Bottom loading furnaces (BLF) are frequently used for huge, heavy samples requiring temperature uniformity throughout the heating process. Bottom load furnaces—also referred to as elevator furnaces—are obtainable in benchtop and production sizes and are divided into two parts. The main body of the furnace remains fixed, while the load platform, also known as the kiln car, is raised into position.
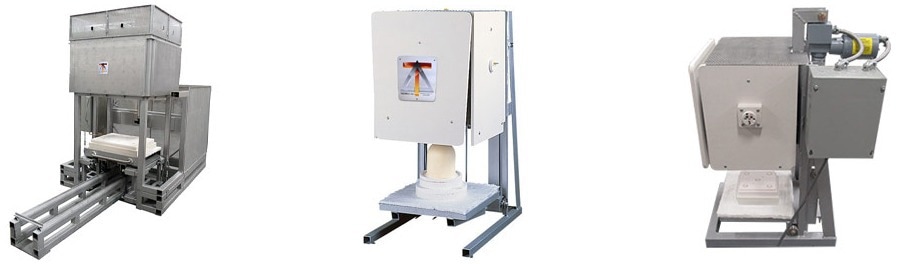
Bottom load furnaces. Image Credit: Deltech, Inc
Benefits of Bottom Loading Furnaces
The main advantages of BLF or elevator furnaces are:
- They can function effectively at high temperatures of up to 1800 ºC
- They can be designed and produced in a variety of sizes
- Effortless loading and unloading
- Uniform temperature due to heating on all four sides of the chamber
- High-quality products
- Rapid cooling
- Minimal heat loss
Deltech Bottom Loading Furnaces
Deltech Furnaces offers furnaces with octagonal, cubic, and square bottom loading workspaces and pneumatic or electric lift systems for easy loading. Deltech employs impact-resistant fiberboard for the furnace’s outside to assist convection cooling without fans. The fiberboard also keeps the furnace's exterior cool, improving operator safety.
Deltech offers “fast fire” options if the process necessitates faster ramp rates. This option increases ramp rates to as high as 1000 ºC per hour for both lab scale and production size bottom load furnaces.
The control systems used by Deltech Furnaces are UL508A and Intertek certified. Door interlocks, isolation switches, an emergency stop button, and a safety relay are standard safety features, but additional temperature and remote access controls are available.