The application of Additive Manufacturing (AM) in the field of biocompatible material manufacturing has truly been beneficial in increasing the biomechanical performance of the end products, as expanded upon in new research in the MDPI journal Polymers.
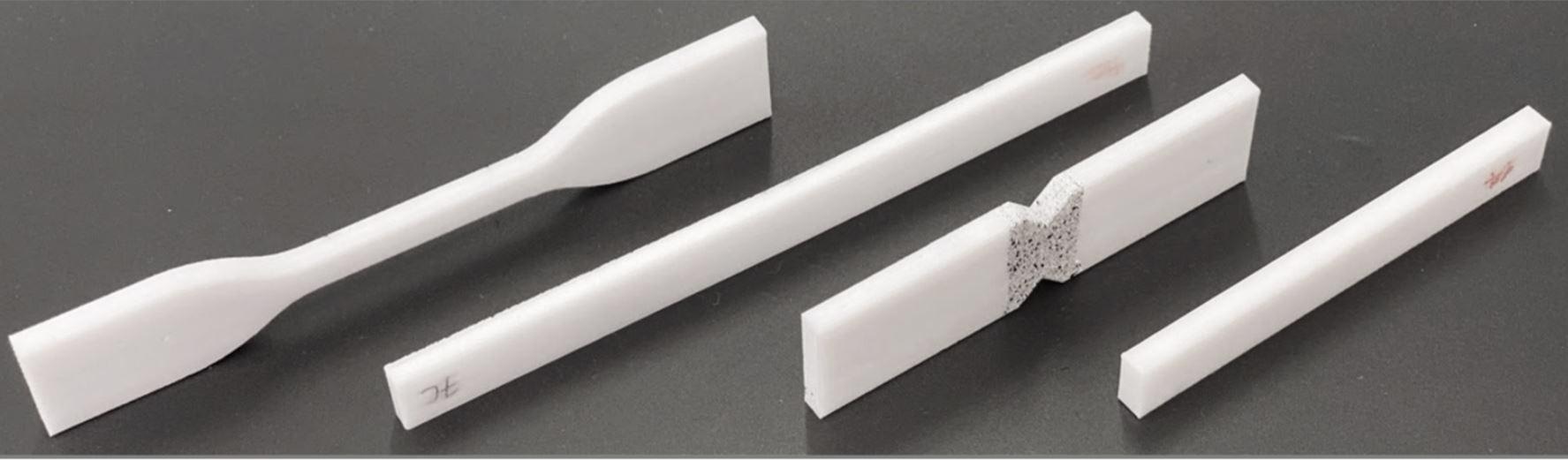
Test specimens’ designs, with dimensions according to the corresponding ASTM standards for each characterisation test. From left to right: tensile testing (ASTM D638), flexural testing (ASTM D790), shear testing (ASTM D5379), fatigue and impact testing (ASTM D7774 and ISO 179-1).
AM now enables the replacement or reinforcement of bones as well as prosthetic limbs through synthetic geometrical imitation. The multilayered sequential deposition of carbonate during the process ensures structural integrity, superior mechanical properties, increased lifetime as well as imitation of the natural bone porosity, making it highly suitable for the biomechanical field.
Polycarbonate and Its Properties
The ISO 10993 certified polycarbonate (PC) is a thermoplastic material with high geometrical complexity conveniently sterilized by gamma rays and ethylene oxide. The high-grade engineering polymer is tough and has high fatigue strength along with heat and chemical resistance.
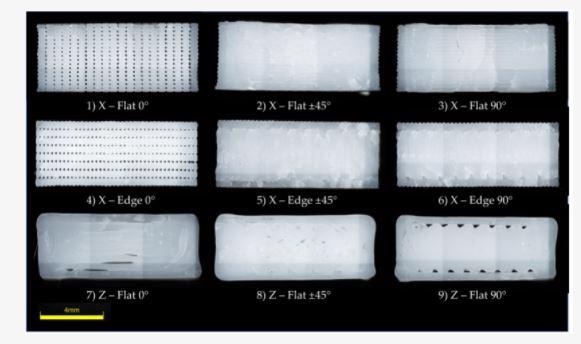
Transversal cross-sections of X-Flat, X-Edge, and Z-Flat samples. Image Credit: Gras, G. G, Polymers.
Thus, it is widely utilized for various medical applications such as sterilization, renal dialysis, surgical instrument manufacturing, and cardiac surgery products. These distinct advantageous properties have been motivating researchers to focus on their extensive utilization in the medical field, and the latest study by Marco A. Perez and his team has successfully analyzed the properties of 3D-printed PCs for biomedical functionalities.
Tests and Methods
The latest study involves extensive tests such as impact tests, shear, fatigue testing, tensile testing, and flexural testing to accurately assess all the relevant mechanical properties. Since the printing mechanism is essential for fiber orientation in the material polymer building resin, two distinct printing orientations, the Z-Flat and Z-Edge, were utilized and Z-Flat (ZX configurations) studied.
Three hundred and twenty-two samples were tested with well-documented standard test procedures and testing equipment such as using the Zwick 30kN equipment. The tests carefully followed the standardized ASTM D638 testing protocol. Such a uniform approach towards testing and evaluation is essential for accurate results and performance analysis.
Tensile and Flexural Performance Analysis
The performance of the polymer was carefully assessed, keeping in view the results of each test individually to have a clear idea of the properties and performance of the polymer. The performance of the Z-axis manufactured samples proved to be the worst. These samples consume the most amount of time to print.
However, the overall results of tensile moduli are very close to the reference value of the modulus (2000 MPa), showing properties of orthotropic stiffness.
The lower strength values of Z-axis printed polymers depict the weak point of vertical polymer manufacturing. The flexural performance was not affected by the variation of printing orientation or direction and is well within the limit of the reference value of 2100 MPa. However, Z-axis samples experienced fractures occurring between various layers.
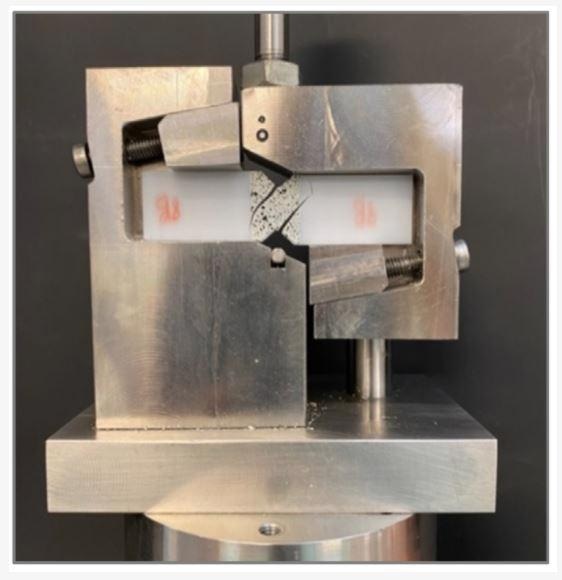
Experimental setup for ASTM D5379 shear test standard with digital image correlation equipment. Image Credit: Gras, G. G, Polymers.
The X-axis samples' strength performance was lowest for 90-degree filament orientation. The performance analysis clearly showed that if the filament is in the direction of tensioned fibber (angle is 0 degrees), maximum strength and resilience are displayed by the polymer.
Impact and Fatigue Performance Assessment
The Charpy test was selected for impact performance assessment, and like the tensile test, the Z-axis samples had the lowest toughness property.
This is because higher stress values lead to crack formation, which acts as a point of fracture. Therefore, it is quite evident that a raster angle of 0 degrees provides the polymers with the highest fatigue strength, while the 90 degrees raster-oriented specimens had the lowest value of fatigue strength. Again, the Z-axis upright polymers had the worst bending fatigue strength limit as their layers experienced disintegration.
These results pose a serious question as to the properties and mechanical performance of Z-axis-oriented polymers.
Performance Review
The detailed performance analysis published in Polymers was able to identify key points regarding the raster orientation. The upright Z-axis samples, having the highest number of layers in their geometrical structure, also take a lot of time and resources for their synthesis.
The purging of layer tips is also an essential factor for this extended 3D printing time.
Although the test results for different 3D-printed samples are almost proportional, the Z-axis performance and mechanical analysis identify it as the weakest sample. The sudden separation of carbonate layers leads to brittle fractures in these vertically oriented samples, depicting its lower resistance properties to exerted stresses.
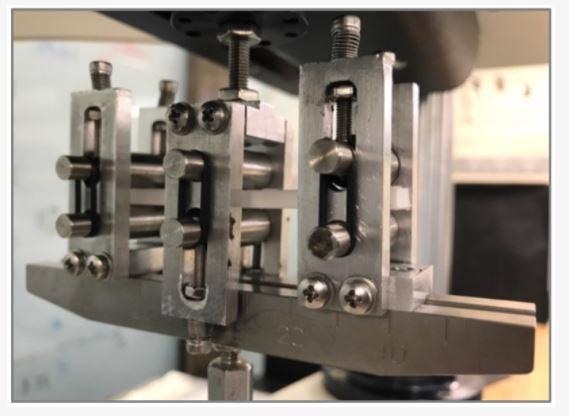
Experimental setup for ASTM D7774 three-point fatigue testing. Image Credit: Gras, G. G, Polymers.
The fatigue properties are extensively affected by the raster angle and axis orientation of the 3D printing of the polymer. The overall analysis of the mechanical performance and test results indicate the X-flat orientation to be the most mechanically reliable and have the greatest strength.
However, an essential point to be noted is that these properties are still far from well-known human bone properties. Hence, although the PC polymer has the certifications for biocompatibility doping with other elements or compounds, it is necessary for the enhancement of mechanical performance and increased reliability.
References
Gras, G. G., Abad, M. D., & Pérez, M. A. (2021, October 25). Mechanical Performance of 3D-Printed Biocompatible Polycarbonate for Biomechanical Applications. Polymers, 13(21).https://www.mdpi.com/2073-4360/13/21/3669
Disclaimer: The views expressed here are those of the author expressed in their private capacity and do not necessarily represent the views of AZoM.com Limited T/A AZoNetwork the owner and operator of this website. This disclaimer forms part of the Terms and conditions of use of this website.