Gas-fired furnaces can produce remarkably different products compared to electric-fired furnaces. An excellent option to scale up while replicating the conditions present in resistance-heated batch furnaces is to use a bespoke Deltech tunnel kiln.
Depending on the user's process parameters, a tunnel kiln might be preferable to a production size “top hat”, bottom loader, or front load furnace, while still maintaining the rapid heating and cooling and exceptional temperature uniformity characteristic of Deltech non-continuous furnaces.
The list of many additional features that can be added to the user’s custom-designed and build tunnel kiln is shown below.
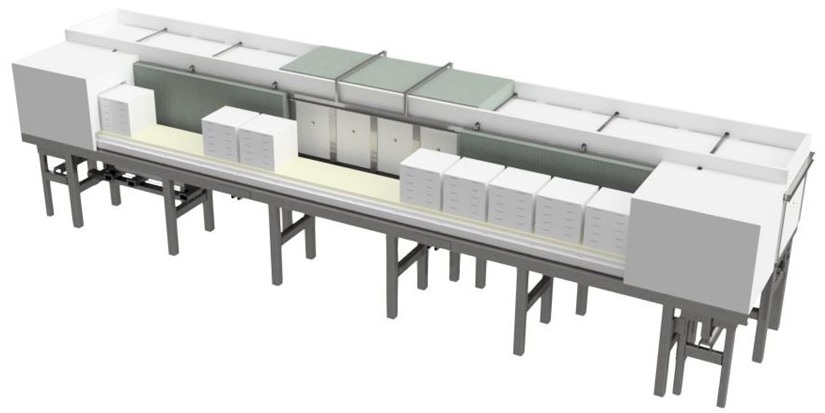
Tunnel Kilns. Image Credit: Deltech, Inc
Features
- Gas analysis and sampling in preheat and exit zones
- Single or multizone including preheat and cool down sections
- Integrated scales for measurement and data logging of material weight changes
- Sustained operating temperatures up to 1800 °C
- Control systems are certified by Intertek UL508A compliant
- Feeding options include screw conveyors, gravity feeds, and volumetric loading
- Control systems made to order, just like your new kiln. PLC/HMIs for speed control, weight data, control trends, and temperature data are examples of features. The user’s desired brand of temperature controller can be supplied and integrated
- Fiberboard or ceramic lined
- The ability to add additional length as product demand grows
- Gas curtains to protect the environment from materials outgassing
- All systems are built to comply with UL508A, CSA 22.2, and NFPA 86 standards
- Controlled atmosphere capability including gas mixing and delivery systems
Information Needed to Start the Design Process:
- Number of zones
- Product characteristics
- Any required controlled atmosphere capability
- Desired operating temperatures
- Product dwell time at the desired temperatures
- Workspace size
- Temperature requirements of individual zones