Besides record levels of global passenger vehicles production, the automotive industry is also witnessing higher levels of investment in support of research and development activities. The challenge in meeting global demand and addressing compliance with changing regulations drives many automotive manufacturers towards strategic partnerships. Most of these collaborations focus on streamlined approaches to tackle issues like materials specification for lightweighting initiatives.
Image Credit: Gorodenkoff/Shutterstock
One example is the joint development deal between General Motors and Teijin to develop technologies for mass production of carbon fiber-based components. A key objective of the partnership is to reduce cost of production of components using these novel materials while reducing weight of vehicles by up to 20% by integrating the materials into the design of vehicle platforms. Another example is the collaboration between Volkswagen Group and Zwick/Roell AG of Ulm, a provider of materials and component testing solutions.
Major Initiatives in Automotive Industry
AleksanderKoprivc, Automotive Industry Manager at Zwick, informed that Zwick solutions are commonly utilized for validating new materials and technologies. Several key initiatives have been started in the automotive industry for the characterization of materials ranging from magnesium to composites for power train, chassis and body applications. The launch of hybrid electric vehicles and other powertrain technologies has promoted testing practices to validate the functionality of novel sensors and safety of batteries. Volkswagen Group is actively involved in component design to work with up-and-coming powertrain technologies in addition to assemblies equipped with novel material systems to improve fuel efficiency. The continuous expansion of major initiatives like ‘lightweighting’ drives manufacturers to shift their focus towards component validation and testing.
Key Strategy of Volkswagen Group
Volkswagen Group, which includes the Skoda, Porsche, and Audi brands, is creating sizeable economies of scale through a novel production strategy called MQB or modular transversal toolkit. Using unique and variable parts, this toolkit provides more options in length, width and height to develop more models, which include regional variations. The strategy not promotes the trends of sizeable reductions in fuel consumption, weight, and emissions, but also minimizes engineering hours per vehicle and unit cost.
According to Koprivc, the partnership between Volkswagen Group and Zwick is to develop materials test and quality assurance solutions that promote the MQB strategy. Volkswagen Group is currently using Zwick test equipment in large volume in its 100 manufacturing facilities across the world. Materials’ testing is an important element of the MQB concept, which involves the selection of materials with unique mechanical properties for specific applications. New types of aluminum and steel alloys and alloys in combination with fiber composites or polymers are used to achieve objectives such as lower unit cost and weight reduction.
Significance of Material Testing
Charlie Lin, Quality Laboratory Manager at Volkswagen’s production facility at Chattanooga, Tennessee, informed that the company has rigorous materials and component specifications relating to vehicle components. It is necessary to understand why there is a difference in test results produced at one plant when compared to products manufactured at other plants worldwide. Moreover, as new components are manufactured using new materials and technologies, OEMs employ testing practices to determine why there is a variation in values from those provided by suppliers. Test throughput levels are emphasized to facilitate timely responses to production and design teams alike. It is necessary to reduce changeover time between tests because test labs look for new approaches to improve test throughput.
Zwick Z010 Allround-Line System
The Zwick Z010 Allround-Line system can measure steering wheel adjustment mechanisms for three different test profiles on three different testing axes, a solution to fulfill the requirement for platform flexibility. The same platform can also be setup to test clutch operating forces by using pneumatic specimen grips and adjusting for different clutch dimensions.
Koprivc informed that considerable time can be saved if the equipment can be easily and rapidly reconfigured for multiple tests. This capability is vital on the production floor.
Volkswagen’s Lin informed that producing qualitative results from tests on compression forces, impact strength, and tensile strength on actual vehicle components and having the capability to reproduce those same tests with a high degree of repeatability is vital.
Conclusion
ZwickRoell joins forces with standardization organizations to monitor and take part in standards development. The company also works with material and component suppliers, and customers for the development of specific standards. Koprivc told that the company helps suppliers to meet the requirements of Volkswagen testing standards. There are nearly 50 different Volkswagen testing standards where ZwickRoell machines may be applied.
About ZwickRoell
ZwickRoell is one of the top-ranking manufacturers of static and dynamic materials testing systems worldwide. With our extensive portfolio of testing machines, systems, and software we supply customized solutions for almost all test tasks required in the area of modern mechanical materials testing.
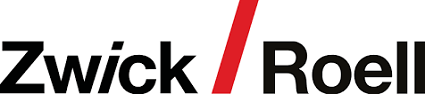
This information has been sourced, reviewed and adapted from materials provided by ZwickRoell GmbH Co. KG.
For more information on this source, please visit ZwickRoell GmbH Co. KG.