A popular and nondestructive technique is generally employed to calculate the thickness of a material from one side. This technique is called ultrasonic thickness gaging. In the late 1940s, the first commercial ultrasonic gages based on sonar principles were introduced and then in the 1970s, portable instruments were used for a wide range of test applications. Later, advancements in microprocessor technology resulted in new levels of performance in current generation of instruments that are compact, sophisticated and user-friendly.
Ultrasonic Thickness Gages
Ultrasonic testing can be done to measure almost any kind of material. Ultrasonic thickness gages can be configured for glass, plastics, metals, ceramics, fiberglass, and composites. It is possible to do in-process or on-line measurement of rolled metal and extruded plastics, as is measurement of separate coatings or layers in multilayer fabrications. In fact, biological samples and liquid levels can be calculated. Ultrasonic gaging does not involve any cutting procedure and hence offers a nondestructive alternative. On the other hand, materials such as foam, paper, wood and concrete products are not suitable for traditional ultrasonic gaging.
Operation Principle behind Ultrasonic Thickness Gages
Sound energy can be produced across a wide frequency spectrum. When the frequency is higher, the pitch we perceive also tends to be higher. Nearly all ultrasonic testing is carried out between 500 KHz and 20 MHz frequency range. However, there are certain unique instruments that go as high as 225 MHz and down to 50 KHz or lower.
Ultrasonic thickness gages can accurately calculate the time taken by a sound pulse produced by an ultrasonic transducer to traverse a test piece. A piezoelectric element is included in the transducer that is stimulated by a short electrical impulse to produce ultrasonic waves. The sound waves get merged within the test material and travel across it until they bump into a back wall. These reflections again travel back to the ultrasonic transducer, which changes the sound energy into electrical energy.
Sound waves are transmitted at different velocities by different materials and they are typically slower in soft materials and faster in hard materials. Sound velocity can vary with respect to temperature. Hence, it is important that an ultrasonic thickness gage must be calibrated to the speed of sound in the material that is being determined, and precision can be as good as this calibration.
Precision Ultrasonic Gaging Techniques
Three common techniques are available for calculating the time interval representing the travel of sound wave via the test piece. The most common technique is Mode 1, wherein the time interval between the excitation pulse that produces sound waves and the first returning echo is measured, and a small zero offset value is then subtracted to offset for transducer delays, fixed instrument and cable. In Mode 2, the time interval between the first backwall echo and the returning echo from the test piece’s surface is measured, and in Mode 3 the time interval between two consecutive backwall echoes is measured. Specific application needs and the type of transducer will determine the choice of mode.
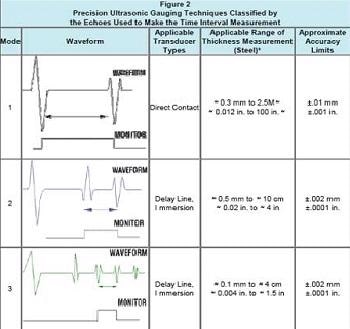
Types of Transducers
Delay Line Transducers
Delay line transducers are utilized in thin material measurements, where it is necessary to divide the excitation pulse recovery from backwall echoes. In addition, delay line transducers can be utilized as a thermal insulator and can even be shaped to enhance sound coupling into confined or curved spaces.
Contact Transducers
Contact transducers are typically employed in direct contact with the test piece. With the help of contact transducers, measurements can be easily done and these instruments are widely used for routine thickness gaging applications, except corrosion gaging.
Dual Element Transducers
Dual element transducers, also known as duals, are mainly utilized for determining rough and corroded surfaces. Duals are suitable for corrosion survey applications, even though measurement using duals is at times not so precise when compared to other types of transducers.
Things to Consider in Ultrasonic Gaging Application
Choosing the right gage and transducer depends on a number of factors such as the material to be measured, geometry, thickness range, accuracy requirements, temperature, and any specific conditions that may exist.
Conclusion
Ultrasonic thickness gages are compact and easy to use and allow users to calculate the thickness of a material from one side only. The instruments are ideal for using in material wall thickness testing applications.
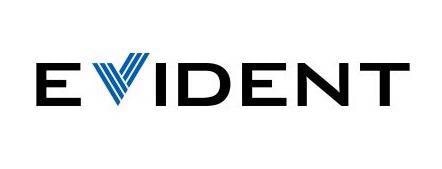
This information has been sourced, reviewed and adapted from materials provided by Evident Corporation.
For more information on this source, please visit Evident Corporation.