Extensometry is the science of the measurement and analysis of changes in a materials linear dimensions during tensile testing.
An extensometer is an instrument that measures test specimen elongation to characterize strain. The range of applications where extensometers are used is diverse and the technical requirements for these devices are multifaceted. There is no single device that meets all needs for all applications.
The requirements for an extensometer are determined by the characteristics of the material to be tested including shape and dimensions, test requirements, and the test standards that must be followed.
It is also necessary to decide whether an extensometer can be connected directly to the specimen. Very thin specimens such as foils can be sensitive to clamping forces, while small diameter wire specimens, for example, lack sufficient visible area for reliable noncontact measurements.
A high stiffness in the initial extension range, followed by high plasticity requires more than one extensometer. The first measures small strains (typically up to 5 mm) very accurately in the elastic range, and the second measures very high extensions (typically 500 mm). Materials with very smooth surfaces, or those made of transparent materials are not suitable for noncontact measurements without first fixing measuring marks onto the surface of the specimen.
To qualify the integrity of a measured signal, standards use quantitative terms such as resolution, deviation, and uncertainty. Requirements for the accuracy of extension measurements are normally given in application-specific test requirements and international standards.
Devices that are easy to set up and sequences that can be automated reduce personnel time and effort. Simplified set up routines can improve the quality of the test results by minimizing subjective influences.
Contact-type Measurement Extensometers
Clip-on extensometers are, as the name implies, mounted directly onto the specimen. The mechanical parts that transfer extension, via knife edges, from the specimen to the internal transducer are short and stiff. There is practically no relative movement between the specimen and the extensometer, resulting in a high level of measurement accuracy.
A Zwick Roell Clip-on Extensometer - Measuring Strain on a Metal Specimen.
The range of a clip-on extensometer is limited to a few millimeters, and it applies a load directly to the specimen. Extensometers with counter-balance weight and double-sided measuring systems are used to compensate for superimposed bending stresses. To minimize setting errors, some clip-on extensometers are equipped with motorized application and removal systems.
Sensor arm extensometers offer the advantages of automatic operation and a large measurement range with high measurement accuracy. Precision designs with a very smooth and balanced mechanical operation apply minimum loading to the specimen (as little as the measurement marks used for noncontact extensometers). Because the sensor arms are in contact with both sides of the specimen, superimposed bending strains are largely compensated.
Because of the direct contact with the specimen, sensor arm extensometers can be damaged or even destroyed at the failure point of high elasticity/high extension specimens. An example from the automotive industry is the testing of safety belts. At the point of failure, the material will exhibit backlash or whiplash characteristics that could damage the testing equipment.
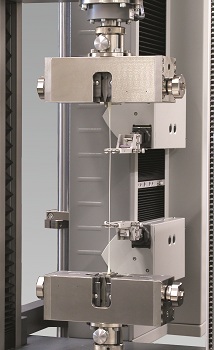
Zwick’s multiXtens extensometer combining fully automatic sensor arm extensometers with a dual averaging axial and transverse strain extensometer.
Non-contact Video Extensometers
A primary advantage of noncontact video extensometers is that they may be used up to the material breaking point without damage, even when testing specimens that exhibit whiplash. Another advantage is the capability to more accurately determine strain and use strain as a control loop mechanism for test samples undergoing large deformations. An example of this may be found in characterization of biomaterials and medical-grade polymers, where video extensometry supports measurement of large strains. Additional applications include testing of medical components in solution, where attachment of a traditional extensometer would not be practical.
Noncontact video extensometers require measurement marks to be attached to the specimen, which are optically distinct from the surrounding area of the specimen. The measurement marks are clipped, tacked, or glued onto the specimen, or the specimen is marked with a colored pen. The application of the measurement marks adds a step to the test cycle, potentially reducing throughput, increasing the cost of testing, and introducing inaccuracies through human error.
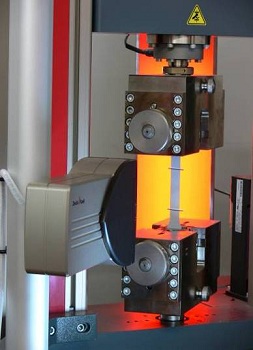
Zwick’s videoXtens noncontact extensometer with the unique flexible illumination system
The position of the measurement marks on the specimen is evaluated by software algorithms which determine a certain area around an optical center point. This becomes the gage length, and as a load is applied to the specimen, the movement of the marks is converted to extension values. Special lighting for surface or background illumination of the specimen optimizes the contrast to the measurement mark. During deformation, the ambient lighting changes on the measurement marks as well as on the specimen, and surrounding influences (such as reflections) can influence the optical center point. This is often the cause of scatter in the test results.
Non-contact Laser Extensometers (Laser Interferometry)
The latest in extensometer technology uses a noncontacting device that does not require measurement marks. The laser extensometer uses the unique structure of a specimens surface as a fingerprint to generate a virtual measurement mark. Laser light directed on these measurement positions is reflected in various directions corresponding to the surface structure and creates a specific pattern of speckles. Selected measurement points are constantly followed and converted to direct extension values. The change in the surface structure, which is the basis of the speckle pattern, is continuously evaluated during specimen deformation.
This laser interferometer-based method of noncontact extensometry allows test labs to characterize materials, components, and even subassemblies making it well-suited for quality control and R&D applications. Additionally, this novel approach to extensometry supports tests on microspecimens with small gage lengths that require exceptional accuracy in strain measurement.
Such tests would not be possible using traditional extensometry. Speeding up throughput and delivering the utmost accuracy in strain measurement, laser interferometer noncontact extensometers offer significant value for high volume test labs.
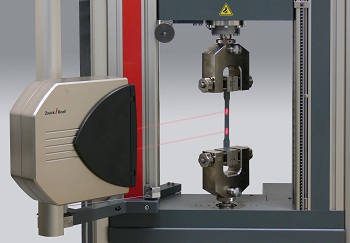
Zwick’s laserXtens noncontact extensometer operating without specimen marks.
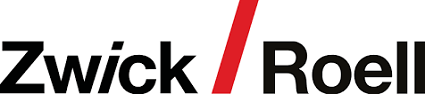
This information has been sourced, reviewed and adapted from materials provided by ZwickRoell GmbH Co. KG.
For more information on this source, please visit ZwickRoell GmbH Co. KG.