QPAC® polyalkylene carbonates copolymers are a unique family of innovative thermoplastics representing a true break-through in polymer technology.
While traditional plastics have been primarily petroleum-based, these materials are derived from carbon dioxide and are produced through the copolymerization of CO2 with one or more epoxides. The resultant polymers are amorphous, clear, readily processible, and have long-term mechanical stability. They are also environmentally friendly by consuming 50% fewer petrochemicals, as compared to other polymers which are 100% petrochemical-based. In addition, they may exhibit biodegradable properties consistent with an environmentally friendly binder.
.jpg)
Image Credits: phidsanu suriyawong/shutterstock.com
QPAC® 25, polyethylene carbonate, and QPAC® 40, polypropylene carbonate, are the two most widely used products within our family of organic binders. However, there is a wide range of QPAC® polymers possible by varying the epoxide monomer or using blends of epoxides to produce a specific reaction. Our technical group has the expertise to effectively work with you to develop the appropriate product for your application.
.jpg)
Thermogravimetric analyses in both air and nitrogen show complete decomposition of polypropylene carbonate at low temperatures, heating rate is 10°C/minute.
Advantages of QPAC Organic Binders
The following is a short list identifying some of the advantages of QPAC®. However, the advantages that our customers see goes well beyond those listed below.
Benign emissions
|
Water and CO2
|
Low temperature / clean burnout
|
Onset at 220°C, complete at 340°C
|
Virtually no residue
|
Less than .10 ppm residue ash and metal
|
All sintering atmospheres
|
Nitrogen, Oxygen, Argon, vacuum (oxygen generated in debind)
|
Controlled debind
|
Polymer chain unzipping means controlled migration of debind emissions through the part. Also results in excellent pore size management.
|
Excellent green strength
|
Tacky, high molecular weight, amorphous thermoplastic polymer allows high-density green shapes, tapes, films, and other structures
|
Typical Applications of QPAC Organic Binders
QPAC® polymers can be processed using typical processing techniques, including solution processing, spin casting, injection molding, or extrusion. This family of copolymers has attractive performance characteristics in a variety of applications. The following table shows some of these applications and QPAC®'s benefits:
Application
|
Benefits
|
End-Use/Industry
|
Electronic ceramic binders
|
|
Electronic/technical ceramics, powder metals, MLCC, Tantalum, Piezo and LTCC capacitors and heaters
|
Technical glass binders
|
|
Display screens, discharge lamps, glass preforms
|
Brazing solutions
|
|
Automotive, HVAC, aircraft
|
Diamond cutting tools
|
|
Construction, cutting tools
|
Energenics
|
|
Propellants, pyrotechnics, airbag inflators
|
Pore formers
|
|
Mesoporous carbon composites, titanium structures, nanomaterials
|
Polymer foaming aids
|
|
Engineering thermoplastics for numerous industries
|
Lost foam casting
|
|
Metal castings, foundries, aluminum, iron
|
Industries Utilizing QPAC Organic Binders
Typical industries that use QPAC organic binders include:
- Electronic Passive Components
- Brazing Pastes
- Technical Glass
- Fuel Cells
- Tooling Manufacturers
- MEMS
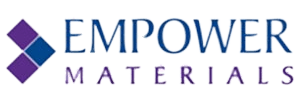
This information has been sourced, reviewed, and adapted from materials provided by Empower Materials.
For more information on this source, please visit Empower Materials.