Feb 15 2001
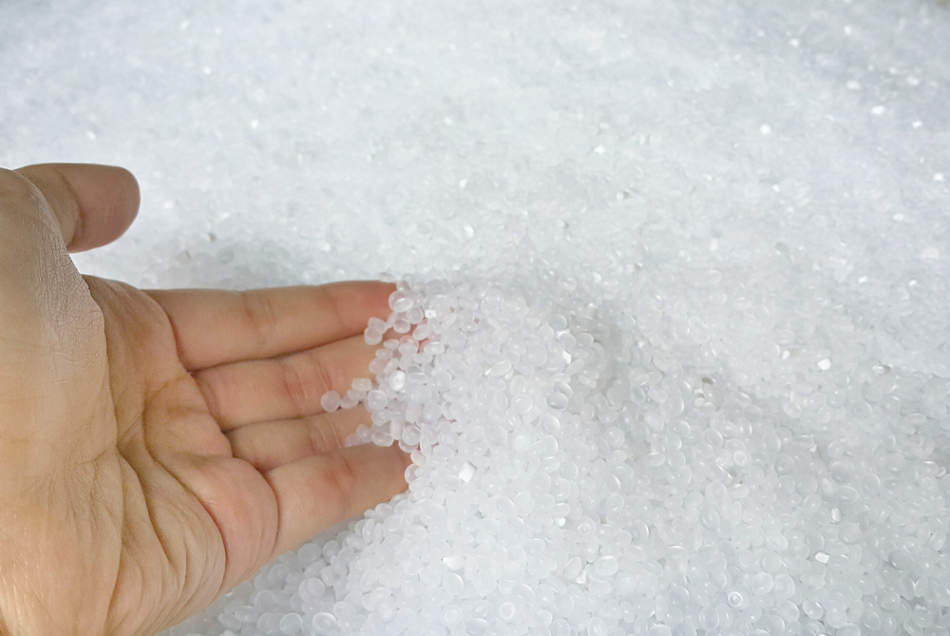
Image Credit: Tommie Bear/Shutterstock.com
Over the past decade, composites have overtaken aluminum as the production material of choice in the aviation and transportation industries. This rise was mostly driven by thermoset composites, but thermoplastic composites are poised to emerge as the new material of choice.
Composite materials are defined by three primary types of components: a resin matrix, an armature and operational additives. Thermoset composites are transformed from a liquid to a solid through a no-reversible chemical change, while thermoplastic composites are solidified through a reversible thermal curing process.
While structural polymer composites have many beneficial properties such as low density, good insulation, environmental resistance, and good mechanical properties, they can be chemically unstable. For example, an impregnated intermediate or prepreg that has a limited shelf life.
Thermoplastic composites (TMCs) evolved from structural polymer composites. These materials do not experience chemical instability because they utilize a thermoplastic matrix. When heated, TMCs soften and can be remolded without degradation. When they cool, they solidify into the finished shape. This heating-cooling cycle can be repeated multiple times, giving the product an almost indefinite shelf life.
Thermoplastic composites could also be shaped using techniques derived from wood and metalworking. They have increased recycling and damage tolerances due to the tough nature of the matrix material.
Types of Thermoplastic Composites
Thermoplastic composites could be categorized into either Glass Mat Thermoplastics (GMT) or Advanced Thermoplastic Composites (ATC).
Glass Mat Thermoplastics (GMTs)
GMTs are thermoplastic prepregs that are superior mechanically to injection-molded reinforced thermoplastics. These materials have become quite popular in the aviation and transportation industries, and the automotive industry in particular – which represented more than 92% of international consumption in 2018. GMTs could also find widespread use in construction and marine applications.
GMTs can use nearly any thermoplastic for the matrix; however, choices have been limited to polyvinyl chloride, polypropylene, polyamide, polyesters, polycarbonate, and polyphenylene sulfide, with polypropylene accounting for about 95% of commercial use.
It is also a suitable material when service temperatures remain below 110°C. When higher temperatures are encountered and service conditions are harsher, more expensive polyphenylene sulfide can be used. E-glass fiber in the form of chopped fibers, random chopped fibers, or continuous mats is the most common reinforcing phase.
The production of GMTs is highly concentrated, with two companies – Hanwha and Quadrant – representing an overwhelming majority of global production.
Advanced Thermoplastic Composites (ATCs)
Originally, ATCs used amorphous resins such as polyethersulphone and polyetherimide for the matrix. However, in applications where increased solvent resistance was required, semi-crystalline polymers such as polyether ether ketone and polyphenylene sulfide may be employed.
A limited number of pseudothermoplastics, including polyamide-imide and polyimides, could also be used. The continuous reinforcement phase may be in strand, woven, knitted or braided fabric forms and be made from carbon, aramid and/or S-, R- and E-glass. Carbon is the most popular material for higher temperature applications, while E-glass dominates lower temperature applications.
Key Properties of Advanced Thermoplastic Composites
- Low density, hence lightweight
- Good strength
- Good toughness
- Good environmental resistance
- Ability to be remolded
- Compositions can be customized to suit a range of temperature and environmental conditions
Applications of Thermoplastic Composites
Thermoplastic composites could be applied to a variety of industries, including the automotive industry, aerospace industry, construction industry, and materials handling.
Automotive Industry
Due to their lightweight and high toughness, GMTs have been adopted by automotive industries for a variety of uses. Applications include seat frames, battery trays, bumper beams, load floors, front ends, valve covers, rocker panels, and under-engine covers.
Aerospace Industry
ATCs have found limited use in the aerospace industry, but they emerged from the need for tougher composites. Currently, composites make up greater than 50% of most modern aircraft, such as the Boeing 787.
ATCs are analogous to the first thermoset composites with fiber contents above 50% and utilize a highly aligned continuous fiber structure. Actual applications include missile and aircraft stabilizer fins, wing ribs and panels, fuselage wall linings, and overhead storage compartments.
The commercial aviation industry has been indicating that ATCs will the fabrication material of choice in the future because the adoption of these materials will translate to significant cost savings, as well as greater sustainability.
After years of chatter about the aviation industry’s embrace of thermoplastics, it now appears to be happening. Just as the automotive and other industries are getting onboard with ATCs, the aviation industry is now starting to see the light.
Construction Industry
In the construction industry, thermoplastics are commonly mixed with wood particles to create composite construction materials. Wood-plastic composites (WPCs) are typically used in place of pressure-treated wood. Recent research found that coal could potentially be used instead of wood particles to create a stronger, more durable and more water-resistant construction material. The research also suggested the production of coal plastic composites would require significantly less energy than the production of WPCs and generate fewer emissions.
ATCs could be used more widely in the construction industry for structural profiles, pipes, concrete rebars, and lightweight structural and insulating panels.
Medical Equipment
Lighter and stronger than many existing materials, the applications of ATCs in the medical equipment industry should be clear. Many companies are using these materials to make parts for wheelchairs other or equipment designed to increase mobility. ATC production processes also facilitate the creation of intricate shapes that can be customized to individual patients.
Materials Handling
The materials handling industry benefits from these thermoplastic composites in the form of pallets and cargo containers. Compared to thermosets, ATCs are easier to ship, more chemically resistant and longer-lasting.
Sources and Further Reading
This article was updated on 18th March, 2020