Updated by Reginald Davey 03/05/2023
Developing materials that can withstand extreme environments is key for a number of industries currently. This article will explore the properties, manufacture, and key industrial applications of Inconel 690TM, a super alloy that has found widespread use in several sectors.
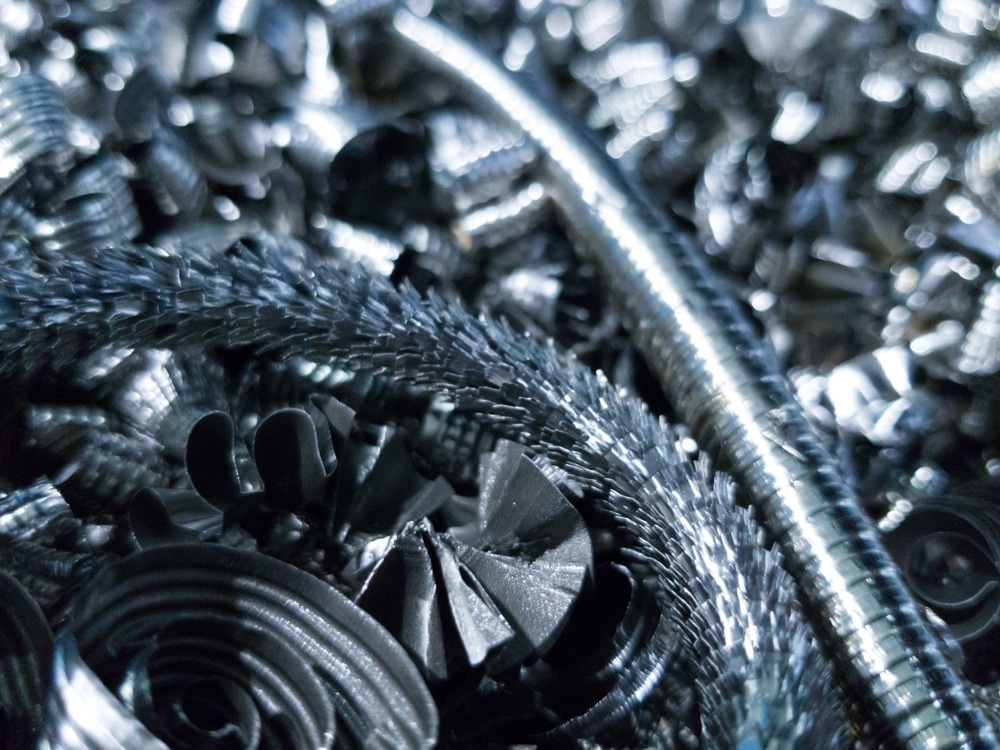
Image Credit: Photon collector/Shutterstock.com
Introduction
Super alloys have good creep and oxidation resistance. They are also known as high-performance alloys and can be formed in different shapes. Work hardening, precipitation hardening, and solid-solution hardening are performed for strengthening the super alloys.
These alloys have the capacity to function at very high temperatures and severe mechanical stress and also where high surface stability is required. For this reason, Inconel 690 is commonly used in applications that must withstand extreme environments.
Inconel 690 is a high-chromium content alloy. Due to its high chromium content, it has superior resistance to environmental conditions such as oxidizing chemicals and hot gases. This makes it an ideal alloy for high-performance applications that require superior durability and damage resistance.
History of Inconel
The Inconel family of alloys received their trademark in the 1930s. The trademark was registered by the International Nickel Company, Ltd., now known as Vale Canada.
Inconel alloys were first used in industrial applications such as the development of the Whittle jet engine. Special Metals Corporation, a US supplier of refractory alloys, acquired the Inconel trademark in 1998.
The following datasheet gives an overview of Inconel 690’s chemical composition, physical properties, mechanical properties, and thermal properties.
Chemical Composition
The chemical composition of Inconel 690™ is outlined in the following table.
Element |
Content (%) |
Chromium, Cr |
27-31 |
Iron, Fe |
7-11 |
Silicon, Si |
0.5 max |
Manganese, Mn |
0.5 max |
Copper, Cu |
0.5 max |
Silicon, Si |
0.5 max |
Carbon, C |
0.05 max |
Sulfur, S |
0.015 max |
Nickel, Ni |
Remainder |
Physical Properties
The physical properties of Inconel 690 ™ are given in the following table.
Properties |
Metric |
Imperial |
Density |
8.19 g/cm³ |
0.296 lb/in³ |
Melting point |
1343-1377°C |
2450-2510°F |
Mechanical Properties
The mechanical properties of Inconel 690™ are displayed in the following table.
Properties |
Metric |
Imperial |
Poisson's ratio |
0.29 |
0.29 |
Hardness |
85 |
85 |
Thermal Properties
The following table shows the thermal properties of Inconel 690™.
Properties |
Metric |
Imperial |
Thermal conductivity |
12.1 W/mK |
84 BTU in/hr.ft².°F |
Other Designations
Other designations that are equivalent to Inconel 690™ include:
Fabrication and Heat Treatment
Inconel 690 can be fabricated using a number of conventional processes. This section will provide an overview of fabrication and heat treatment methods that can be used to produce this material..
Machinability
Inconel 690™ can be machined using conventional machining methods, which are used for iron-based alloys. Machining operations are performed using commercial coolants. High-speed operations, such as grinding, milling, or turning, are performed using water-base coolants.
Forming
Inconel 690™ can be formed using all conventional techniques.
Welding
Inconel 690™ is welded using gas-tungsten arc welding, shielded metal-arc welding, gas metal-arc welding, and submerged-arc welding methods.
Heat Treatment
Inconel 690™ does not react to heat treatment.
Forging
Inconel 690™ is forged at 1038 to 1233°C (1900 to 2250°F).
Hot Working
Inconel 690™ is hot worked at 872 to 1205°C (1600 to 2200°F).
Cold Working
Inconel 690™ is cold-worked using standard tooling.
Annealing
Inconel 690™ is annealed at 1038°C (1900°F) followed by cooling.
Aging
Inconel 690™ does not react to aging thermal treatment.
Hardening
Inconel 690™ is hardened by cold working.
Applications
Inconel 690TM is supplied in commercial forms such as pipes and tubes. The superior stress cracking resistance means that Inconel 690 has superseded Inconel 600 and 601 in key industrial applications.
Inconel 690™ is used in the following applications:
- Duct work
- Steam generators
- Furnaces
- Petrochemical heaters
- High-temperature burners
- Heat exchangers
- High-temperature applications which are commonly exposed to caustic solutions
- Metal pickling operations due to Inconel 690’s resistance to nitric acid and hydrofluoric acid mixtures.
One of the key industries that Inconel 690 has found widespread application in is the nuclear power industry due to the need for alloys which can withstand extremes of heat and other harmful environments. It is a commonly used alloy in nuclear reactor steam generators.
More from AZoM: Metal Alloys - Classification and Properties of Copper and Copper Alloy