STACIS® III from TMC features sophisticated inertial vibration sensors, advanced piezoelectric actuators and state-of-the-art control algorithms.
This innovative active vibration cancellation system performs real-time vibration cancellation both through ongoing measurement of floor activity and filtering out of floor motion through expansion and contraction of piezoelectric actuators.
Key Features and Benefits
STACIS III comprises the DC-2020, a new and enhanced digital controller. This breakthrough control system also has a new dual-core processor and Ethernet and USB serial ports on its front and rear panels. The user-friendly, PC-based graphical user interface (GUI) is another key feature of the system.
With the unique serial design and proprietary high-force piezoelectric technology, the onset of vibration isolation takes place at 0.6 Hz, with 40% to 70% isolation achieved at 1 Hz. More than 90% isolation can be achieved at 2 Hz and higher, vertically and horizontally.
Besides minimizing fab floor construction expenses, STACIS III enables installing tools in higher vibration conditions. It has an active bandwidth of 0.6-150Hz and 6 degree-of-freedom active hard mount design without soft air suspension.
With many hundreds of successful installations worldwide, STACIS is the ideal vibration cancellation system for the most vibration-sensitive instruments. Scheduled re-tuning is not required as it is a robust control system. STACIS III is a point-of-use solution with compatibility to all internal tool vibration isolation systems.
Using TMC’s STACIS® technology, STACIS III performs vibration cancellation with piezoelectric actuators. By this way, it allows accommodating sophisticated tools in the older and noisier floors. It is compatible with different floor heights and sub-floor geometries in fabs.
STACIS III affirms compliance with tool vibration criteria during increasing vibration levels over time, thereby increasing throughput, yield and quality. TMC also offers RoHS-compliant version. STACIS is hundreds of times stiffer when compared to air isolators, thus eliminating all of the limitations of air vibration isolation systems.
Unlike active air systems, it is possible to place STACIS underneath a tool featuring an internal active air isolation system, thus optimizing both the systems. The worldwide installation of over hundreds of STACIS systems demonstrates that STACIS is the most suitable vibration cancellation system recommended by most tool manufacturers for the most vibration-sensitive instruments.
Specifications of STACIS® III System
The key performance specifications of the STACIS® III system are given in the following table:
Performance Specifications |
Active degrees of freedom |
6 |
Active bandwidth |
0.6 to 150 Hz |
Natural frequency |
Passive elastomer. 18 Hz
Effective active resonant frequency: 0.5 Hz |
Isolation at 1.0 Hz |
40% - 70% |
Isolation at 2.0 Hz and above |
90% or better |
Settling time after a 10 lb (4.5 kg) step input (10:1 reduction) |
0.3 sec |
Internal noise |
<0.1 nm RMS |
Operating load range per isolator (different passive mounts required) Isolator overload safety factor |
400 - 4,500 lb
(182 - 2,045 kg)
>2:1 |
Number of isolators |
3 or 4 typical |
Stiffness (1,000 lb/454 kg mass) (typical middle capacity isolator) |
40,000 lb/in.
(73 x106 Wm) |
Magnetic field emitted |
<0.02 micro -gauss broadband RMS |
The isolator dimensions, environmental and utility requirements are listed in the following table:
Isolator Dimensions, Environmental & Utility Requirements |
Isolator size |
11.75 in. (W) x 12.5 in. (D) x 10.8 in. (H)
(300 x 320 x 275 mm) |
Isolator weight |
75 lb (34 kg |
Controller size |
19 in. (w) x 8.5 in. (D) x 1.75 in. (H)
(483 x 381 x 44 mm) |
Temp., operating |
50° to -F90°F (10 to 32°C) |
Temp., storage |
-40° to 255°F (-40 to 125°C) |
Humidity, operating |
30- 60% |
Power required |
100, 120, 230 or 240 volts; 50/60 Hz; <600 watts, CE compliant |
Floor displacement |
<480 µ in. (12 µm) below 10 Hz |
Options: TMC laminated, stainless steel platforms, frames, "risers," leveling devices, earthquake restraints, and lifthoods |
The following table summarizes the key specifications of the DC-2020 controller:
DC -2020 Controller Specifications |
|
|
Physical dimensions |
1.75" (45 mm) H x 19' (483 mm) W x 8.5" (216 mm) D
RETMA rack mountable with optional brackets |
Weight |
6.3 lb. (2.9 kg) |
Processor |
Dual core processor 150/75 MHz |
Sampling rate |
10 KHz |
Analog outputs |
16 channels |
Analog inputs |
16 channels |
Status light |
Single LED |
Front panel ports |
Serial USB 2.0
Serial Micro USB
Ethernet RJ-45
2 BNC connectors |
Rear panel ports |
Ethernet RJ-45
Serial USB 2.0
RS -232 DB-9 legacy serial port (compatible with STACIS 2100) |
User interfaces |
Character menu on HyperTerminal
Extended GUI on Windows -Based PC
Embedded Ethernet GUI control pages |
Performance of STACIS® III System
The following graph shows the performance advantage of the STACIS® III system:
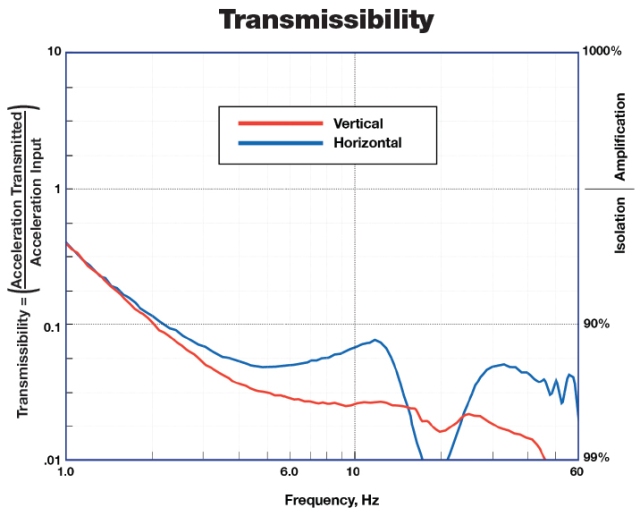
Key Applications
STACIS is originally designed for vibration cancellation in precision microlithography, inspection, and metrology instruments used in sophisticated semiconductor factories. The system has now become the industry standard solution for the highly sensitive equipment operating under noisy conditions, including:
- Semiconductor fabs
- Failure analysis labs
- Nanotechnology research
- Nanofabrication facilities
- Materials research
The STACIS® III Piezoelectric Active Vibration Cancellation System from TMC

STACIS® III (Piezoelectric Active Vibration Cancellation System)

STACIS® System on “risers” installed under a custom designed TMC Quiet Island® subfloor platform to support an eBeam lithography tool in a 36” tall raised floor.

A STACIS® System, incorporating a non-ferromagnetic, highly damped, aluminum platform, provides a second stage of vibration isolation for a Bruker BioSpin 600 MHz NMR Spectrometer. Photo courtesy of Bruker BioSpin and Memorial Sloan Kettering Cancer Center.

DC-2020 and PC-Bassed Graphical User Interface

STACIS® supporting the end chambers of a prototype LIGO interferometer at the California Institute of Technology. These are the most precise instruments ever made – capable of measuring distances of less than 10-18 meters.