Austempered Ductile Iron (ADI) is a series of iron-based materials that are extremely strong, tough and wear resistant and hence widely used in gear box components and combustion engines.
However, in addition to functional aspects, safety aspects are also involved. Owing to this reason, it is necessary to monitor the modifications in the ADI production process with respect to the characteristics of the material and need to be optimized thoroughly.
Seamless Integration of Light and Electron Microscopes
Scientists generally use light and electron microscopes for micro- and nanoscopic analysis of structures and precipitations. So far, it has not been possible to precisely relocate the regions of interest when shifting the sample from the electron to the light microscope or vice versa.
To address this issue, Carl Zeiss offers an easy-to-use solution called “Shuttle&Find” for materials analysis. This correlative microscopy solution allows flawless integration of these two technologies.
ADI Material
Using different processes, ADI can be obtained by heat treatment of nodular cast iron. The minimum tensile strength of 1200 MPa and elongation at fracture of minimum 2%, results in an economical solution that offers similar performance to steels or aluminum alloys.
Equipment Used for Analysis
The present analyses were performed on a ZEISS Axio Imager.MI light microscope with motorized stage, SUPRA 55VP FE-SEM with an AsB and Bruker Quantax 200 EDS detectors, and SUPRA 40VP Field Emission-SEM (FE-SEM) integrated with an AsB detector.
As a rule, the following points have to be fulfilled to allow the correlative workflow:
- Scanning electron microscope of XIGMA, EVO, MERLIN, ULTRA and SUPRA range with an SEM adapter for correlative microscopy.
- Light microscope integrated with digital camera and motorized stage of Axio Observer, Axio Imager and SteREO Discovery series with corresponding mounting frames.
- Software compatibility requirements.
- Correlative holder.
Application of Correlative Microscopy
.jpg)
Figure 1. Light microscope image of ADI sample with a magnification of approximately 400:1. One can see the regions of interest with the precipitates.
.jpg)
Figure 2. SE image of the same area as in Fig. 1. The problem of relocating the same area with SE becomes evident
.jpg)
Figure 3. BSE image of the same area as in Fig. 1. The microstructure can be clearly seen in contrast to the SE image.
.jpg)
Figure 4. SE image of the same area as in Fig. 1 overlapped with molybdenum, iron, and phosphorus mappings obtained with EDS.
The chief investigation task was elemental analysis and precise description of the materials’ microstructure. However, only correlative microscopy can be used for this purpose. This is because the precipitates enabled a methodical examination in the scanning electron microscope after being studied in the light microscope only in case of an exact relocation (see Figures 1-4 for further details).
Moreover, the task turned to be rather difficult because only the precipitates in the scanning electron microscope with the backscatter electron detector can be detected. Also, the chemical composition of precipitates can be identified only with the help of an EDS detector. Therefore, the precise relocation of the region of interest is extremely important to eliminate time consuming searches.
Carl Zeiss’ correlative microscopy solution, "Shuttle&Find" enables the exact relocation of the region of interest on metallographic samples even at intense magnifications in electron and light microscopes, and hence can be used to meet such application requirements.
Results
The matrix mainly includes graphite nodules, bainite, and individual regions of austenite. The precipitates were identified in these regions. Following the relocation of the precipitates in the scanning electron microscope using the "Shuttle&Find" solution, the region was examined with EDS for carbon, phosphorus, iron and molybdenum.
The EDS’ spatial resolution in this experimentation s limited with the purpose to offer data about the actual position of the adjacent elements. However, the EDS mappings demonstrated that carbon, phosphorus and molybdenum are detected in the same region, thus confirming the existence of molybdenum carbides and iron phosphides.
Through such hard precipitates, the wear resistance increases, while the toughness decreases. It should be noted that an acceleration voltage of 30 kV and an extended analysis time are needed to resolve molybdenum.
Conclusion
From the above experiment, it is evident that “Shuttle & Find” provides a practical solution for microstructural investigation of Austempered Ductile Iron.
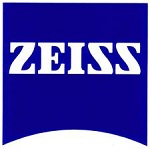
This information has been sourced, reviewed and adapted from materials provided by Carl Zeiss Microscopy GmbH.
For more information on this source, please visit Carl Zeiss Microscopy GmbH.