Zwick Roell, a leading supplier of test equipment to the fibre composite industry, has introduced the hydraulic composites compression fixture (HCCF), which improves specimen handling, enables different specimen geometries to be tested and guarantees reproducible results due to exact alignment.
Found to deliver good results following tests carried out by a major European aircraft manufacturer in 2010, the HCCF was developed and patented by IMA Materialforschung und Anwendungstechnik GmbH in Dresden, Germany. It is produced and marketed by Zwick.
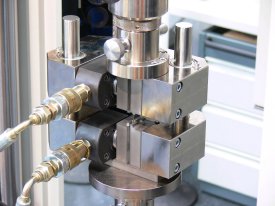
The compression test is one of the most important tests performed on carbon-fibre composite materials. However, it can be a challenging test to perform accurately because introducing the load to the specimen is problematic and flexure and stress peaks can easily lead to erroneous test results.
The new HCCF from Zwick eliminates these problems and gives better control during tests. It enables shorter testing times, avoids errors and is very flexible, allowing different shapes of specimens to be tested. Compliant with the important Airbus AITM 1-0008 industry standard, the HCCF can also be used for notch compression tests (OHC, FHC) to AITM 1-0008. Versions that can be used at temperatures of between -60 °C and +150 °C are also available.
Zwick has also updated its testXpert II software to include an expanded range of standard test programs for the composites industry. As well as producing suitable testing machines and fixtures, the company can now supply more than 40 standard test programs for composites. Test programs are available for all established types of test (such as tensile, compression, interlaminar shear strength, flexure, shear etc.) and all standards (such as ISO, EN, ASTM, Airbus AITM, Boeing BSS).