Compounding companies are continually seeking competitive advantage, as well as opportunities for cost reduction. One method of gaining competitive advantage is to offer superior quality. Maintaining a high degree of batch-to-batch quality enables compounders to effectively differentiate their products and translates into demand for tests that support more stringent quality standards.
Testing of Thermoplastic Materials
In addition, the application space for thermoplastics is expanding – resulting in new performance requirements that must be verified through testing. Testing under non-ambient conditions enables compounders to demonstrate performance across a range of values that map to customer applications.
Specific examples of tests that are increasingly utilized include Vicat Softening Temperature and Heat Deflection Temperature. Compounders are also seeking ways to increase throughput in testing and automation solutions help support this requirement.
Vicat Softening Temperature
As thermoplastics do not have a definite melting point that precisely marks the transition from solid to fluid, analysis of the slow softening they undergo as temperature increases is an important element to determining quality and performance. Vicat Softening Temperature describes the temperature at which a 1 mm 2 circular indenter (or cylindrical punch) is able to penetrate 1 mm into the sample at applied loads of 10 N and 50 N. The standards for Vicat Softening Temperature are ISO 306 and ASTM D 1525.
Heat Deflection Temperature
The Heat Deflection Temperature (HDT) test involves flexural loading of a standard test bar as the temperature is ramped at a specified rate. HDT thus defines the temperature at which the standard test bar deflects a specified distance under a load. It is most often utilized to determine short-term heat resistance and distinguishes between materials that may sustain light loads at high temperatures versus those that lose their rigidity over a narrow temperature range. The standards for HDT are ISO 75 and ASTM D 648.
Specialized Equipment Eases Testing
A complete range of testing solutions for compounders is available from Zwick/Roell, based in Ulm, Germany. Among the newest products introduced by Zwick for plastics testing are the Aflow and Mflow extrusion plastometers.
The Aflow Extrusion Plastometer
The Aflow extrusion plastometer supports determination of melt mass flow rate (MFR) and melt volume flow rate (MVR). The Aflow has been designed for high throughput environments. Melt index determinations may be made faster and more reliably with this system, through automation features. Features include force-control which automatically controls stepless adjustment of test loads up to 50 kg and automatic parameter control, which automatically sets the relevant parameters.
.jpg)
Figure 1. Zwick’s Aflow extrusion plastometer for high throughput environments.
Automatic parameter control is particularly useful for polymers with an unknown MFR, where operator influence in the determination of parameters could lead to reductions in measurement accuracy.
Push-button pre-compacting and cleaning conserve operator time while automatic parameter control enables auto programming of the test procedure for all flow rates. The overall benefits of the Aflow extrusion plastometer include a reduction in active operator engagement during the test procedure and increased accuracy in results.
The Mflow Extrusion Plastometer
Zwick’s Mflow extrusion plastometer incorporates program-controlled weight positioning and removal – streamlining the testing process by eliminating the need for an operator to manually position the weights required for testing of each polymer. Similar to the Aflow system, the Mflow incorporates automatic parameter control, an element of design that supports the highest levels of measurement integrity.
.jpg)
Figure 2. Zwick’s Mflow extrusion plastometer with modular design elements to facilitate upgrades and retrofits.
Compounders managing a mid-range level of throughput turn to the Mflow extrusion plastometer for the flexibility it delivers. This flexibility is driven by a modular design that allows for upgrades and retrofits in accordance with changing departmental needs.
Unique Solutions for Reinforced Plastic Composites
Relatively high tensile strengths and sensitive flexural behavior are typical properties of reinforced plastic composites. As mechanical behavior and properties for these materials differs greatly from unfilled plastics, the tests that are utilized to assess their performance in applications vary greatly as well.
There are two essential requirements for tensile tests on plastic composite compounds. These tests include specimen loading over a large area, achieved by the use of load transmission elements in the form of bonded tabs, and a tensile load aligned exactly axially.
Specimen grips operating on a wedge or wedge-screw principle are normally used. The exact alignment can in simple cases be checked by using a specimen with three strain gages applied and comparing the specimen strain measured. For more advanced testing, for example in the context of a Nadcap certification, special aids are used to enable angular and axial errors in any direction to be detected.
Materials Testing Machines Designed for Different Test Procedures
The many different types of tests require frequent equipment changes on the materials testing machine. To minimize the amount of work involved, testing machines are provided with two test areas. In the upper test area, for example, are the tensile grips with which the tensile tests, in-plane shear (IPS) and open-hole tensile tests can be performed without laborious equipment changes. The lower test area is then available for an additional fixture, such as a compression test kit.
.jpg)
Figure 3. A materials testing machine with two test areas can be used for various tests on reinforced plastic composites without equipment change.
Additional fixtures for three and four-point flexure tests, interlaminary shear strength (ILS) or the Iosipescu V-notch shear test are conveniently attached via slide-in inserts used in the tensile grips in place of jaws. This enables very fast equipment changes and has the added advantage that the pre-set axial alignment of the specimen grips to each other is not lost during the changeover.
Compression Testing
Compression tests represent a particular challenge. Compression tests allow the properties of the whole composite to be measured in addition to fiber strength. The challenge lies in inducing compression deformation up to failure of the material, if possible, without buckling. This means avoiding bending in a flat, planar specimen.
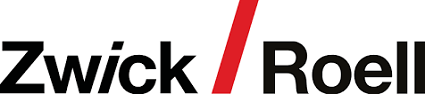
This information has been sourced, reviewed and adapted from materials provided by ZwickRoell GmbH Co. KG.
For more information on this source, please visit ZwickRoell GmbH Co. KG