A multitude of materials are vying to rule the seas. Steel, aluminium and composite materials are competing to be the material of choice, with each making waves depending on the craft under consideration. Two centuries ago, things were much simpler, ships and boats were all made of wood. But today, ships are made of steel, small pleasure boats are usually made of glass fibre reinforced plastic (GRP), and small commercial vessels are made of a variety of materials, for a variety of reasons. ‘Small commercial vessels’ covers everything from fast ferries, and patrol craft to pilot boats and workboats. These vessels are the main battleground for the marine materials. Economies of Scale The material that is considered first for building small, slow commercial vessels is still steel because it is the cheapest. However, GRPs become competitive if a shipbuilder knows that it is making more than ten identical craft or hulls. The cost of producing a plug and mould can be spread over a number of hulls, and so many small commercial vessels that are built using the same hull design, such as pilot boats, are made from GRPs. Orders for ten or more craft are much less likely as the size of the craft increases, which is why there are few GRP craft more than 20m in size. Materials Selection There are two main drivers for using materials other than steel, the desire for speed, and customer preference or prejudice. All vessels have a maximum ‘displacement speed’, which is related to their length. When travelling at this speed, the craft is pushing aside water and travelling in the trough behind its bow wave. To go any faster than this displacement speed, craft must be light enough and have the power to ‘mount’ the wave and ‘plane’ across the water. So to achieve more than the displacement speed requires a light construction. It is almost impossible to design a 10m craft in steel that can plane, it is difficult even to build a 20m craft that can do so, and at 40m there is still a significant loss of speed associated with the weight of the steel. GRPs, fibre reinforced composites (FRCS) and aluminium are all alternatives. Timber is also still used but only in a few instances. Customer preference or prejudice is also an important driver. Every boat owner has definite views, usually associated with previous bad experiences or preconceived images. FBM Marine hears all the reasons under the sun as to why prospective customers specify a particular material, even if it is not the optimum material for the vessel being ordered. Changing owners minds in these circumstances is difficult but is possible if a good case is made, using strong technical or life-cycle costing arguments. Below are some of the arguments for and against the use of various materials in the marine environment. Welded Aluminium Hulls Welded aluminium hulls are becoming increasing popular because the material has a number of advantages, as well as being lightweight. There used to be a great deal of prejudice against using aluminium in a marine environment, but today the tonnage of aluminium being produced specifically for boats and fast ferries (up to 120m in length) is growing rapidly. The alloy used is usually 5083 (plate) or 6082 (extrusion), and 6061 in the US. Advantages and Disadvantages However, the marine environment is particularly harsh for any material, and aluminium has two Achilles’ heels, low fatigue strength and low position in the galvanic scale, figure 1. On the other hand it does not rust or suffer osmosis, and paint coatings last longer than on steel. Aluminium internal areas need no protective painting, and many craft are left unpainted externally above water. The surface goes gritty but the degree of corrosion is small. 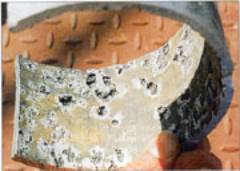 | Figure 1. Deep Pitting corrosion in an aluminium alloy after only a year in service in a marine application. | Aluminium’s low fatigue strength has caused problems in numerous vessels, from patrol craft and fast ferries to the superstructures of large liners. The problems arise because, whereas in dry air aluminium alloys exhibit the same ratio of fatigue strength to yield strength as most metals, in welded structures and when immersed in sea water the fatigue strength is reduced. This means that designers must limit stresses to as low as 30-40 MNm-2. As a result of this reduced fatigue strength, the bottom aft structures of waterjet-powered fast ferries have suffered from extensive fatigue cracking. Similarly, the waterjet inlet tunnels, figure 2, are subject to intense vibration as they are very close to a multi-bladed impeller that sends pressure pulses through the water. On top of this, the impeller is usually made of stainless steel and galvanic effects can wreak havoc, even when the impeller is stationary. 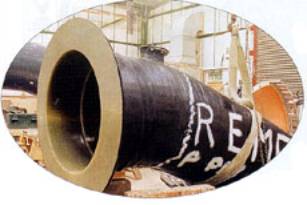 | Figure 2. A fibre reinforced composite waterjet tunnel that overcomes problems such as fatigue cracking, galvanic corrosion and erosion associated with aluminium tunnels. | Passenger Safety Nevertheless, aluminium is the predominant material for fast ferries because the only other materials giving the necessary performance are GRP or FRC. Safety for passengers is the key problem with plastics. A GRP structure can contain a fire, but the resulting smoke and toxic fumes can also be killers. Fast ferries are now subject to a recently introduced International Maritime Organisation Code of Safety. A previous code only allowed non-combustible materials to be used (aluminium is included in this definition), but the new code defines the criteria for a so called ‘fire restricting material’. These include limits for smoke, toxicity and heat release under the ISO Room Corner Test. Not many normal plastics pass this standard. Phenolics do, but they have serious drawbacks for producing large structures in the marine industry the need to post cure at elevated temperatures, the health hazards during production and their lower mechanical properties. There are one or two new products that pass the standard but their applicability extends mainly to internal outfitting, such as linings and ceilings. This does mean, though, that the passenger saloon can be made to look more attractive more in the style of an aircraft. Aluminium Honeycomb Structures Aluminium honeycomb, consisting of aluminium skins covered with a thin decorative plastic laminate, is also widely used. This `composite' is used in various thicknesses for minor bulkheads and linings. Baggage lockers and ceilings can be moulded with phenolic skin and aluminium honeycomb to look the same as aircraft. The aluminium core of the material is classed as non-combustible and therefore does not have to pass the ISO test. The Future for Plastics Very few fast ferries have been built completely from plastics to the new code. Realistically, a structural reinforced plastic that is suitable for boat construction and meets the new code is unlikely to come on to the market at present. So the solution is to design a vessel so as to prevent a fire reaching the plastic structure by covering all internal surfaces with fire-proof materials, eg Rockwool. This does not push up costs greatly, because all the surfaces of the passenger accommodation, car decks and wheelhouse have to be thermally insulated anyway, and Rockwool can be used for both jobs. But high tooling costs are a problem for plastic craft bigger than 20m, so aluminium is unlikely to be supplanted for several years. Aluminium Extrusions Aluminium is also widely used in the form of large extrusions for major structural applications. Whole decks are constructed from extruded planks with integral T stiffeners. FBM Marine also use box section extrusions for creating a `raft' to which the two hulls of a catamaran are welded, figure 3. Quick to produce, the extrusions need no internal inspection in service, and the ‘honeycomb’ produced gives the catamaran substantial built-in buoyancy. The largest extrusions used are 300mm deep and 12m long. These are laid alongside each other and automatically welded together to create a deck section 12m by 4m. These welded extrusions are the only part of the structure holding the two hulls together. 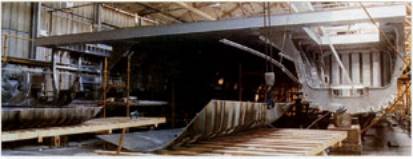 | Figure 3. The long horizontal extrusion is one segment of a nest of extrusions welded together to form the deck of a passenger catamaran. | Hybrid Structures An emerging trend in marine structures is that combinations of different materials are increasingly being used. The word ‘hybrid’ is used to describe these combinations, rather than the old word ‘composite’, which today implies a combination of plastic and a reinforcement. (Not so long ago, the word ‘composite’ meant a steel-framed ship with wooden planking.) Hybrid structures are mainly made from aluminium, with GRP or FRC being used in areas where it is more appropriate. For example, FBM Marine is tackling the problem of aluminium jet tunnels by making them instead from solid GRP mouldings and bolting them to the main aluminium structure using stainless steel bolts and adhesive sealant. Geometric Considerations The problem of rapid double curvature can also be solved using moulded GRP. FBM Marine recently built two small waterplane area twin hull (SWATH) vessels for the Ministry of Defence, which have torpedo-shaped hulls, figure 4. The cylindrical part of the torpedo shape is easy to make in aluminium, but the nose cone is very difficult. So instead, these were moulded in GRP and flange bolted to the aluminium cylinder to create a hybrid hull. The cones were filled with foamed-in buoyancy in order to achieve the damage stability required. Foam filling an all aluminium structure would not have been allowed by the classification authorities, because access to the internal structure for regular inspection would not be possible. 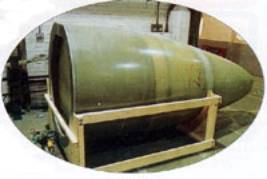 | Figure4. A fibre reinforced composite nose cone of a small waterplane area twin hull (SWATH) | Foam Sandwich Panels Foam sandwich panels of FRC can replace aluminium in other areas. Those parts of a vessel that are clear of the passenger saloons or car decks are not subject to the stringent fire regulations of these areas, and so large panels of FRC in sandwich form can be used. These offer advantages over aluminium. Aluminium structure in welded form suffers from weld distortion and shrinkage to a greater extent than steel. Hulls usually come out several inches shorter than designed, but the real problem is one of aesthetics. Buckled panels are unsightly. One customer demanded that FBM Marine create a smooth surface over an entire superstructure area. The solution was to build an aluminium ‘box’ that formed the structural and fire integrity of the saloon and then to clad it with FRC panels. These panels were lightweight foam sandwich panels with very thin skins of stitched cloth and polyester resin. The resulting superstructure finish was yacht-like. Structural Adhesives in Hulls Another way of reducing the unsightly effects of distortion is to join aluminium panels together using structural adhesives. In fast ferry design, the problem with adhesives is their poor resistance to collapse in a fire. The solution is to combine rivetting with the adhesives. Panels are very large and in many cases need assembling vertically, so rivets are required in any case just to hold the surfaces together while the glue dries. However, rivet spacing can be much greater than in a rivet-only joining process. Applications of Composite Materials Another positive trend for composite materials is the increasing replacement of steel shafting with composite shafts. Carbon fibre composites are the best materials for this application. Shaft diameter is greater using composites, but the weight is a fraction of steel shafts. Other parts that are being made from moulded reinforced plastics rather than metal include double-skin doors, shower trays, Bimini sun shields for tropical waters, navigation light boxes, wheelhouse consoles and chain cable lockers. Summary However, the marine construction world is very conservative. Sandwich bottoms for boats are still frowned upon, as there have been too many disasters in this area. In fact, sandwich decks and superstructure roofs still give delamination and blistering problems, especially under tropical skies. Part of the problem lies in lack of quality control during construction, but sun, sea and salt water combine to create a very harsh environment for any material. Clearly, for a material to be successful in marine applications it must prove itself equal not only to competing materials, but to the challenges posed by nature. |