The Chemical Formula of Boron Carbide is B4C and is the third hardest material known to man. The first and second being diamond and cubic boron nitride respectively. Boron Carbide powder is produced when Carbon reacts with Boron Trioxide (B2O3).
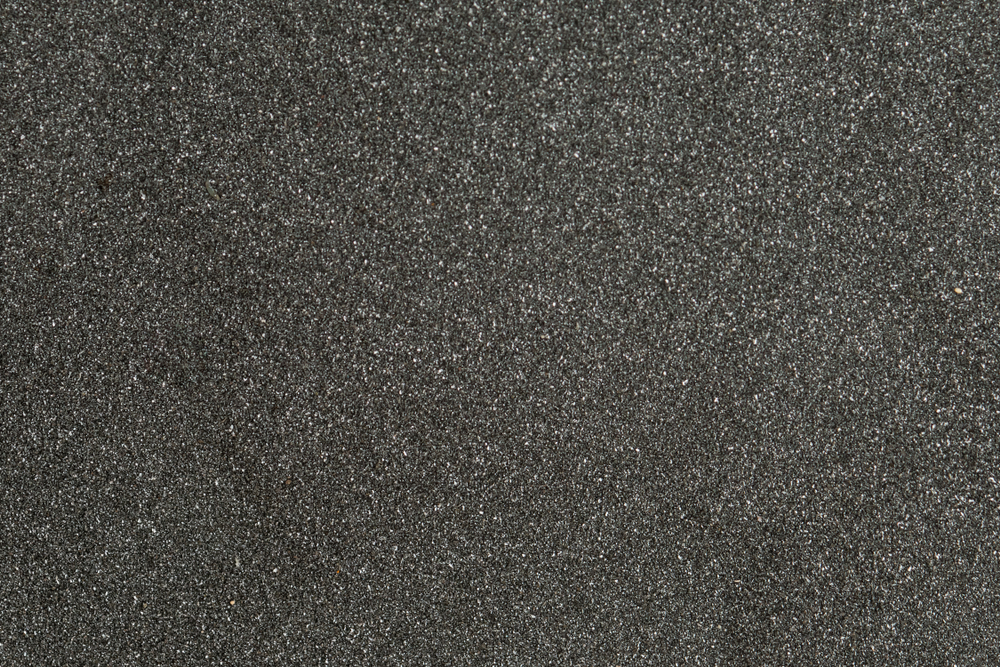
Image Credit: Shutterstock/AkulininaOlga
Machining Boron Carbide
In all of these applications where a high precision engineering component is required, it is important to recognise the difficulties of machining Boron Carbide. Despite the high hardness values it displays, it is nevertheless a relatively brittle material and can only be machined using diamond grinding techniques.
Consequently, it is beneficial that a skilled and experienced operator conducts the machining operations as incorrect procedures can generate sub-surface damage and micro-cracks that may lead to premature failure once the component is subjected to operating stresses in service.
Types of Boron Carbide
Henri Moissan, by reacting and fusing Boric Oxide and Carbon first synthesized Boron Carbide in 1899 in an electric arc furnace. The molten material becomes very carbon rich and it is composed of boron carbide and graphite as it solidifies. In commercial use, Boron Carbide powders are milled and purified to remove any residual metallic impurities.
It is difficult to sinter pure Boron Carbide to high densities and the sintering process requires the use of sintering aids. To achieve a density of greater than 95% of theoretical density, hot pressing or sinter HIPing is required, but even using these processes small quantities of dopants like fine carbon or silicon carbide are required to achieve full densification.
Key Properties of Boron Carbide
The physical and chemical properties of Boron Carbide make it ideal for a number of industrial uses. These include;
- High Hardness
- High Melting point
- High Young’s Modulus (it’s a very stiff material)
- Relatively low thermal expansion and conductivity
However, one of the drawbacks of Boron Carbide is that it begins to oxidise at temperature above 500°C unlike Silicon Carbide where the formation of an oxide layer of Silicon dioxide, retards high temperature oxidation. In addition, due to the relatively low thermal conductivity of Boron Carbide it displays poor thermal shock resistance.
As it is often considered for application alongside Silicon Carbide it is useful to contrast the typical properties of Boron Carbide with Silicon Carbide in the hot-pressed pore-free condition as shown in the table below;
Table 1. Property comparison of boron carbide and silicon carbide.
Property |
Unit |
SiC |
B4C |
Density |
g/cm3 |
3.21 |
2.51 |
Melting Point |
° C |
2,760 |
2,450 |
Hardness |
Vickers |
2,600 |
3,000 |
Compressive Strength |
MPa |
2,200 |
2,800 |
Young’s Modulus |
GPa |
410 |
450 |
Fracture Toughness |
K IC MPam 1/2 |
3.2 |
3.0 |
Electrical Resistivity |
ohm.m |
10 3-104 |
10-103 |
Thermal Expansion Coefficient |
10 -6 K -1 |
4.0 |
4.6 |
Thermal Conductivity |
Wm-1K-1 |
110 |
35 |
Thermal Shock Resistance |
- |
Good |
Poor |
Temperature of Application (in Air) |
° C Max |
1,600 |
500 |
Source: Product Development with SiC and B4C Ceramics, P Feinle, H Knoch, 3 rd European Symposium on Engineering Ceramics, Ed. FL Riley, Elsevier, 1991
Major Applications of Boron Carbide
The key properties of Boron Carbide, which are of interest to the designer or engineer, are hardness and the related abrasive wear resistance.
A typical example of the optimum use of these properties is in the field of abrasive blasting and water jet cutting, where Boron Carbide nozzles are used to withstand the harsh wear regime generated by blasting media such as alumina or silicon carbide grits and slurries. Several tests have shown that under similar blasting conditions a Boron Carbide nozzle will outlast a typical hard metal, Tungsten Carbide nozzle by a factor of 100.
These qualities also lead to Boron Carbide being used in high precision tooling dies and similar engineering components.
Boron Carbide is also found in personal and vehicle anti ballistic armor plating where the combination of low density and a high Young’s modulus are attractive qualities, providing high specific stopping power to defeat high velocity projectiles.
In the nuclear field, the ability of Boron Carbide to absorb neutrons makes it popular as a material for absorbing neutron radiation in nuclear power plants. Boron Carbide is used to shield, as a control rod in the nuclear reactor and as shut down pellets in a nuclear power plant.
Precision Fabrication By Design
.jpg)
This information has been sourced, reviewed and adapted from materials provided by INSACO Inc.
For more information on this source, please visit INSACO Inc.