By Surbhi JainReviewed by Susha Cheriyedath, M.Sc.Apr 21 2022
In an article recently published in the journal Additive Manufacturing, researchers estimated the warping in robotic 3D-printed continuous fiber-reinforced composites.
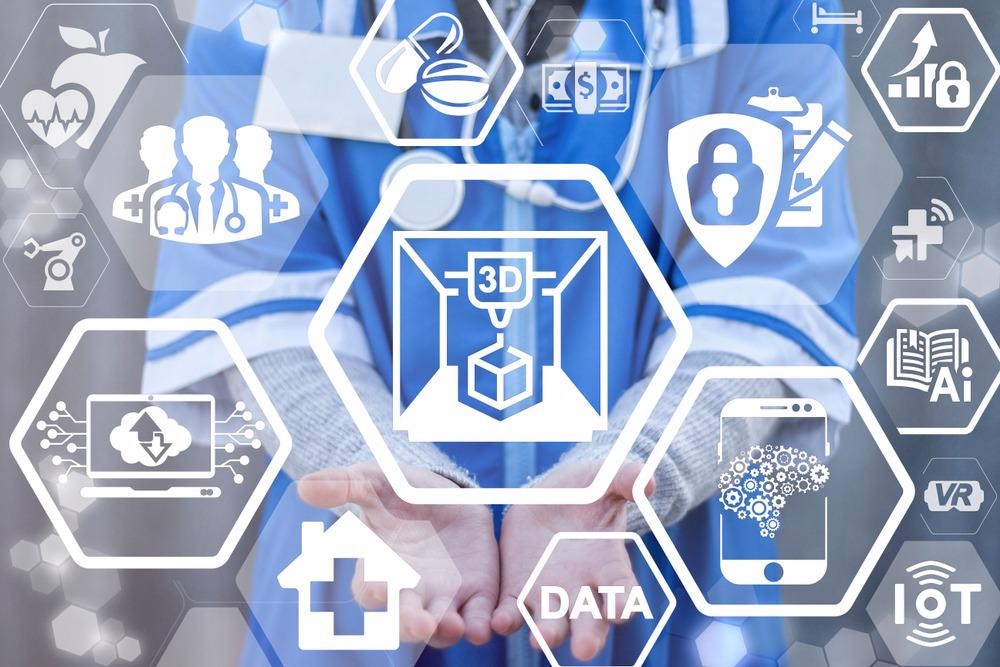
Study: Warping estimation of continuous fiber-reinforced composites made by robotic 3D printing. Additive Manufacturing 102796 (2022). https://www.sciencedirect.com/science/article/abs/pii/S221486042200197X
Background
Material extrusion (MEX) technology is a 3D printing technique that uses a nozzle or aperture to disperse material selectively. Continuous fiber 3D printing has been marketed by a rising number of companies that offer a diverse range of materials, part sizes, techniques, and production quantities. The mechanical performance and geometrical dimensions of the finished products are affected by the production design and process parameters such as bed temperature, nozzle temperature, and printing speed.
Despite the fact that the design of the experiment (DoE) could reduce the number of experimental trials required to determine the best 3D printing design and process parameters, time, significant cost, and many materials are still involved, particularly for high-performance, high-temperature, composite 3D printing.
As a result, simulation is an intriguing method for avoiding the burdens and costs involved with experimentation. Numerous efforts have been made to establish an accurate and reliable model of 3D printing of composite materials through modeling and simulation. There is currently no simulation for the thermal fields in the robotic and 3D-printed continuous fiber composites. Also, there is no model that estimates the wrapping of the final object. The proper generalized decomposition (PGD) approach has been applied to a variety of composite material manufacturing processes with great success.
About the Study
In this study, the authors discussed the modeling effort, as well as wrapping and deformation estimation during 3D printing. A thermal simulation was conducted followed by the use of the thermal results to run a deformation simulation using correct generalized decomposition.
A handheld laser scanner was used to build a 3D model and final shape for a tensile specimen that was manufactured according to ASTM D3039-17 with a changed width. The effects of the build platform temperature, nozzle temperature, and 3D-printing speed on the maximum deformation of the part were examined.
The researchers used combined thermo-mechanical deformation and experimental validation to describe the 3D printing of continuous fiber composite materials created by robotic 3D printing. To create items from continuous carbon fibers reinforced with PEEK, a robotic 3D printer was constructed with a custom-built head. Composite material for design applications was evaluated, and tensile properties were measured.
A tensile specimen was designed and 3D printed with a modified breadth in accordance with ASTM D3039-17. Experimental data were used to simulate and evaluate the final shape. The material details, tensile specimen measurements, and robotic 3D-printing technique were described.
More from AZoM: What is Femtosecond Laser-Based 3D Printing?
The team explained the experimental materials and methods employed, as well as the modeling methodology used in the problem simulation. The experimental and simulation results were compared and contrasted. To reduce computing time while providing accurate results, the PGD in-plane-out-of-plane decomposition was adopted.
In addition, Tenax®-E TPUD PEEK-HTS45 robotic 3D printing was used to create a tensile specimen with a changed width and 0o fiber orientation, as per ASTM D3039-17. A handheld laser scanner was used to scan the specimen and build a 3D model of the 3D-printed part. Moreover, the impact of 3D printing process parameters such as nozzle temperature, build platform temperature, and 3D printing speed was evaluated after validating the numerical model.
Observations
The difference in deformation at the part margins between numerical and experimental data was less than 11.2%. Because the first deposition did not reheat any substrate, simulations were necessary for five prepeg tapes per layer across five layers. The deposited prepreg's dimensions were 300 x 6.35 x 0.14 mm3. Each deposition had a width of 3 x 6.355 mm. The specimen's final thickness varied between 0.639 and 1.014 mm, but the material datasheet specified a nominal thickness of 0.7 mm, or 5 x 0.14 mm.
The modeling effort, which used a simple static per-layer technique, culminated in a nonlinear thermomechanical coupled problem with transient thermal simulation and mechanical deformation. As a result, the modeling was quick and simple to use, and accurately duplicated the deformation of the final 3D-printed object. When the numerical and experimental findings were compared, it was discovered that the relative error in the deformation at the part's edges was less than 11.2%. The maximum deformation and residual thermal stresses decreased when the build platform and nozzle temperatures were raised, whereas the deformation enhanced as the 3D-printing speed was increased.
Conclusions
In conclusion, this study elucidated the deformation of continuous fiber-reinforced composite parts generated by robotic 3D printing.
The authors observed that voids in continuous fiber-reinforced composites had a substantial impact on their performance, and 3D printing a part with a low void content was found to be difficult. They also mentioned that the numerical model used in this study will be expanded upon in a future study to estimate the void content of 3D-printed parts.
Disclaimer: The views expressed here are those of the author expressed in their private capacity and do not necessarily represent the views of AZoM.com Limited T/A AZoNetwork the owner and operator of this website. This disclaimer forms part of the Terms and conditions of use of this website.
Source:
Luca, P. D., Macario, A., Siciliano, C., et al. Warping estimation of continuous fiber-reinforced composites made by robotic 3D printing. Additive Manufacturing 102796 (2022). https://www.sciencedirect.com/science/article/abs/pii/S221486042200197X