Glasses display both the properties of supercooled liquids and crystalline materials but with properties that are different to both.
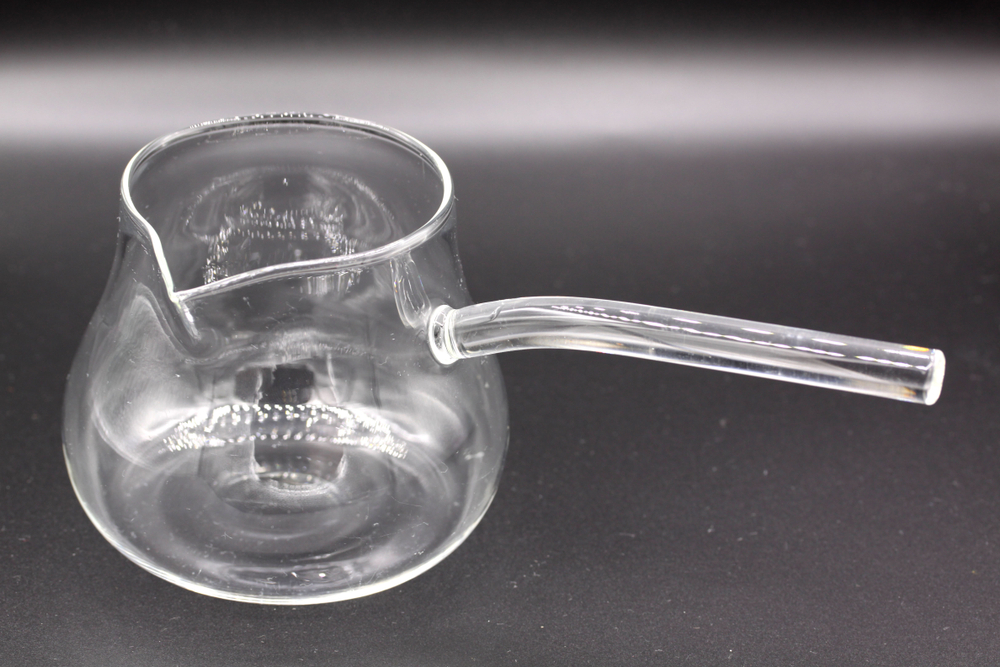
Image Credit: Shutterstock/Shafostock
They are typically formed from a “former” such as silica sand, a “fluxing agent” such as Potash or Lithium Carbonate which aids in reducing the melting temperature of the Former and “stabilizers” such as Alumina or Zinc Oxide which aid in the production of a uniform structure.
Some common glass families are as follows;
- Soda-lime glass is one of the most common and least expensive forms of glass. A typical composition is 60-75% silica, 12-18% soda, 5-12% lime.
- Borosilicate glass is defined as a silicate glass with at least 5% of boric oxide in its composition. The major properties of Borosilicate Glass are its high resistance to temperature change and chemical corrosion. Laboratory ware and headlights are examples of the use of Borosilicate Glass.
- Aluminosilicate glass utilizes aluminium oxide in its composition. It is similar to borosilicate glass but it has greater chemical durability and can withstand higher operating temperatures.
- Glass-Ceramic materials are formed initially as glasses but then are converted into a largely crystalline form similar to a ceramic material, or are composed of a glassy matrix with ceramic elements within the matrix. To be classed as a Glass Ceramic, at least 50% of the structure must be crystalline.
In this article we describe three of these types of glass ceramic materials which are often employed as precision machined, engineering or optical components.
ULE® or Ultra Low Expansion Glass Produced by Corning
ULE® or Ultra Low Expansion glass is a titania-silicate glass, manufactured by flame hydrolysis which has a very low coefficient of thermal expansion – typically 0 ± 30 x 10-9/°K for temperatures between 5-35°C. It is supplied by Corning in large blocks or boules which then have to be machined to final dimensions.
The thermal expansion behavior from -100°C to + 100°C is presented graphically as shown in Figure 1 below.
.jpg)
Figure 1. Thermal Expansion behavior for ULE® (Source: Corning Data Sheet)
ULE® exhibits excellent resistance to weathering, no electrical surface leakage when subject to aqueous species and a high resistance to chemical attack.
Typical Properties for ULE® are presented in Table 1 below.
Table 1. Mechanical and Physical Properties for ULE®. (All properties are at room temperature unless otherwise noted. Engineering data are representative, and are not intended as absolute nor warrantable. Manufacturer's Data shown is blended from multiple sources and therefore illustrates the marketplace.)
Property* |
Value |
Mechanical |
Density |
2.2 gm/cc |
Hardness |
49 Knoop |
Modulus of Elasticity |
9.8 x 106 psi |
Poisson's Ratio |
0.17 |
Electrical |
Volume Resistivity |
1x1011.6 ohm-cm |
Thermal |
Coefficient of Thermal Expansion |
0.00 +/- 0.03 x 10-6/°C |
Thermal Conductivity |
1.31 W/mK |
Specific Heat |
0.18 cal/g °C |
Maximum Working Temperature |
800 °C |
Optical |
Index of Refraction |
1.48 |
Given the excellent thermal stability of this material it is not surprising that it finds applications as machine tool reference blocks and mirrors for telescopes and satellites.
Zerodur®
Zerodur® is a glass ceramic manufactured by Schott using a process known as controlled volume crystallization. The structure contains 7-78% of high quartz micro-crystallites 30-50 nm in size.
This leads to the production of a highly uniform, isotropic and homogenous material even in large blocks.
The thermal expansion of this glass ceramic material is even lower than ULE®, recording a value of 0 ± 0.10 x 10-6/K. Other mechanical and Physical Properties are summarized in Table 2 below.
Table 2. Mechanical and Physical Properties for Zerodur. (All properties are at room temperature unless otherwise noted. Engineering data are representative, and are not intended as absolute nor warrantable. Manufacturer's Data shown is blended from multiple sources and therefore illustrates the marketplace.)
Property* |
Value |
Mechanical |
Density |
2.53 gm/cc |
Hardness |
620 Knoop |
Modulus of Elasticity |
13 x 106 psi |
Poisson's Ratio |
0.243 |
Electrical |
Dielectric Constant |
7.4 (@ 1 MHz) |
Volume Resistivity |
2x1013 ohm-cm |
Thermal |
Coefficient of Thermal Expansion |
0.00 +/- 0.1 x 10-6/°C |
Thermal Conductivity |
1.43 W/mK |
Specific Heat |
0.80 cal/g °C |
Maximum Working Temperature |
600 °C |
Optical |
Index of Refraction |
1.54 |
Transmission Band |
0.3 - 2.5 Wavelength (microns) |
Typical applications of Zerodur include:
- Precision Optics
- Mirror Substrates for Large Astronomical and X-Ray Telescopes
- Ring Laser Gyroscopes
- Standards for Precision Measurement Technology
- Lightweight Honeycomb Mirror Supporters
- Stages and mirrors for Lithography Equipment
Macor®
MACOR® Machinable Glass Ceramic is a white, odorless, porcelain-like (in appearance) material composed of approximately 55% fluorophlogopite mica and 45% borosilicate glass. The key benefit provided Macor® is that the structure of the material although a glass ceramic iscomposed of interlocking plate like mica crystals in a glassy matrix (see Figure 2 below) which, unlike other glass ceramics can be machined by using conventional metal working tools. The material produced during the machining process is a fine powder of glass and crystals.
.jpg)
Figure 2. Macor Microstructure (Source: Corning Data Sheet)
The key properties of Macor® are that it has a continuous use temperature of 800°C and a peak temperature of 1000°C. Its coefficient of thermal expansion readily matches most metals and sealing glasses.
It is also non-wetting, exhibits zero porosity, and unlike ductile materials, won’t deform. It is an excellent insulator at high voltages, various frequencies, and high temperatures. When properly baked out, it won’t outgas in vacuum environments.
More detailed property data is contained in Table 3 below.
Table 3. Mechanical and Physical Properties for Macor®. (All properties are at room temperature unless otherwise noted. Engineering data are representative, and are not intended as absolute nor warrantable. Manufacturer's Data shown is blended from multiple sources and therefore illustrates the marketplace.)
Property* |
Value |
Mechanical |
Density |
2.52 gm/cc |
Hardness |
250 Knoop |
Modulus of Elasticity |
9.7 x 106 psi |
Flexural Strength |
15 kpsi |
Compressive Strength |
50 kpsi |
Fracture Toughness |
1.53 MPa m1/2 |
Electrical |
Dielectric Strength |
785 ac V/mil |
Dielectric Constant |
6.03 (@ 1 MHz) |
Volume Resistivity |
> 1014 ohm-cm |
Thermal |
Coefficient of Thermal Expansion |
9.4 x 10-6/°C |
Thermal Conductivity |
1.46 W/mK |
Specific Heat |
0.19 cal/g °C |
Maximum Working Temperature |
1000 °C |
Typical applications for Macor include;
- Spacers, reflectors and cavities in laser assemblies
- High vacuum industry
- Thermal breaks, coil supports and vacuum feed throughs
- Aerospace/space industry
- Space Shuttle door and window retaining rings, satellite electrical supports
- Nuclear industry
- Fixtures and reference blocks in power generation units
Machining of Technical Glasses and Glass Ceramics
As is often the case when faced with a difficult manufacturing challenge, it is always best to talk to someone with experience in order success as quickly as possible.
.jpg)
This information has been sourced, reviewed and adapted from materials provided by INSACO Inc.
For more information on this source, please visit INSACO Inc.