to getting reproducible results between laboratories, or for that matter, repeatable results between operators in the same lab, is to be sure that both parties are preparing and testing the samples in the same way. Given all the steps that are involved, that can be a tremendous undertaking.
Sample Preparation
ASTM D256 requires that a minimum of five and preferably ten (or more) individual determinations be made to determine the average impact resistance for a particular material sample.
An extra specimen needs to be prepared since notching requires dummy bars be used when notching the specimens, so that means at minimum of 7 specimens of any particular sample need to be prepared for testing. However, since the test method allows inspection of the individual specimen results, and to retest if they are not satisfactory, it is advisable to notch several extra specimens if they are available.
Preparing Materials for Izod Impact Testing by Injection Molding
As with any plastic test, the way a specimen is prepared can influence test results greatly. It is critical that users refer to the ASTM material specification for the material being tested to determine how the specimens are to be prepared. Most specimens are to be prepared by injection molding. The molds can be specifically designed to produce specimens or the specimens may be cut from tensile dogbones or flex bars.
Sources of Potential Error for Injection Molded Specimens
When injection molding specimens, it is important that cooperating laboratories be aware that the type of mold, the molding machine used, the machine set-up and the flow behavior within the mold cavity are all factors that will influence the test data. For example, the impact resistance of a plastic material may be different if the notch is cut perpendicular to, rather than parallel to, the direction of molding. Also, a specimen taken from one end of a molded bar may give different results than a specimen taken from the other end.
Another source of potential error when using injection molded specimens could be the draft angles on the specimens. For years, ASTM D256 has stated that it is essential that the notched surface be machined parallel to its opposite surface within 0.0025 mm (0.001in.)” for injection molded specimens in order to eliminate the high spots on these surfaces caused by the draft angle of the mold. In reality, most testing labs have generally ignored the requirement. This requirement was meant to eliminate any variation in the test results caused by inconsistent specimen placement in the vice which would affect the way the striker hits the specimen when testing, but recently it was observed that it also was causing errors in the measurement of the amount of material remaining under the notch because some technicians measured on the low side, some measured on the high side and others tried to measure somewhere in the middle.
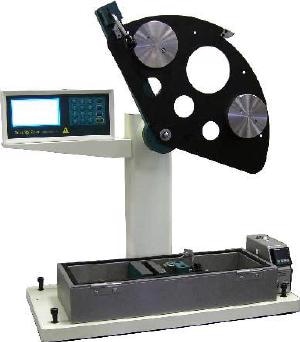
Figure 3. Tinius Olsen's model IT504 impact tester, configured for Izod testing, shown with a cold box to reduce the test temperature (the lid is removed for this picture).
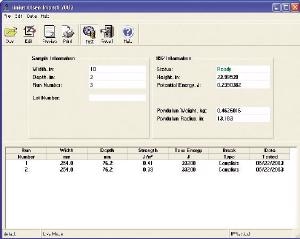
Figure 4. Example of a result screen from Tinius Olsen's Impact Software
Improving Consistency of Izod Test Results
Currently, work is underway in ASTM Subcommittees to revise D256 to eliminate the requirement to machine the specimen and to define the actual point on the specimen where the depth is to be measured.
Preparing Materials for Izod Impact Testing by Compression Molding
Specimens can also be prepared by compression molding a sheet of material to the desired thickness, and then die cutting or machining the specimen from the sheet, or they can be machined from a manufactured part.
However they are prepared, they must be checked to ensure that they are free from scratches, pits, sink marks, and other surface defects. They also should check with a straight edge or on a flat surface to ensure that they are straight. The dimensions of a standard specimen for ASTM D256 are 4 x 12.7 x 3.2 mm (2.5 x 0.5 x 1/8 in.). The most common specimen thickness is 3.2 mm (0.125 inches), but the width can vary between 3.0 and 12.7 mm (0.118 and 0.500 in). The materials specifications should again be consulted to determine the acceptable specimen width for the material being tested.
Notches in Izod Test Specimens
In order to do a notched Izod test, a precise notch is cut into the specimens. The purpose of the notch is to serve as a stress concentrator. The notch is probably the most critical part of specimen preparation and there is tight tolerance defined by ASTM D256 on the depth of the notch (actually the material remaining under the radius of the notch), the angle of cut and the radius at the base (or apex) of the notch. Research has shown that the notch in the specimen is perhaps the greatest source of variability of test data.
Since materials behave differently in response to the notching process, it is important to verify the dimensions of the notch in the specimen as opposed to verifying the cutter dimensions.
Notching Izod Test Specimens
Specimens can be notched using a milling machine, engine lathe or commercially available, specifically designed notching machine. ASTM D256 does not define the specific operation of the notching machine, but most involve adjusting the cutter height on the machine so that it cuts a notch that leaves 10.16 +/- 0.05 mm (0.400 +/- 0.002 in.) of material remaining under the apex of the notch in a single pass and a radius of curvature at the apex of 0.25 +/- 0.05 mm (0.010 +/- 0.002 in.). Single tooth cutters are preferable over multi-tooth cutters. The profile of the cutter can vary but it must produce the notch as specified in the standard.
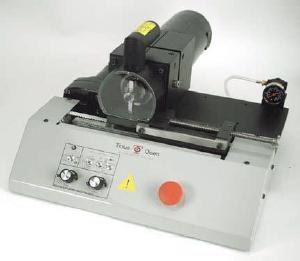
Figure 5. Tinius Olsen's plastics impact specimen notcher.
Commercially available notching machines vary in their features. Some of the more inexpensive ones only have fixed cutter speeds and hand crank feeds. Technically, these do not meet the requirements of the standard since cutter speed and feed speed will vary by material. The standard states “the notching parameters used should not alter the physical state of the material such as by raising the temperature of a thermoplastic above its glass transition temperature” Unfortunately, there is no chart that shows the proper speed for a given material so both cutter speed and feed rate need to be determined by the technician for each individual material type by trial and error. A general rule of thumb is that a high cutter speed combined with a slow feed rate and a lack of some sort of coolant will cause more thermal damage than a slow cutter speed, fast feed rate and the use of coolant. However, if you are buying the material from a supplier who does this test, you can always call the suppliers’ technical department and ask what conditions they are using.
Provision for cooling the specimen when cutting, with either a liquid or a gas coolant, is recommended. Most of the commercially available notching machines provide a way to blow air on the cutting area during the notching process.
Molding Notches and Die Cutters
Molds with designed-in notches and die cutters that cut out a specimen with a notch, while seemingly convenient, rarely meet specifications and should not be used.
Measuring and Inspection of Notches
While the notch depth, the included angle of the notch, and the radius of curvature are critical, only the measurement of the notch depth is relatively simple and can be easily done on specimens prior to testing. The angle of the notch and the radius of the angle at the base of the notch are more difficult to measure. Therefore, specimens must be periodically sampled for inspection under magnification.
A method of identifying the individual specimens within the sample should be devised. Measure and record the width of each individual specimen in the area of the notch using a micrometer or similar instrument. A notch depth verification device, which consists of an analog dial indicator positioned above an anvil, is commonly used to measure the depth of the notch. A digital indicator may also be used and is particularly useful if the actual depth of the notch is to be determined or if it is necessary to switch between measuring in traditional US units and metric units. However, for those laboratories interested in doing a go/no-go type determination, analog dials are very convenient because they can be equipped with follower arms that serve to mark the upper and lower limits of the depth tolerance.
Conditioning Izod Test Specimens
Prior to testing, ASTM D256 requires that notched specimens be a condition for a period of not less than 40 hours after notching in a controlled environment at 23±2°C (73 +/- 3.6°F) and 50 ± 5 % relative humidity. However, some hygroscopic materials are excluded from this requirement. The materials specifications should again be consulted to determine which materials are exempt. In addition, the standard provides relief from the 40-hour requirement when the cooperating parties involved in the testing agree to waive or shorten the conditioning period.
Izod Impact Testing Equipment
Instruments for testing plastics have been manufactured commercially since the 1940s, and there are several manufacturers of testing equipment that meet the requirements of ASTM D256. Over the years, the basic physical characteristics of the test machine have stayed the same, but the means of data acquisition have changed significantly. As a result, many types of equipment, ranging from analog dial & pointers to digital readouts to computer interfaces, are found in various labs throughout the country. However, just because the equipment is old doesn’t mean that it is obsolete. It doesn’t mean it is acceptable for use either since wear and tear take their toll over the years and some machines were manufactured before strict adherence to the specifications in ASTM D256 was deemed to be critical. There is no hope of ever getting accurate results if the equipment isn’t operating according to the specification. Therefore, it is strongly recommended that the impact tester be calibrated and/or verified by an accredited calibration service at some regular interval during its service life.
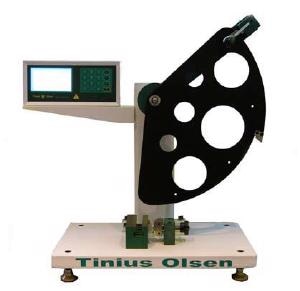
Figure 6. Tinius Olsen's model IT504 impact tester with the release point of the pendulum lowered. In Low Blow fashion, to reduce the amount of available energy.
The testing machine should be located in a temperature and humidity controlled environment. Some means of preventing injury to bystanders due to flying pieces of the specimen should be available. A sheet of cloth, cardboard or similar material may be used and it should be installed in such a manner that prevents the broken ends of the specimens from flying across the room; alternatively, machines like the enclosed model IT503 can be used.
Design of Izod Impact Testing Machines
Impact testing machines are designed and manufactured so that they can be used on a variety of plastic materials. It is impossible for the pendulum to have enough energy to break the toughest of materials while maintaining the resolution or sensitivity to provide accurate results when testing low energy materials. Some manufacturers have interchangeable pendulums while others supply add-on weights for a permanently mounted pendulum. The advantage of using add-on weights is that it is quick and simple and does not involve removing the pendulum from the axle.
Izod Impact Testing Procedure
Once that the correct pendulum energy has been selected, clamp the specimen firmly in the vice. The specimen is clamped so that it is vertically cantilevered with the notch surface facing the direction of impact. The vice should be equipped with an adjustable stop and a notch centering jig which will aid in positioning the specimen in the same position for each determination. The pressure used to clamp the specimens can also be a source of variation in the test results. Too much pressure may damage a specimen while too little will cause the specimen too move in the vice resulting in erroneous readings. A torque wrench should be used to ensure consistent clamping pressure on the specimen.
Latch the pendulum in its upright position. After making sure that the swing plane of the pendulum arm is clear, release the pendulum and allow it to break the specimen.
Pendulum Selection
If the average breaking energy of a sample is known, select the lightest pendulum that will break each specimen in the group without losing more than 85 % of its original energy. The reason for this is to prevent the velocity of the pendulum from falling to an unacceptable level. If the breaking energy of a material is not known, it must be determined by trial and error.
ASTM D256 vs ISO 180
The above procedure is really for ASTM D256. ISO 180 is similar except that it requires a repeat of the test until all specimens have been tested satisfactorily. If there are any outliers, retests are required using extra specimens.
|