The most recent generation of Instron's Autoinjector Testing System was created in close collaboration with CDMOs and pharmaceutical device manufacturers. It can conduct comprehensive functionality testing on various drug delivery devices, including safety syringes, button-activated devices, and needle shields.
Cap removal, dosage accuracy, activation force, injection duration, needle depth, click detection, and needle guard lockout are critical performance criteria this system evaluates. By doing so, laboratories can meet internal quality needs and international standards like ISO 11608.
Autoinjector Testing System | Semi-Automated System for Testing Pen and Autoinjectors to ISO 11608
Video Credit: Instron - USA
Get in touch now
All-In-One Solution
The Autoinjector Testing System substitutes conventional test methods, frequently calling for several pieces of equipment. This allows manufacturers to shorten the time to market by allowing users to execute a whole test sequence on a single system.
- Cutting down on the amount of time and devices needed to finish testing
- Spending less on specimens, maintenance, and testing apparatus
- Streamlining the processes of data consolidation, analysis, and validation
- Optimizing tech transfer to manufacturing sites

Image Credit: Instron - USA
Full Functionality Testing
Run a Complete Sequence of Tests on a Single System

Image Credit: Instron - USA
Activation Force
The system activates the device and determines the force necessary to commence injection.
Needle Depth
Images from the machine vision camera are taken at the injection's beginning and end.
Click Detection
A microphone confirms an audible click at injection activation and needle withdrawal.
Delivered Volume
The fluid that has been expelled is weighed using a precise scale.
Injection Time
A machine vision camera calculates the total time fluid in the field of view.
Needle Guard Lockout
The system loads the test device to a predetermined lockout force or until the defeat force is met.
Dedicated Test Methods
Autoinjector Testing System | Simple Test Methods
Video Credit: Instron - USA
Bluehill® Universal employs more accessible test types that allow users to quickly build and adjust method parameters while providing flexibility to incorporate future devices without requiring Instron's assistance. Users can select the appropriate functional tests (cap removal, injection, and needle shield safety check) and enter their parameters.
The system automatically executes the tests in the proper order, reducing test time and assuring consistency. The software has pre-loaded templates, allowing users to quickly and easily design a new device method and begin testing.
- Quick and easy to establish a new device technique and begin testing
- Improved uniformity in testing among operators
- Flexibility to change procedure parameters as needed
- Preloaded templates for two-step, three-step, and safety syringe devices
System Suitability Testing

Image Credit: Instron - USA
The Autoinjector Testing System incorporates system suitability testing into the testing process by automatically urging users to execute admin-defined daily checks on the load cell, machine vision camera, and scale in accordance with internal regulations and Good Manufacturing Practices.
Results are maintained in the system’s audit trail, making meeting FDA 21 CFR Part 11 and other accrediting body standards easier.
- Control over what is checked and how frequently.
- Capability to block system use until all system checks are completed
- Traceability is necessary to meet audit standards
- Easy-to-use hardware kit speeds up the evaluation procedure
Get in touch now
Advanced Camera Capabilities
Optical Measurements

Image Credit: Instron - USA
The autoinjector testing system includes a machine vision camera that measures injection time with high precision and detects exposed needle depth at the start and end of the injection.
Root Cause Analysis

Image Credit: Instron - USA
A high-resolution video camera and a machine vision camera give important visuals for successfully analyzing test findings, making it easier to discern whether a poor result was caused by a device failure or simply an error in the testing procedure.
Device Flexibility

Image Credit: Instron - USA
The autoinjector testing fixtures were intended to reduce side loading during cap removal, support typical industry device shapes, and provide flexibility to handle customized devices.
- Increased flexibility and efficiency for testing numerous device types
- Easily generate new inserts to suit future devices
- Decreased variability in test results
- Simplified alignment
Safer
Light Shield
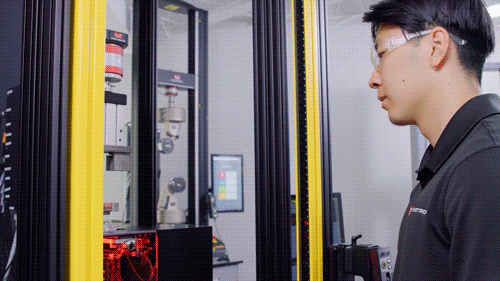
Image Credit: Instron - USA
The testing system is enclosed with debris shields on three sides and a light shield across the front that prohibits the machine from operating when the operator is physically present in the test room. A physical door can be added on the front to enclose the testing system.
Smart-Close Air Kit & E-Stop

Image Credit: Instron - USA
The pneumatic-powered upper and side grips use the 6800 Series smart-close air kit technology, which allows users to save preferred grip pressure settings in the test method and ensures consistency across tests. The air kit is fully incorporated with the system’s emergency stop, which causes the grips to disengage when the E-Stop is engaged.
Operator Protect

Image Credit: Instron - USA
The autoinjector testing system features Instron's patent-pending Operator Protect architecture. An intelligent process that maintains equipment and operator safety by monitoring system status from setup to test completion. The built-in safety coaching always gives clear visual feedback on system status.
Get in touch now
System Validation
Instron provides a comprehensive turnkey solution, including goods and services, to assist testing laboratories in expediting their in-house validation procedures and using their autoinjector testing system.
Traceability
Instron® | Traceability Module in Bluehill® Universal Software
Video Credit: Instron - USA
Bluehill Universal’s Traceability module helps users comply with audit regulations, such as FDA 21 CFR Part 11, ISO 17025, Nadcap, etc. This sophisticated add-on seamlessly integrates electronic approvals and an automated audit trail and works in tandem with Bluehill's built-in security to ensure unparalleled data traceability.
Centralized Lab Management
Bluehill® Central | Lab Management Software from Instron®
Video Credit: Instron - USA
By integrating Bluehill Central software, a laboratory management solution that provides centralized, remote management of Bluehill Universal software applications connected with various Instron test frames, users can manage tech transfer and make sure all sites employ verified test techniques.
Using this software, users can remotely manage all Bluehill Universal users, test templates, results, approvals for file revisions, and audit trail data from various Instron systems.
On-Site Calibrations

Image Credit: Instron - USA
Instron Professional Services provides on-site calibration for the Autoinjector Testing System, which includes tension and compression force, speed and displacement, and needle depth. These services verify that testing parameters are satisfied and that the findings are calculated correctly.
IQOQ Validation

Image Credit: Instron - USA
Software validation is essential for ensuring compliance with FDA 21 CFR Part 820, often known as the Quality System Regulation (QSR), and ISO 13485. Instron provides vendor Installation Qualification and Operational Qualification (IQOQ) documentation completed on-site by certified Instron Field Service Engineers.
This validation is meant to check that the Instron testing instrument has been properly installed, is appropriate for its intended use, and can produce accurate results. Instron's skilled Service team will employ their proven documentation pack, which includes the relevant IQOQ documents, reference files for calculation validation, and instructions.