Adaptive3D today announced the first shipment of a Carima DM400A in North America. The large vat top-down DLP® 3D printing machine was delivered to a leading health system in the US. It is anticipated that it will be used to process Adaptive3D’s high-performance elastomer products, Elastic ToughRubber™ and Soft ToughRubber, for medical applications.
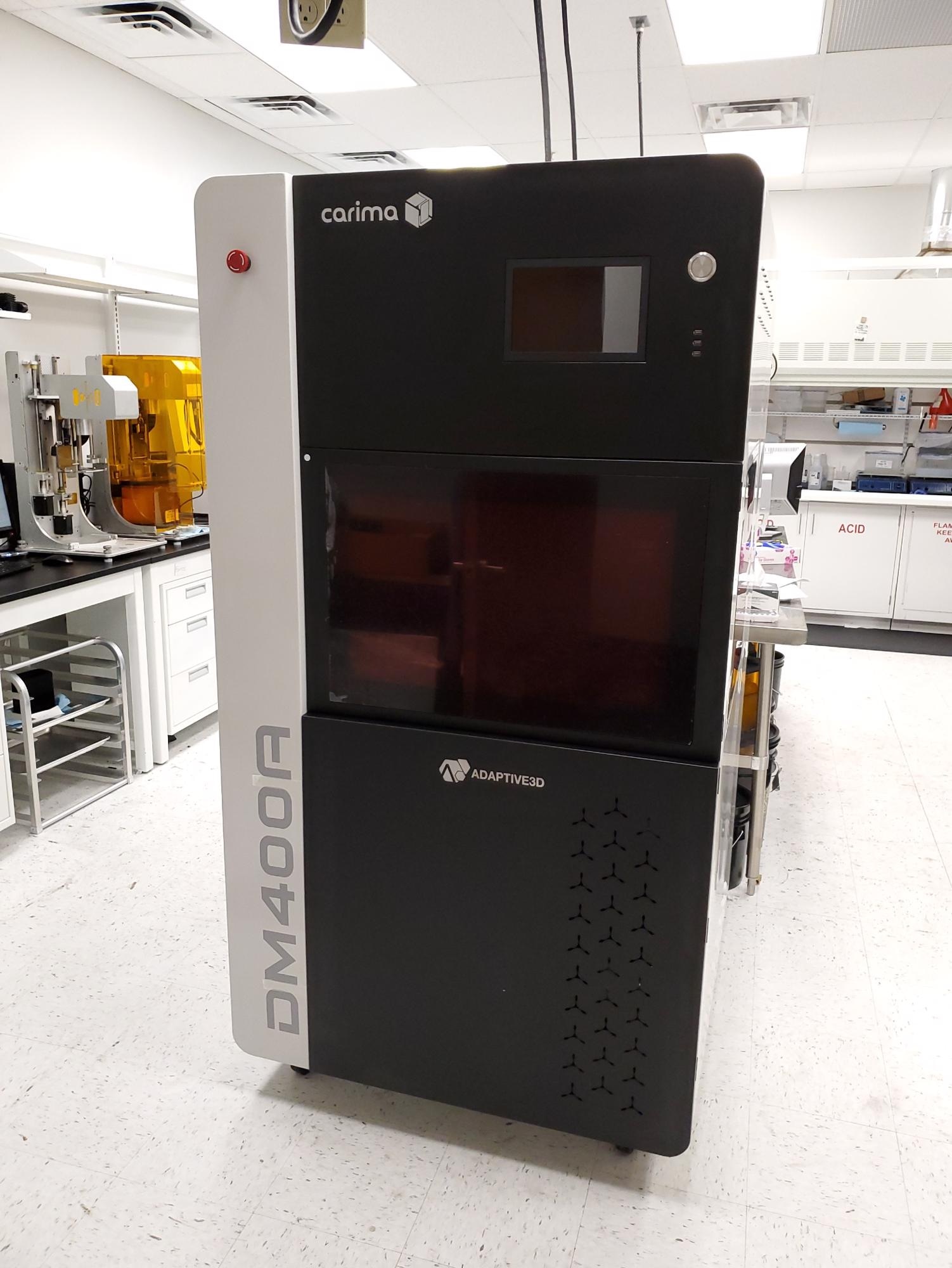
Image Credit: Adaptive3D
The Carima DM400A represents a revolutionary departure from standard bottom DLP 3D printers in that it configures the dual 2K ultra HD light engines at the top facing downward toward the print area, reminiscent of large vat SLA 3d printers. It is widely accepted that a major challenge to higher volume additive manufacturing using DLP® is overcoming separation forces experienced during a print. By returning to a more scalable top-down setup, Carima has elegantly overcome this significant barrier to higher volume printing: fighting gravity and separation forces.
“As the leader in additive manufacturing elastomers, we believe that top-down DLP is the optimal platform for processing this class of photopolymers for larger parts or larger batch sizes, higher throughput and lower cost,” said VP Sales & Marketing Kial Gramley. He went on to say that “with a build envelope of 400mm × 330mm × 500mm, the Carima DM400A delivers part and batch sizes more than 10× of the highest throughput bottom-up DLP systems that the competition has to offer.”
Adaptive3D sells photopolymer resins to enable the additive manufacturing of tough, strain-tolerant, tear-resistant rubbers, such as its flagship resin product, Elastic ToughRubber 90™: a tough, printable elastomer for all seasons. Adaptive3D printable photo-resins are optimized for high-throughput manufacturing of functional complex 3D plastic and rubber parts in consumer, healthcare, industrial, transportation and oil and gas markets.