Copper has high electrical and thermal conductivity and hence is considered to be a very useful metal. It occurs abundantly in nature and is affordably priced. The metal is employed in a number of applications, but is mostly used in electronics, industrial machinery and construction materials.
Sulfur concentration in copper or copper alloy tends to be an essential quality control parameter during copper production. High levels of sulfur can cause embrittlement, which markedly reduces ductility. When the amount of sulfur present in the product is verified, users can use such a product to bend, form and spool without worrying about cracking.
Accessories
Accessories include 528-018 or 528-018HP (preheated) ceramic crucible, HP copper accelerator (502-492) or copper accelerator (501-263), tongs (761-929), and metal scoop (773-579).
.jpg)
Figure 1. CS844 Elemental Analyzer.
Calibration
Certified bodies like NIST, BCS, JK and JSS have many certified copper base reference materials (SRM/CRM). Single or multipoint calibration curves can be used.
Method Parameters
General Parameters
- Purge Time: 10 seconds
- Analysis Delay: 20 seconds
- Sample cool time: 10 seconds
- Furnace power: 70±5%
- Furnace mode: Constant
Element Parameters - Sulfur
- Starting Baseline: 2 seconds
- Ending Baseline: 2 seconds
- Integration Delay: 0 seconds
- Integration Time: 60 seconds
- Use Comparator: No
- Use Endline: Yes
- Range Select: Auto
- Range Lower Limit: 800
- Range Upper Limit: 950
It should be noted that furnace power should be tuned based on facility incoming line-power under load. Also, the furnace power should be reduced if oxides occur during examination.
Analysis Notes
When compared to powders or chips, solid samples burn less aggressively. However, care should be taken while setting up the instrument with the densest sample. LECO 502-403 Copper Pin Samples or an equivalent solid copper sample weighing ~1.0 g can be employed when setting up the instrument. Before beginning the process, a clean combustion tube and a dust filter are required.
Instrument Setup
This process reduces the power level from the maximum set in a usual technique so as to reduce the dust generated from sample combustion. The power settings are given in the Method Parameters section.
- First, add ~1.0 g Copper Accelerator to a pre-heated 528-018 or 528-018HP Crucible so that it is uniformly distributed on the base of the crucible.
- Place a ~1.0 g copper solid or the LECO 502-403 Copper Pin inside the crucible. Then, enter a 1.0 g weight into the Sample login. After this, place the crucible on the furnace pedestal and then press Analyze.
- The plate current must stabilize at ~320 to 360 mA for complete combustion.
- After the combustion cycle, unlock the furnace and take out the crucible with the help of tongs. Study the sample while it is still hot. The sample should emerge as a flat, smooth melt without any dark spots at the base of the crucible.
- In case the plate current goes beyond 360 mA for most of the analysis, excess amount of oxide dust would be produced, which will result in low sulfur recovery.
- If dust has been produced, then clean the dust filter and combustion tube, decrease the Furnace Power and repeat from the second step.
.jpg)
Figure 2. Example of a good burn.
.jpg)
Figure 3. Example of a sample burn when power parameters are slightly high.
.jpg)
Figure 4. Example of a sample burn when power parameters are significantly high.
Typical Results
|
Mass |
Sulfur % |
IARM 90a |
~1.0 g |
0.0370 |
0.037% S |
|
0.0371 |
±0.0017% S |
|
0.0371 |
|
|
0.0370 |
|
|
0.0369 |
|
|
0.0369 |
|
|
0.0370 |
|
|
0.0370 |
|
|
0.0368 |
|
|
0.0371 |
Average: |
|
0.0370 |
Std Dev: |
|
0.0001 |
NIST 885 |
~0.9 g |
0.00190 |
0.0018% S |
|
0.00185 |
±0.0003% S |
|
0.00187 |
|
|
0.00186 |
|
|
0.00188 |
|
|
0.00188 |
|
|
0.00188 |
|
|
0.00191 |
|
|
0.00190 |
|
|
0.00187 |
Average: |
|
0.00188 |
Std Dev: |
|
0.00002 |
IARM 86a |
~1.0 g |
0.0273 |
0.029% S |
|
0.0276 |
±0.0030% S |
|
0.0275 |
|
|
0.0277 |
|
|
0.0275 |
|
|
0.0275 |
|
|
0.0276 |
|
|
0.0275 |
|
|
0.0277 |
|
|
0.0277 |
Average: |
|
0.0276 |
Std Dev: |
|
0.0001 |
LECO 502-403 |
~1.0 g |
0.00098 |
0.00091% S |
|
0.00094 |
±0.000073% S |
|
0.00100 |
|
|
0.00096 |
|
|
0.00100 |
|
|
0.00094 |
|
|
0.00096 |
|
|
0.00096 |
|
|
0.00098 |
|
|
0.00097 |
Average: |
|
0.00097 |
Std Dev: |
|
0.00002 |
BCS 180/2 |
~1.0 g |
0.0074 |
0.006% S |
|
0.0073 |
|
|
0.0074 |
|
|
0.0072 |
|
|
0.0072 |
|
|
0.0075 |
|
|
0.0072 |
|
|
0.0074 |
|
|
0.0074 |
|
|
0.0074 |
Average: |
|
0.0073 |
Std Dev: |
|
0.0001 |
Conclusion
The above results demonstrate the efficiency of the CS844 Elemental Analyzer to determine the concentration of sulfur in the copper or copper alloy.
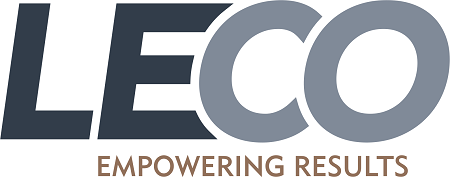
This information has been sourced, reviewed and adapted from materials provided by LECO Corporation.
For more information on this source, please visit LECO Corporation.