Ulrich medical (Ulm, Germany) uses a Zwick GmbH servo-hydraulic fatigue testing machine for both quality control and development of its spinal column implant systems. These implants are designed using the latest bio-mechanical , clinical and computer simulation data to provide durable spinal support for the patient. Because of the implant location in the spine it is critical they are fully quality tested prior to use.
The Zwick Amsler HC25 servo-hydraulic testing machine provides the manufacturer with the ability to perform a range of rigorous fatigue tests on implants to ensure reliability and strength. The testing process is made much more straightforward by the flexible testXpert II research software and the new testControl II control electronics provided with the Amsler HC25.
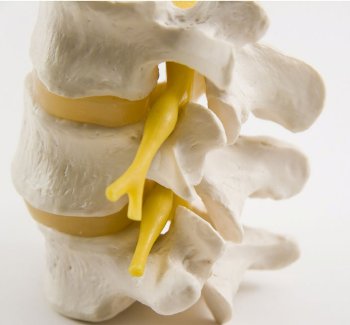
testXpert II provides an intuitive user interface, and makes cross-format data exchange simple as it is compatible with NI Diadem, ASCII and Excel formats. Importantly, testControl II offers high-frequency (up to 400 Hz) high-speed testing regardless of the number of measurement channels.
Typically, Ulrich medical uses the versatile Zwick Amsler HC25 to perform a range of essential tests on implants including: quasi-static, oscillating, pulsating compression and shear tests to provide a simple simulation of the everyday dynamic stress to which the implant is subjected in the spine. Such tests are performed regularly during the development process to ensure the quality and utility of Ulrich implants. More complex tests can be also be performed. For example, a torsion device may be used to apply a multi-axial static or oscillating load to the implant in superimposed torsion loading to apply stress in different areas of the spine and simulate the effects of posture changes.