The wind power industry is growing, and with it, a demand for parts that can be easily manufactured and recycled at the end of their life. A new project at the NREL in the US has developed a 3D printing method to manufacture turbine blades with recycled resin.
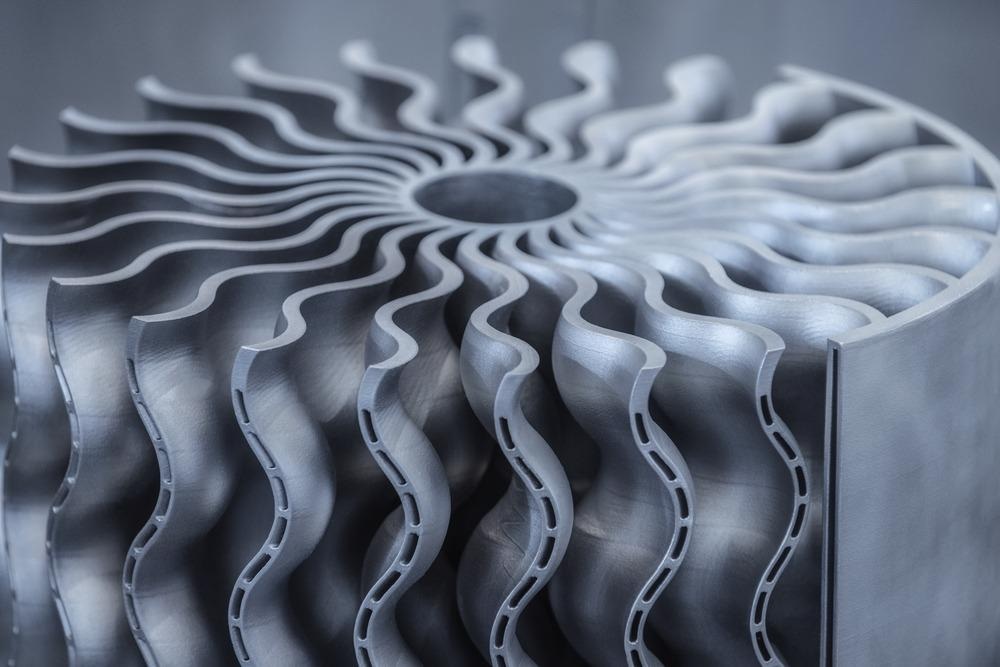
NREL Explores Innovative Manufacturing Approach for Next-Generation Wind Turbine Blades. Image Credit: Sergii Chernov/Shutterstock.com
The Problem with Current Wind Turbine Blades
Currently, utility-scale turbine blades are manufactured in a way that makes them hard to recycle, adding to the problem of industrial waste. The manufacturing method involves bonding two fiberglass skins together using thermosetting resins such as vinyl esters, polyesters, and epoxies that are irreversibly set due to their cross-links. This means that the plastic parts in the turbine blades cannot be recycled at the end of their life.
Whilst turbine blades have been designed with efficiency in mind, this process severely impacts the sustainability of parts in the wind power industry, which is at odds with the image of the renewable energy sector. If the parts in wind turbines cannot be retrieved for recycling, it still means that new ones need to be fabricated, leading to an increased need for resources.
President Biden strengthened the US commitment to sustainability and green technology by committing to substantially reducing the nation’s carbon emissions. Innovative approaches will be needed to achieve this goal, and researchers aim to revamp and revolutionize wind turbine manufacturing to realize more sustainable technology.
A New Approach
A team led by Derek Berry has developed a circular method for wind turbine manufacture. With backing from the US Department of Energy, the approach makes use of 3D printing technologies and recyclable thermoplastics to realize sustainable wind turbine blades.
By using 3D printing instead of traditional fabrication techniques, blades of a more advanced design with complex, highly engineered structures can be fabricated.
The internal structures have varying internal geometric arrangements and densities and have complex net-shaped structures between the skins of the blades. Furthermore, thermoplastic resins are used to join the parts together. Thermal welding is used to attach the recyclable thermoplastics together with applied pressure and heat, which further removes the use of conventional adhesives, which can be toxic and expensive.
A prototype blade measuring 13 meters has been built by Berry’s team using this innovative and novel process, with the aim of using the prototype to inform future blade design.
Advantages of the Technology
The technology has several advantages that help it overcome key critical issues in the industry. These include improved sustainability, cost reduction, and eliminating the need for toxic materials which are both harmful to health and the environment.
3D Printed Turbine Blades for More Efficient Power Generation | The Cool Parts Show #35
Video Credit: Additive Manufacturing Media/Youtube.com
In conjunction with their US partners, the team identified the possible cost and weight reductions in wind turbine manufacture of 10%. Lead times could be reduced by up to 15%. Lightweight, advanced 100-meter-long components (about the height of the Statue of Liberty) could be manufactured using this process.
Other Technologies Being Developed
Several other key research studies being developed at the moment have the aim of revolutionizing the wind turbine industry. These studies are exploring the application of 3D printing technologies, waste recycling, and the scalability of processes.
The University of Maine is developing sustainable 3D printing mold processes for wind turbines. Germany’s voxeljet and Fraunhofer IGCV are developing processes that will build 60t printed turbine blades. Researchers from Ryerson and McGill universities have announced a process that converts recycled parts into a printable PLA.
GE Research has announced the development of a printed blade tip that will be undergoing structural testing to explore fully-3D printed turbine blade technology.
The wind turbine industry will benefit greatly from the projects currently being undertaken by universities and commercial partners in the US currently, pointing the way toward a more ecologically friendly future for renewable energy generation using this abundant natural resource.
Moving Toward a More Sustainable Future
Whilst still a new area of research, the adoption of 3D printing by the wind turbine industry to create a more sustainable, circular manufacturing process for turbine blades has the potential to substantially improve sustainability and cost reduction in the sector. This can only be a good thing for the entire sector, helping the industry to provide clean energy without the production of harmful, hard to recycle industrial waste.
As the world moves away from fossil fuels and seeks to stave off the worst effects of climate change, innovative solutions will be needed to solve critical waste and resource issues. Advanced material-enhanced clean energy is an exciting direction for the renewable energy sector.
Further Reading
NREL.gov (2021) NREL Explores Innovative Manufacturing Approach for Next-Generation Wind Turbine Blades [online] nrel.gov. Available at:
Disclaimer: The views expressed here are those of the author expressed in their private capacity and do not necessarily represent the views of AZoM.com Limited T/A AZoNetwork the owner and operator of this website. This disclaimer forms part of the Terms and conditions of use of this website.