Aircraft manufacturers have been benefiting from thermoplastic composites in the form of a tough, durable structural material for more than 15 years and aerospace design allowable databases are available for both commercial and military applications.
.jpg)
Although the reasons behind the selection of a thermoplastic composite are different, there are several key reasons that drive OEMs’ interest in thermoplastics. First, very low void thermoplastic unitape development and automation solutions eliminate the utilization of an autoclave in the production of very low void content thermoplastic structure. Second is the ability to fusion weld thermoplastics through induction or resistance welding techniques, providing a feasible way of reducing weight and cost without using fasteners. Lastly, the migration towards composite fuselages necessitates the removal of metallic structural brackets and associated effects of galvanic corrosion.
Besides superior fire retardancy and structural properties, thermoplastic composites also provide cost effective processes such as thermoforming and compression molding to fabricate the multiple metallic brackets. Very high consistency, low void content thermoplastic prepreg materials have become essential in several emerging automation solutions.
Polymer Technology
Thermoplastic polymers are categorized into amorphous and semi-crystalline. Amorphous thermoplastics do not form crystalline structure and are moldable at temperatures nearer to their glass transition temperature (Tg) when compared to semi-crystalline polymers. However, one concern with amorphous thermoplastics is their poor resistance to certain solvents.
A semi-crystalline polymer has areas where it is amorphous and areas where it is closely packed in a crystal lattice. The amount of crystallinity in a specific part is based on the type of the polymer and the cooling rate utilized in forming that part. A semi-crystalline polymer has both Tg and melts temperature Tm, a point at which the crystalline structure breaks down.
Key thermoplastics utilized in composites include
- Poly –ether-imide (PEI) - Amorphous
- Nylons – Amorphous or Semi-Crystalline
- Poly-ether-ketone-ketone (PEKK) – Semi-Crystalline
- Poly-ether-ether-ketone (PEEK) – Semi-Crystalline
- Poly-phenylene-sulfide (PPS) – Semi-Crystalline
Material Forms
Thermoplastic material exists in three material forms. The first form is the fabric prepregs wherein a typical glass or carbon fiber is woven material and a thermoplastic resin is integrated into the fabrics. They are slightly drapable and conformable and are typically called as semi-pregs due to the presence of most of the resin on the fabric surface. The impregnation occurs in a high-temperature autoclave. TenCate manufactures a broad range of materials under its Cetex brand name utilizing carbon and fiberglass fabrics with different resins such as PEI, PA, PEEK, and PPS.
Second, are the reinforced thermoplastic laminates (RTLs). An RTL obtains better fiber bundle impregnation of the higher viscosity thermoplastic resins in high pressure and high-temperature thermoforming cycle. TenCate provides these materials under its Cetex RTL brand name.
The third is a thermoplastic unitape, ranging from a 1/8 inch slit tape to a tape with a width of 6-12". This material form enables the use of automated tape laying and fiber placement equipment with maximum efficiency. Various automation solutions are available with this form via fiber tape placement (in situ), continuous compression molding or tape laying. TenCate supplies this material form under the Cetex Thermo-Lite brand name.
Advantages of Thermoplastic Composites
Thermoplastic composites have been utilized for several years successfully. Some of the advantages of thermoplastic composites.
- Ability to utilize short cycle time thermoforming part fabrication techniques
- Low moisture uptake
- Good toughness and damage resistance
- Room temperature storage quality eliminates the use of any refrigeration and allows large structure fabrication without the limits of outtime constraints
- Ability to re-form parts as thermoplastic resins can retain their properties even after repeated heating and cooling
- Very low void content
- Alternatives to part fabrication without using autoclaves
- Fire retardancy
Disadvantages of Thermoplastic Composites Over Thermosets
Some of the disadvantages of thermoplastic composites over thermosets include:
- High initial raw material cost over thermosets
- Higher processing temperatures
- Traditional part maker unfamiliarity with today’s thermoplastic composite processing options
- Typically higher cost tooling due to the requirement for metal tooling for thermoplastic parts. However, it is possible to reduce lead time and cost by using aluminum tools for prototyping purposes.
Lists out the Tg and process temperature for various thermoplastic polymers for the following Table 1.
Table 1. Thermoplastic Polymers Used in Composites
Polymer |
Tg |
Process |
Temperature Morphology |
PEEK |
290°F (143°C) |
715° – 740°F (380° – 395° C) |
Semi-Crystalline |
PEI |
423°F (217°C) |
575° – 625°F (300° – 330° C) |
Amorphous |
PPS |
192°F (89°C) |
550° – 620°F (290° – 325° C) |
Semi-Crystalline |
PEKK |
312°F (156°C) |
645° – 690°F (340° – 365° C) |
Semi-Crystalline |
Nylon – 11 |
108°F (42°C) |
360° – 400°F (180° – 205° C) |
Semi-Crystalline |
Nylon – 6 |
116°F (47°C) |
415° – 450°F (210° – 230° C) |
Semi-Crystalline |
Other Considerations Associated with Thermoplastics
The degree of crystallinity affects the properties of semi-crystalline thermoplastic polymers. If the crystallinity is low, then the composite is tough but with poor solvent resistance. The majority of the engineered thermoplastics demonstrate very fast crystallization rates. Another key concern with any composite structure is the way of attaching a piece with other parts of a structure. To weld structures, it is required to soften the material by heating the bondline up to the processing temperature.
Manufacturing Processes
Recent developments in automated techniques facilitate the cost-effective production of thermoplastic parts. Several companies develop a wide range of automated techniques to enhance production speed and thermoplastic part quality. Some of the most common techniques used include Automated Fiber Placement and Tape Placement, Thermoforming, Robotic Lay-up, and Continuous Compression Molding (CCM).
Automated Fiber Placement and Tape Placement
.jpg)
Companies produce parts by utilizing thermoplastic composite tows and slit tape. The tape is placed on a tool or mandrel under temperature and pressure, resulting in the consolidation of the material without any further processing. However, the unitapes utilized must have very low void contents as it is a relatively low-pressure process. Technology utilized by TenCate in the production of thermoplastic unitapes innately provides both superior polymer distribution and low voids. Figure 1 shows a cross section photo illustrating TenCate’s TC1200 PEEK unitape laminates.
.jpg)
Figure 1. A cross section photo showing TenCate’s TC1200 PEEK unitape laminates. Note the very even resin distribution around the carbon fiber tows and the low void content in the laminates.
Thermoforming
Thermoforming for thermoplastic composites is similar to the thermoforming process typically utilized for non-reinforced plastics. This process involves the heating of a consolidated thermoplastic laminate up to the processing temperature utilizing IR heaters followed by molding of the part at a stamping station using a male and female mold. The total time to create parts is often below 5 minutes.
Robotic Lay-up
.jpg)
Figure 2.
Machinery rapidly lays down thermoplastic tape in the fiber orientation as per the design. A local heating source is used to tack the plies followed by the press consolidation and thermoforming of the resulting blanks into parts.
CCM
CCM, an automated, semi-continuous production process, is capable of taking thermoplastic composites for producing flat panels or highly shaped profiles of effectively unlimited length.
Conclusion
Finding low-cost production techniques is the current trend for the composites industry to lower overall part costs. A major effort focuses on producing parts utilizing processes without an autoclave. Composites reinforced with thermoplastic polymers provide designers and production engineers a variety of processes that make parts rapidly and reliably. With recent developments in automation and qualities such as room temperature storage, weldability, superior toughness, and almost unlimited shelf life together, thermoplastic composites will be useful in more applications.
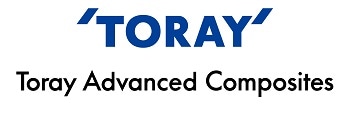
This information has been sourced, reviewed and adapted from materials provided by Toray Advanced Composites.
For more information on this source, please visit Toray Advanced Composites..