PSL technology helps hundreds of pilot and production facilities worldwide manufacture their goods consistently and efficiently allowing them to bring their products to market more quickly every day. Pharmaceuticals, fine chemicals, and precious metals are just a few industries that use PSL Agitated Nutsche Filter Dryers (ANFD).
PSL's production scale ANFD filter dryers were designed to combine multiple processing steps within a single piece of equipment in demanding production settings. Solid-liquid separation is carried out, also known as filtration. Product washing occurs to remove impurities and/or solvent traces. The final steps are to dry and retrieve the collected solids.
PSL ANFD's contain an agitated vessel that can operate under pressure and vacuum. The vessel is constructed from Stainless Steel (316L or 304L) or Alloy 22. It also has a heated agitator and heated jacket for effective product mixing and drying.
Download the Brochure for More Information
Features and Benefits
Combined Filtration and Drying
Agitated Nutsche Filter Dryers from PSL offer a single piece of machinery that complies with Good Manufacturing Practices (GMP) for stringently controlled development and production processes. They enable manufacturers and process engineers to carry out wide-ranging processes using an all-in-one piece of equipment.
- Slurry filtration
- Product washing
- Re-slurry
- Vacuum drying
- Product sampling
- Product discharge
cGMP Compliance, Delivered
The strength of PSL is derived from an in-depth understanding of GMP regulations, practical experience, and familiarity with various production workflows.
PSL ANFD filter dryers offer the highest standards of quality and safety. They are produced to comply with various industry standards, including directives such as cGMP and GAMP, FDA regulations, ATEX guidelines, 21 CFR Part 11 rules, and initiatives like PAT.
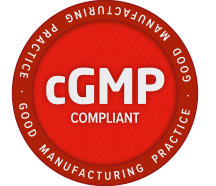
Image Credit: Powder Systems
Be Containment-Ready
For over 35 years PSL has gained the confidence of industry partners by providing well-engineered containment systems that safeguard their employees' health.
Containment technology is a necessary component of many industrial filtration and drying processes because it protects operatives from extremely dangerous substances and/or shields delicate products from hazardous production conditions.
PSL's high containment systems function in a negative pressure, HEPA-filtered atmosphere, guaranteeing operator protection. Worldwide, PSL isolators are used for processing highly potent substances in need of extremely low Occupational Exposure Limits (OELs), such as 20 ng/m3. These compounds may include hazardous cytotoxic substances or High Potency Active Pharmaceutical Ingredients (HPAPI) for example.
The containment solutions can be rigid or flexible/disposable, depending on the specific demands of the business. PSL gloveboxes can be manufactured to comply with industry practices and achieve containment performances against SMEPAC Guidelines.
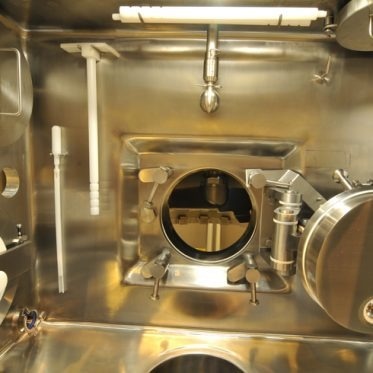
Image Credit: Powder Systems
Predictive Scale-Up
PSL is aware that scaling up the process and guaranteeing final production success depends on the choice of processing technology.
Our well-established filtration and drying solutions are widely acknowledged for their ability to expedite even the most intricate process developments for scale-ups, ranging from early R&D to GLP batches, pilot plants, and eventually GMP commercial production.
With the help of the filter-dryer portfolio, users will be able to carry out both scale-up and scale-down studies while maintaining the important process objectives (like batch uniformity, product quality, and yield) and production parameters (like filtering time, washing time, and drying time) at every scale.
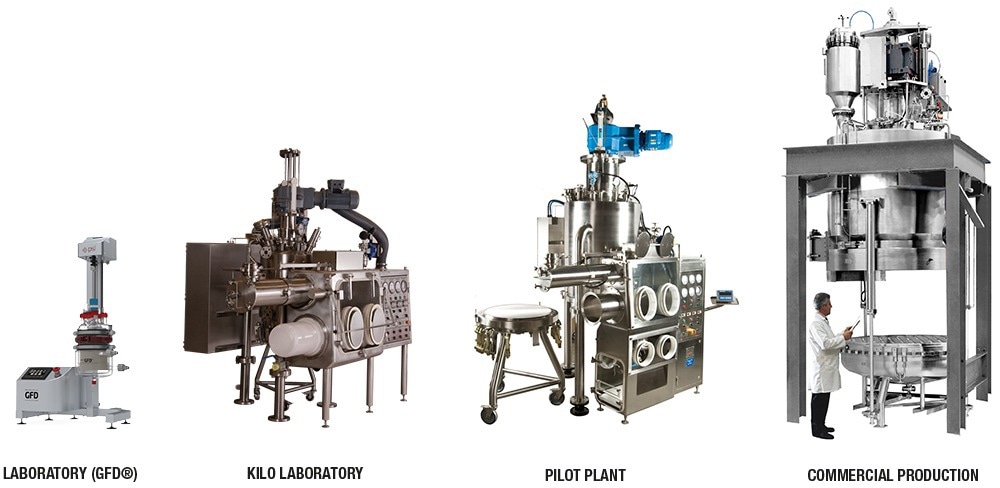
Image Credit: Powder Systems
Maximizing the Competitiveness
We know how precious the end product is and how important it is for the users to maximize production yield to maintain market competitiveness. This essential requirement was considered when designing the basic characteristics of filter dryers.
The product can be easily recovered from a PSL nutsche filter dryer by using the PSL agitator to automate the discharge process. The remaining portion of the batch, commonly known as product heel, can then be recovered using the "Direct Heel Recovery" technique that PSL introduced to the market several decades ago.
This process involves manually raking the product heel into a PSL high containment off-loading glovebox (ergonomically designed and integrated by PSL), resulting in efficient high-yield productivity. This guarantees a complete product recovery by keeping users, products, and the environment safe.
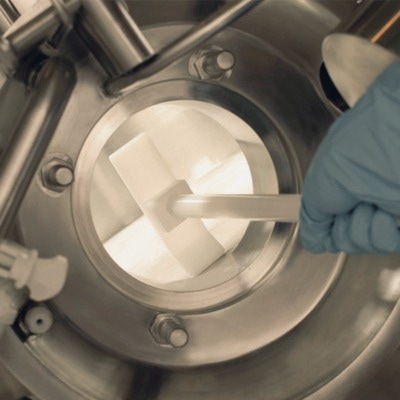
Image Credit: Powder Systems
Download the Brochure for More Information
Technical Overview
Vessel Sizes
Source: Powder Systems
.V |
. |
. |
. |
. |
. |
Filtration Area |
0.05 m2 |
0.125 m2 |
0.3 m2 |
0.6 m2 |
1.0 m2 |
Filter Cake Volume Range |
1 - 10 L |
2.5 - 37 L |
6 - 120 L |
12 - 240 L |
50 - 400 L |
Filter Cake Height Range |
20 - 150 mm |
20- 300 mm |
20 - 400 mm |
20 - 400 mm |
50 - 400 mm |
Max Liquid Volume |
20 L |
100 L |
270 L |
600 L |
1000 L |
Industry Applications
Source: Powder Systems
Industries |
Production Scale |
Processes |
Product Form |
Ingredients |
Pharmaceuticals |
Process optimization |
Filtration |
Suspension |
API drugs |
Chemicals |
Pilot development |
Separation |
Slurry |
Intermediates |
Food |
Pre-clinical & clinical |
De-watering |
Wet cake |
Raw materials |
Material sciences |
GMP batch |
Re-slurry |
Powder |
Excipients |
Synthesis |
Commercial production |
Washing |
Semi-solids |
Reagents |
Special processes |
|
Mixing |
|
Catalysts |
|
|
Sampling |
|
Precious metals |
|
|
Drying |
|
Graphene, Lithium |
|
|
Discharge |
|
|