There is no doubt that the developments in materials science over the past 20 years have opened up vast, opportunities for industry. The introduction of novel materials has allowed industry to enhance products, optimise process performance, and in many cases implement better safety and environmental management procedures. One of the greatest advances has been made in the field of fibre reinforced composite materials, which consist of fibres embedded in a thermosetting or thermoplastic matrix. Composite materials are now widely used in the space and aerospace sectors where their low density, coupled with durability, stiffness and strength, makes them an attractive weight saving option. These same properties make composites potentially beneficial to other industries, particularly the automotive sector. However, much more information on composite properties and performance in a number of areas is required before they gain full acceptance amongst engineers and designers. Impact Performance Modelling Obviously, with safety a major priority in the automotive sector it is vital that manufacturers have accurate information on how all the materials going into their vehicles will perform under crash conditions. One barrier to the greater exploitation of composites in the automotive industry is the amount of R&D money potentially required. The LINK programme in the UK was developed to validate computer impact performance models. Such models could potentially replace some aspects of time consuming, real life testing, thus bringing faster product design and testing procedures, and helping manufacturers to get the most from their R&D spend. Fibre Reinforced Composites The variety of possible geometries and basic materials ensures that composites offer a wide range of properties and can be tailored to specific applications. Geometries include long, aligned or woven fibre, sheets stacked in a regular sequence, with successive sheets at an angle to one another, short fibres randomly distributed in two or three dimensions, or complete fibre preforms. The stacked lay‑up gives good properties in several directions within a plane (but not through the thickness), while short fibre materials are easier to handle in fabrication. A preform can be specifically designed to meet the stresses in a particular component. Among the fibres used are glass, by far the most common and cheapest, and for high performance applications the more expensive carbon, ceramic, aramid and thermoplastic materials. In each case, the polymer matrix must have a low enough viscosity to impregnate the fibre reinforcement before solidifying, and must not degrade the fibre through chemical interaction. Properties of composites depend on the type, orientation and geometrical distribution of the fibre, the quality of fabrication, and the type of matrix employed. The vital importance of the latter two points is often overlooked. Generally, the modulus and strength are enhanced in the fibre direction(s). Because of the low density of the composite, the specific properties (the ratio of the property to the specific gravity) can be very high, well in excess of those of metal materials. Advantages of Composites in the Automobile Industry Fibre reinforced composites offer a wide range of advantages to the automotive industry. Perhaps the most widely recognised benefit is the potential for weight saving offered by their low density. Reduced weight could of course lead to lower fuel consumption, with all the economic and environmental implications that brings. However, there is a range of other economic benefits: • Component designs can be such that the fibres lie in the direction of the principal stresses, and the amount of fibre used is sufficient to withstand the stress, thus optimising materials usage. • The design and fabrication routes can be combined so that complicated shaped components can be moulded in one process rather than being assembled from components or machined from blank, potentially reducing manufacturing costs. • Composites can be fabricated relatively easily at low pressures and temperatures of no more than 200°C, which again has implications for production costs. • The excellent resistance to corrosion and other chemical environments could help manufacturers to prolong the lifetime of individual components and whole vehicles. Strangely, composite materials are not currently being extensively used. A major factor contributing to this is a lack of information about composite properties, particularly in relation to impact. However, there are other reasons: • Users are not familiar with composite materials and the benefits they can bring to the automotive industry • Lack of processing equipment, with most production lines designed to use metals • Little information on design and design practices/codes and hence excessive safety factors • Composites are often seen as a substitute rather than a designed replacement, leading to inefficient usage • Difficulties of joining and repairing composites • Poor transverse and shear properties of unidirectional materials • Doubts about the trade off between lower weight (leading to better vehicle performance and lower petrol consumption) and the possible extra cost of materials and fabrication • Difficulties with the surface finish and painting of composites. These other issues will of course, need to be addressed before composites find wider recognition in the automotive industry. Performance of Composites under Impact Conditions Unlike metals, fibre reinforced composite materials do not undergo plastic deformation under impact. A local blow or impact will therefore either result in elastic deformation or damage (debonding, matrix cracking, fibre failure). The energy absorbed in an impact depends on, among other things, the strength of the fibre-resin bond. If the bonding is strong, a crack may propagate through the material virtually undeviated. With a weaker bond, the crack path may be much more irregular, leading to extensive interfacial debonding possibly associated with fibre pull out, and hence considerable energy absorption. Care must be taken to ensure bonds are not too weak, as the shear strength of the material will then be inadequate. The presence of an external stress field (i.e. an applied tensile/compressive load) complicates matters because of interaction between the stress and the crack front. Current Methods of Studying Impact Performance Although the major damage mechanisms (matrix cracking, debonding and fibre failure) may appear individually simple, their interaction and the effects of fibre type and lay-up, distribution and geometrical nature, plus the type and state of the matrix, fibre resin bond and environmental effects, make the subject of impact and subsequent failure very complex. There are a number of ways of measuring the performance of composites under impact conditions but none of these is particularly satisfactory AEA Technology Programme As a result of the seriousness of the problem, the lack of a systematic approach to impact studies, and dissatisfaction with existing experimental and analytical methods, AEA Technology organised the LINK club programme on behalf of the DTI with a number of industrial partners. The aim of this work was to investigate the impact performance of composites in a more systematic manner and compare the results with those obtained from the Impact computer code and the more advanced Abaqus and Vecdyna3D codes. Materials Preparation The base materials used in the programme were prepared from quasi-isotropic lay-ups of T300 or XAS carbon fibre, Kevlar 49 aramid fibre, and R glass fibre in epoxy resin. Other work involved a much smaller number of cross ply, glass fibre phenolic and SiC glass ceramic specimens and HTA and IMS carbon fibres in toughened epoxy resins. Panel specimens were subjected to low, medium and high velocity impacts whilst unstressed or stressed in tension/compression to a maximum of 0.5% strain. The impact velocities were up to a few ms-1, 3-200m.s-1, and >900m.s-1 respectively, corresponding to a maximum impact energy of 2.69KJ. Specimens were prepared by the industrial members of the programme using, where possible, their own products. The majority of the testing work was carried out using two main test rigs, figures 1 and 2. Prior to testing, some of the plates were examined with the ultrasonic C scan technique to check for deplying and the presence of flaws. After impact, specimens were examined visually, and some were C scanned to detect the extent of delamination. Alternatively, the residual strength (or strain) after impact was measured and compared with that of unused material of the same type. Generally, impact, with or without pre-straining, causes delamination, breakout of rear plies, and sometimes complete penetration. Damage was assessed by the width of the delaminated region indicated by the C scan. Figure 3 this shows the failure strain of the material impacted whilst pre-strained, and then strained to failure if necessary. It is clear that simultaneous straining and impacting results in a lower strain to failure than sequential impacting and straining (though this is not invariably the case). 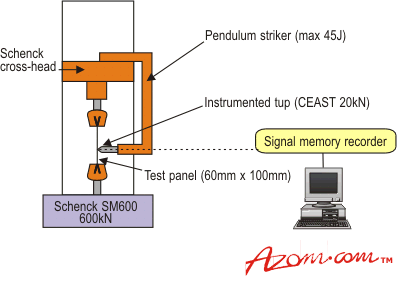 | Figure 1. Pendulum impact test rig for low velocity impact on stressed composites. | 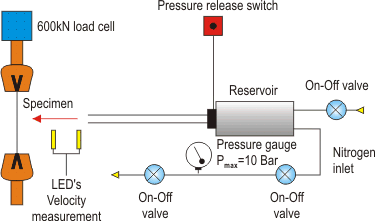 | Figure 2. Gas gun used for intermediate impact on stressed composites. | 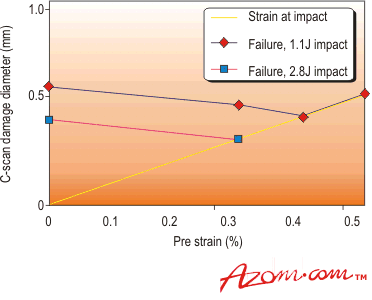 | Figure 3. Failure data for composite panels impacted at low range energies and pre-stresses. | Low Velocity Impact Testing C scan measurements, figure 4, indicate a slight increase in damage for the base materials under a tensile preload and a large increase in damages for carbon composite under a compressive preload. Though damage increases with tensile or compressive preload for all types of carbon fibre, the tougher the resin the less the damage. For impacts at 1.75m.s-1 and 5J the residual strain to failure of XAS carbon composite falls with increasing tensile pre-strain, as does that of a woven glass phenolic system and Kevlar specimens, though the glass epoxy specimens exhibit a rising strain to failure. Under a compressive load the carbon composite again shows a decrease in properties, while the other two types of material are insensitive to compressive pre-strain. The SiC glass ceramic composite was also sensitive to compressive pre-strain. 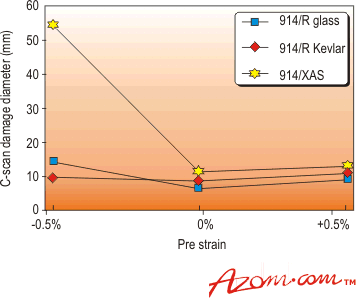 | Figure 4. Comparison of delamination diameter from C scans for 914/XAS, 914 R Glass and 914/Kevlar as a function of pre-strain for 3J impacts at 1.35m.s-1 with a 6mm impactor. | Intermediate Velocity Impact Testing C scan measurements showed that none of the base materials was sensitive to tensile pre-strain but that Kevlar and carbon composites were markedly affected by a compressive pre-strain as was R glass material to a very small extent. Again, the carbon composite results were very sensitive to the toughness of the resin, with the relationship, the tougher the matrix the less the delamination. Impact at an energy of 2.8J and 80m.s-1 under a tensile pre-strain indicated that the performance of carbon fibre composites depended on the strength of the fibre, with higher strength material giving better results. Sensitivity to compressive pre-strain was also exhibited by IMS and HTA carbon fibre in epoxy resin. High Velocity Impact Testing High velocity studies were more limited in extent that the others. Glass fibre composites delaminated more than carbon and Kevlar composites, but absorbed twice as much energy when struck with 5.56mm armour piercing bullets. In other work involving impact at 1.4km.s-1, pre-strain exacerbated damage, which involved complete penetration of the target. Modelling Comparison of the physical test results with the computer models showed that the Vecdyna3D code is the best of the three. The Impact code gave a poor account at both low and high velocities. The Abaqus code took a very long time to run and needs the addition of suitable failure criteria. Overall it is important to use the correct boundary conditions in the models. Potential failure mechanisms are complex and interrelated and if one is not correctly predicted this may affect the prediction of the others. The results are complicated because of the number of variables involved and the fact that the critical variables may change with impact velocity. Compressive pre-strain appears more damaging than tensile pre-strain, probably because the initial delamination allows the plies to buckle more easily in compression. It should be noted that sometimes the effects of materials variables on delamination, for example, will differ from their effects on residual strength. Conclusions There are obviously drawbacks to the use of fibre-reinforced composites in the automotive industry. The impact studies have shown that materials respond differently to impact under different conditions, and like all other materials they have advantages and disadvantages. In the present case these may be amplified because of the user's unfamiliarity with the materials and the lack of suitable design methods. This need not deter engineers and designers. For example, glass is a brittle material but is extensively used in buildings, transportation etc. Timber beams are employed in construction work though they often show significant longitudinal cracking. Concrete, a heterogeneous material, is used on a massive scale worldwide. In each case, users are familiar with the materials and their limitations and employ them successfully. The further development of impact performance models will enable automotive engineers to design and test composite products more cost effectively. This will add to the body of knowledge on impact performance, enabling the automotive industry to recognise the limitations of composites, whilst exploiting their undoubted benefits in the most appropriate areas. |