Impact tests are utilized to study a material’s toughness, which is a key property that plays a significant role in the longevity of a structure. For instance, an aircraft may experience impact when it is hit by a bird during cruising, or when it is struck by debris found on the runway during its takeoff and landing, and due to several other reasons.
Tinius Olsen Impact Testers
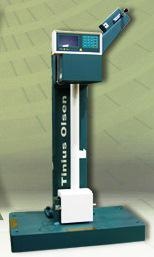
Since 1900, when manufacturers started realizing the importance of impact tests, there has been no change in the basic physical aspects of either the test machine or the test procedure. It is a pendulum-type single-blow impact test that involves the use of a notched test piece, which will be tested by either of the two techniques, namely the Izod test and Charpy test. In this scenario, Tinius Olsen comes as a game changer with its impact testers with a testing capacity of up to 542 J, quality testing, superior data acquisition capability, accuracy and robustness.
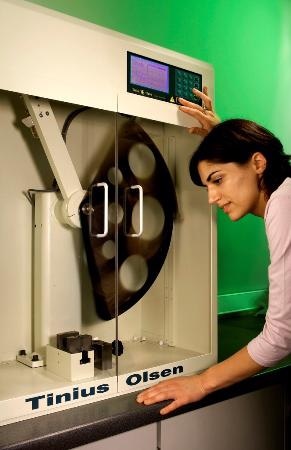
The test specimens utilized are according to the specifications outlined by the National Institute of Standards and Technology. The Tinius Olsen impact testers are engineered to meet the requirements of ISO 148, EN10045 -2, and ASTM E23 standards. They are widely utilized for purposes such as material acceptance, research and development, and quality control. The test results are normally presented as the energy needed for fracturing the test piece.
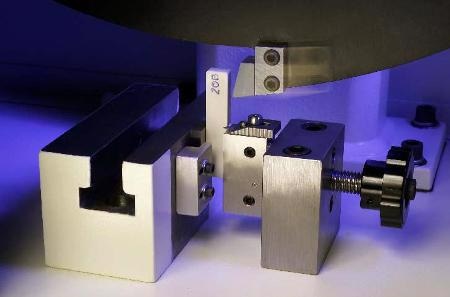
Conclusion
Tinius Olsen impact testers have been widely adopted by manufacturers from all across the world in order to ensure the behavior and toughness of their products under various conditions.
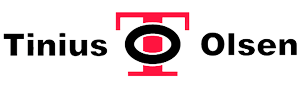
This information has been sourced, reviewed and adapted from materials provided by Tinius Olsen.
For more information on this source, please visit Tinius Olsen.