e-Xstream engineering has announced the release of Digimat 2019.0 the technology leading polymer simulation software. This version brings a series of enhancements to support the design and manufacture of innovative composite materials and parts, with improved accuracy, new materials systems, and greater efficiency in time taken and therefore cost savings.
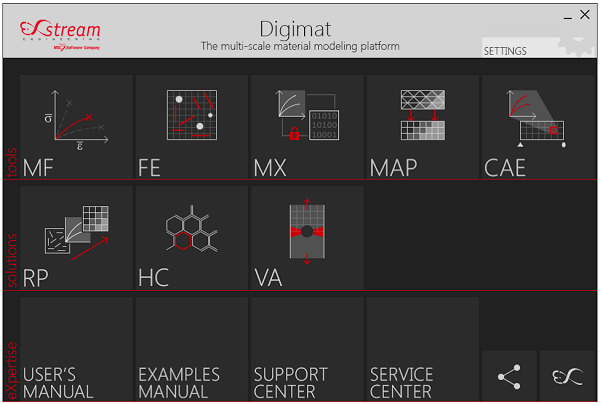
Democratization of High Fidelity Crash Simulations
It allows for the democratization of high fidelity crash simulations for reinforced plastic parts and also includes a strong interface to MaterialCenter now, a leading enterprise material data management solution.
Democratizing high fidelity failure & crash simulation of reinforced plastic parts: This type of simulation is required for confident design of lightweight components made of reinforced plastics. Access to material microstructure information is now made easier in the early design stage thanks to the capability to predict weld line location in addition to a new fiber orientation distribution. Time and complexity associated to the creation of a crash material model creation is drastically reduced with a new strain-rate dependent calibration procedure.
Lifetime Prediction of Reinforced Plastics Parts
New solution for lifetime prediction of reinforced plastics parts: In partnership with DSM, a state-of-the-art workflow for constant amplitude loading fatigue analysis of reinforced plastic parts is introduced – starting from efficient material model characterization up to dedicated fatigue post-processing capabilities in Digimat-RP. The solution is complemented by fatigue data available in the Digimat-MX database.
Tim Vorage, Dutch State Mines (DSM) Global Market Development Manager for Tii® PA4T, commented on this capability: “The automotive industry is looking for light weighting opportunities for various reasons like; function integration, NVH optimization, cost optimization and to reduce CO2 emissions, built-in safety and infotainment systems, or increase driving range for battery driven vehicles.
Predictability of Part Performance
Another trend is that designers and engineers are facing shorter design cycles, meaning that computer-based designs, predictability of part performance and 3D prototyping are key for metal replacement programs. Our close cooperation with e-Xstream is addressing these key needs and allows us to bring predictability of part performance directly to our industry partners with innovative engineering plastics such as ForTii® Ace MX53T (PA4T GF50).”
Integrative simulation for fiber reinforced polymer additive manufacturing: The Additive Manufacturing industry for polymers is entering the production era thanks to high performance fiber reinforced materials. To unleash their full potential Digimat 2019.0 provides both process simulation capabilities for warpage prediction and mitigation as well as as-manufactured part performance capabilities, enabling performance optimization as a function of the material and the manufacturing.
Furthermore, fiber reinforced material models are readily available inside Digimat-MX for material systems from DSM, Solvay Specialty Polymers and Stratasys Inc. “Our growing range of AM filaments underscores Solvay’s determination to establish itself as an industry leader in this rapidly evolving market,” says Christophe Schramm, Additive Manufacturing business manager in Solvay’s Specialty Polymers global business unit. “Digimat®-AM allows customers to simulate the printing process and successfully predict the thermomechanical behavior of 3D-printed designs in order to ‘print right the first time’,” he added.
Modeling of foam materials: Foam materials have unique combinations of stiffness and density. Enabling end users to control the microstructure and tailor the material properties to their requirements. This release introduces this material family into Digimat’s material engineering capabilities to complement the already wide range of materials, including polymers, composites, ceramics and metals.
Management of composite physical and virtual data at the enterprise level: Digimat-VA and MaterialCenter are now strongly interfaced in the 2019.0 release to enable an entreprise wide management of virtual and physical test results. Ply properties stored in MaterialCenter can be used as input for virtual allowable campaigns, while virtual test results can be stored, shared and managed in MaterialCenter, along with the available physical data.
Increase in Content of Digimat’s Advanced Material Database: Access to advanced material data is key to achieving high fidelity structural analysis and process simulation, whether for injection molding or additive manufacturing applications. Digimat-MX database provides direct access to validated off-the-shelf material models from a wide range of material suppliers. This new release further strengthens the content of its market leading public database. Two new material suppliers are added: Borealis and SUMIKA Polymer Compounds. New material systems and models are included from Asahi-Kasei Corporation, DSM, DuPont Performance Materials, Kuraracy Co. Ltd., SABIC, SOLVAY Engineering Plastics, SOLVAY Specialty Polymers and Stratsys Inc. Overall 68 new material systems have been added, corresponding to 15,871 new models, including fatigue data.
Roger Assaker, CEO of e-Xstream engineering and Chief Materials Strategist at MSC Software notes that; “This is another strong release of Digimat that helps our customers make an optimal use of materials for effective and efficient design of high-performance products. This is just the first release of a long series to leverage the interaction of Digimat with MaterialCenter in order to provide an enterprise-wide ICME solution to our customers across all industries.”