The Ignite process from Harper International helps companies develop advanced materials from the lab to complete commercialization helping turn customer dreams to reality. Using the broad experience of the company in thermal processing, they partner with the customer to ensure success as operations are scaled up.
.jpg)
Figure 1.
The support of Harper International to emerging industries start in early stages of research and development whether at universities, government institutions, corporate research and development centers or start ups. The company’s mission is to support these customers in turning the next generation of material innovations into new profitable markets. Success stories of customers paving the path of material science innovations are discussed below.
Activated Carbon Development
EnerG2 started work with Harper in 2009 on their energy storage materials as they refined and optimized their thermal processing regime. That work resulted in a major piece of equipment to enable their production scale operations for performing pyrolysis of activated carbon for ultra capacitors. EnerG2, based in Seattle, WA, USA, is focused exclusively on the production and development of advanced carbons for energy storage devices.
The new furnace design of Harper enables the unique requirement of EnerG2 of producing very high purity material at temperatures to 1100°C. Metallic impurities are not accepted as they may impact charge storage ability. Precise control of gas particle interactions are necessitated by the high temperatures and purity specifications.
Metallic impurities are not acceptable as they could impact charge storage ability. The purity specifications and high temperatures necessitate exacting control of gas particle interactions. Harper designed the multi-line rotary with specialty construction materials along with a ceramic lined process area to satisfy purity conditions and balanced the need for a gas tight operation on the nitrogen atmosphere through its proprietary sealing technology.
.jpg)
Figure 2.
The rotary system is presently used at EnerG2’s new Oregon facility the world’s first commited to the commercial-scale production of synthetic high-performance carbon electrode material. The facility was made possible by a $21.3 million Federal stimulus grant allocated by the US Department of Energy for manufacturers of advanced automotive batteries and energy storage technologies.
Nano-Engineered Powdered Metals
After process optimization and refinement at Harper’s Technology Center, Harper developed continuous Rotary Furnace for Allomet Corporation for producing nano-engineered powdered metals.
The system is designed to drive a high throughput of Allomet’s material by a number of multiples over previous batch systems considerably improving their operations through high productivity, short delivery lead time and reduced production costs.
.jpg)
Figure 3.
Allomet made their choice after a number of process evaluation sessions at Harper’s Technology Research Center, where Harper’s experts supported the fine tuning of their carburization process. The results provided an optimized system design, and will provide an increase in output efficiency that supports Allomet’s continuing production volume growth while minimizing new capital investment. Harper’s expertise was recognized by Allomet in thermal process development across a range of material industries, and Harper’s knowledge in this area was a key factor for its selection as a partner. The new rotary furnace is developed to accommodate Allomet’s use of hydrogen, argon and methane atmospheres either alone or in combination.
The President of Allomet John Keane commented that as they look to considerably increase the production capacity to meet the growing global demand for the unique and highly wear-resistant Tough Coated Hard Powders (TCHP), they recognized that careful consideration and un-derstanding of thermal processing steps was needed. Harper offered superior technical proficiency in this area and then followed it up with a tailored furnace that optimizes our process and delivers efficiencies in multiple areas.
Allomet Corporation has been at the forefront of the nano-engineered powdered metal industry for almost a decade. Using its globally-patented high-technology processes and equipment, the company has successfully developed number of grades of unique, high-value commercial materials known as TCHPs, which are an entirely new class of industrial powders with long sought-after extreme strength and wear-resistance performance characteristics. High value uses of TCHP include cutting tools, wire dies, and surface coatings created via thermal spray or laser cladding.
About Harper International
Harper International is a global leader in complete thermal processing solutions, as well as technical services essential for the production of advanced materials.From concept to commercialization, from research scale to full production line operations, Harper is perpetually on the cutting edge. For decades, we have pioneered some of the world’s most innovative, customized systems, with a focus on processing materials at high temperatures and in non-ambient atmospheres.
Harper’s value proposition is unequaled — decades of industry experience, a highly specialized, multi-talented group of employees, and a passion for partnership. We don’t shoehorn a standard line of products to fit our customers’ requirements. We specialize in first-of-a-kind solutions using our exceptional depth and breadth of knowledge. Harper’s culture is one of genuine ingenuity and creativity, which ensures we are constantly challenging ourselves to craft the best-engineered technology solution for our customers’ unique thermal processing needs.
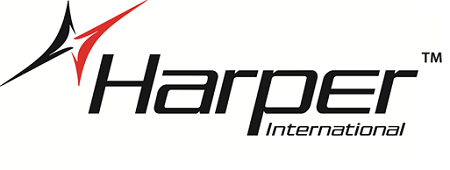
This information has been sourced, reviewed and adapted from materials provided by Harper International.
For more information on this source, please visit Harper International.