Deben, a leading provider of in situ testing stages together with innovative accessories and components for electron microscopy, reports on how TU Dortmund University is using their CT5000TEC compression/tensile stage to study fiber-reinforced composites. This work is being performed using a Nikon X-ray source
Ronja Scholz is a scientific assistant and PhD student in the group of Prof. Dr. Frank Walther, Head of the Department of Materials Test Engineering (WPT) at TU Dortmund University. She specialises in the use of computed tomography (CT) to characterise composite materials contributing to the scientific and industrial research projects. These deal with investigations concerning metals, additively manufactured materials and composites using modern measurement and inspection processes, supported by optimized analysis and evaluation techniques. WPT provides the database for construction and production as well as for virtual development of reliable high-performance products for different industries and is used for decision-making guidance for material selection, quality control, component monitoring and damage analysis. This is facilitated by determining the chemical composition, analyzing microstructural properties with light, electron beams and X-rays, determining material properties and characteristic values by means of destructive (DT) and non-destructive testing (NDT) methods.
Ms. Scholz describes her work applying CT. “Our investigations provide microstructural information of a material as a non-destructive testing technique. The ability to look inside a specimen or component and getting 3D volume information, which can be characterized concerning different structural issues like defect volume, fiber orientation or wall thickness, expanded the test technology of our department in a very efficient way. Thus, to really understand the interdependencies between microstructure, mechanical loading and climatic implied processes in materials as accurate as possible, in situ investigations are of great importance. Therefore, the use of the Deben's CT5000TEC stage in combination with Nikon XT H 160 kV microfocus X-ray source enables the capture of the current state of a material in situ under mechanical tensile or compression loads up to 5 kN and variable temperatures in the range of -20 °C to +160 °C, see Figure 1. These measurements give essential information about defects such as pores or delaminations in the material’s initial condition as well as the progression and development of these defects under mechanical loading. This strategy allows the evaluation of different process routes for the manufacturing of a material allowing the study of the resulting microstructure as well as the performance of the material or component under application-oriented conditions such as elevated temperatures. When comparing CT scans of a damaged composite specimen, the in situ scan results reveal significantly more damage than the results of a conventionally performed scan. Figure 2a visualizes the damage development in a fiber-reinforced plastic. This material shows great potential as a substitute material for metals in automotive and aero applications providing economic efficiency thanks to their high specific strength. To gather sufficient information about the load capacity, damage development and the use of composites under changing environmental conditions, detailed investigations are necessary. In Figure 2b, the development of the defect volume due to increasing tensile load is shown for a cellulose-based composite, which shall be utilized as resource-efficient construction material. These results generated at room temperature can now be correlated with investigations at elevated or degraded temperatures, depending on the area of application.”
“Lastly, it is important to note that before using the integrable Deben CT5000TEC stage, we focused on conventional CT investigations, where specimens are scanned while resting (no load applied) to characterize their specific structure, e.g. fiber orientation, pore content, wall thicknesses, etc. Now our experiments produce data that is much realistic to the in-life use of these exciting, new composite materials.”
To obtain full details of the Deben applications and product portfolio, please visit www.deben.co.uk.
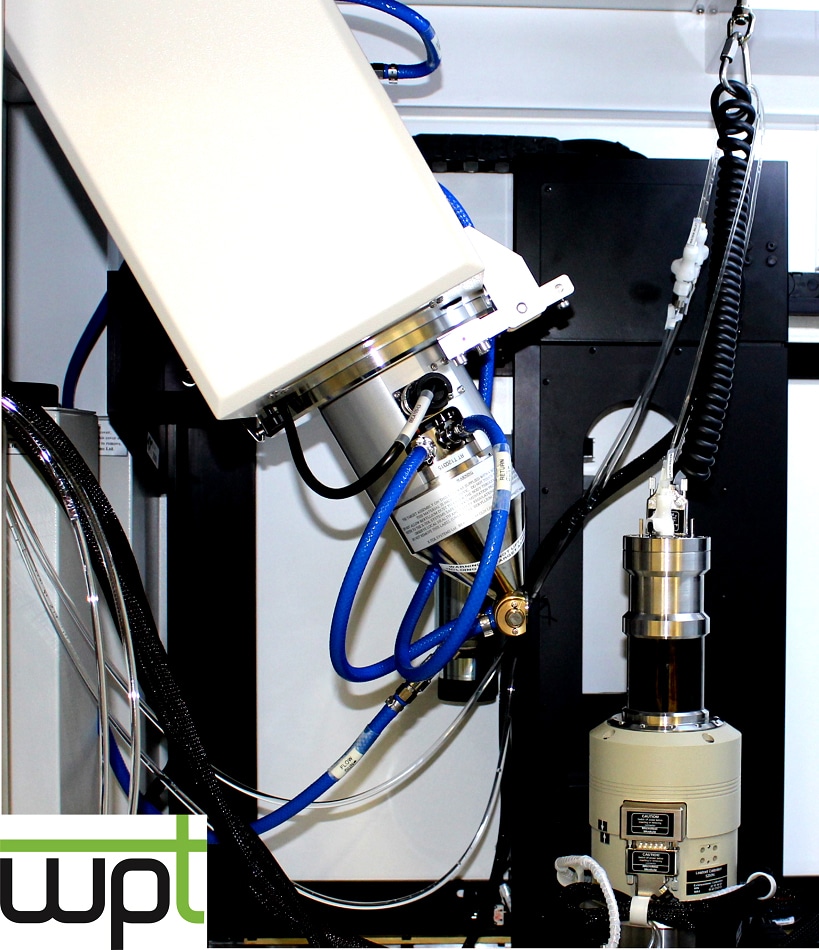
The CT5000TEC (Deben) mounted in a X TH 160 device (Nikon).
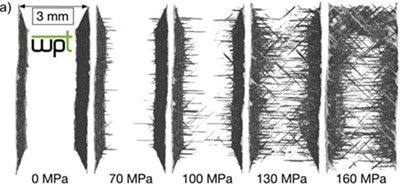
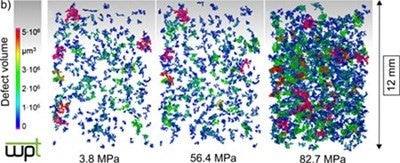
Figure 2:
a) Visualization of stress induced fatigue (tension-tension) damage development in a fiber-reinforced plastic specimen; b) Development of defect volume in a resource-efficient composite material under increasing tension load
References
Tenkamp, J.; Koch, A.; Knorre, S.; Krupp, U.; Michels, W.; Walther, F.: Defect-correlated fatigue assessment of A356-T6 aluminum cast alloy using computed tomography based Kitagawa-Takahashi diagrams. International Journal of Fatigue 108 (2018) 25-34.
Goerlich, P.; Scholz, R.; Walther, F.: Micro-CT defect analysis and hardness distribution of flat-face extruded EN AW606 aluminium chips. Materials Testing 59, 7-8 (2017) 613-617.
Siddique, S.; Imran, M.; Rauer, M.; Kaloudis, M.; Wycisk, E.; Emmelmann, C.; Walther, F.: Computed tomography for characterization of fatigue performance of selective laser melted parts. Materials & Design 83 (2015) 661-669.
A collective list of the publications can be reviewed under: http://wpt.mb.tu-dortmund.de/cms/de/forschung/publikationen/index.php