Recent developments in production processes, materials and delivery equipment have together created a dynamic environment in the drug delivery field. The successful introduction of new products and support of existing products demand new research and development parameters and protocols. For new drug delivery device development, gaining insights into all components and the performance of the device under different situations is essential.
Materials Testing and Characterization at Becton, Dickinson and Company
Sophisticated characterization and testing of materials are being performed by top medical device development firms at the product development stage to ascertain quality in design and mass production. As part of its efforts in new product development, Becton, Dickinson and Company (BD), a manufacturer and seller of medical devices, reagents and instrument systems, uses many different mechanical testing routines which are designed to help device design engineers make decisions, according to key staff members involved in research and development at BD.
The data acquired in the BD research and development laboratory streamlines the design cycle and helps the design for production process. Investments made in testing at this stage help the company to achieve quality in device production. Devices analyzed in the laboratory often have smaller footprint, with specimens typically having a size of smaller than 50 mm and are made of biodegradable plastic. Hence, it is highly significant to be able to carry out very small motions with a high level of precision owing to the characteristic of the devices being analyzed.
Zwick Solutions at Becton, Dickinson and Company
BD uses cutting edge test and measurement devices in its research and development laboratory, including those supplied by Zwick USA, a unit of Zwick/Roell. For more than 100 years, Zwick has been a key player in the development and fabrication of materials and component testing solutions for use in the medical industry. The testing solutions and software offered by Zwick are designed to fulfill the specific requirements of the medical packaging industry, including solutions for primary packaging such as testing of carpoules, vials, and pre-filled syringes, and solutions for secondary packaging such as peel testing on blister packages.
BD research and development laboratories carry out compression, tensile and some cycling tests for analyzing material interactions. Besides providing accuracy and facilitating convenience in the testing laboratory, the zwicki-Line system at BD delivers the versatility required to testing many different device characteristics, according to Zwick’s medical industry manager, Erik Berndt. Zwick’s proven testXpert II software is the reason behind such versatility. Programmability within testXpert II facilitates the configuration of new test routines and aids the analysis of ergonomic parameters.
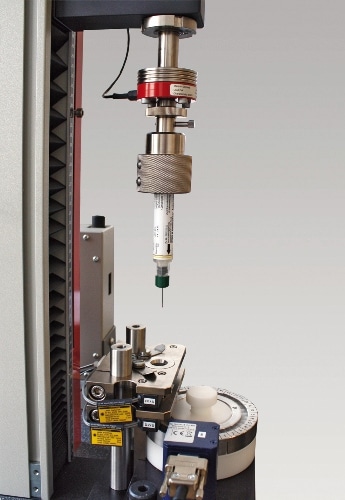
Figure 1. A zwicki-Line system engaged in characterization of an injection device. Specialized fixturing holds the specimen in position for a variety of different tests in accordance with customer requirements.
Sophistication in external signal processing allows the testXpert II measurement and control software to facilitate test procedure automation by feeding back the signals from external sensors in order to initiate the next step in the test flow. FDA traceability is highly significant to BD, which employs the innovative electronic recordkeeping functions of the testXpert II measurement and control software.
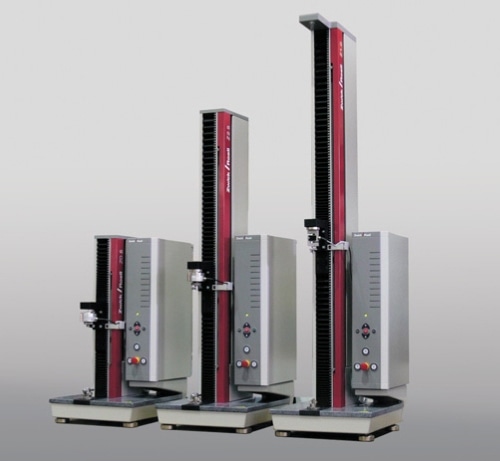
Figure 2. The suite of zwicki-Line systems balances accuracy in testing with a compact footprint to address customer needs for precise testing as well as conservation of benchtop space in the laboratory.
The manufacture of medical packaging and delivery products needs to be conformed to regulations such as Annex 11 of the EU GMP directive and FDA CFR Part 11 while utilizing electronic recordings and signatures in the regulated environment. Berndt informed that Zwick’s electronic records function provides tamper proof documentation of all measures and modifications carried out in testXpert II.
The user defines the level of measures to be recorded and validated as per the specifications. In a particular case, this could involve logging every parameter change relevant to testing. The capture of electronic signatures facilitates the statement of responsibility to be documented and enables the transition to a paperless laboratory at the same time, because of the possibility of replacing the signature on a document with a digital signature of the test series, informed Berndt.
Conclusion
The ability of the Zwick systems to store the entire test environment, which includes all software and hardware control factors and test conditions, optimizes test throughput and helps customer objectives in product development.
About Zwick
For over 150 years the name of Zwick Roell has stood for outstanding technical expertise, innovation, quality and reliability in materials and component testing. Our customers’ confidence in us is reflected in our position as world- leaders in static testing and the significant growth we are experiencing in fatigue strength testing systems. The figures tell the same story: in the 2011 the company achieved incoming orders of €185m.
With innovative product development, a comprehensive range and worldwide service, this family concern supplies tailor-made solutions for the most demanding research and development and quality assurance requirements in over 20 industries. With over 1100 employees, a production facility in Ulm, Germany, additional facilities in America and Asia plus agencies in 56 countries worldwide, the Zwick brand name guarantees the highest product and service quality.
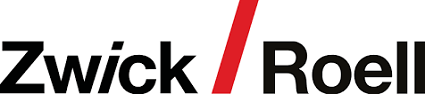
This information has been sourced, reviewed and adapted from materials provided by ZwickRoell GmbH Co. KG.
For more information on this source, please visit ZwickRoell GmbH Co. KG.